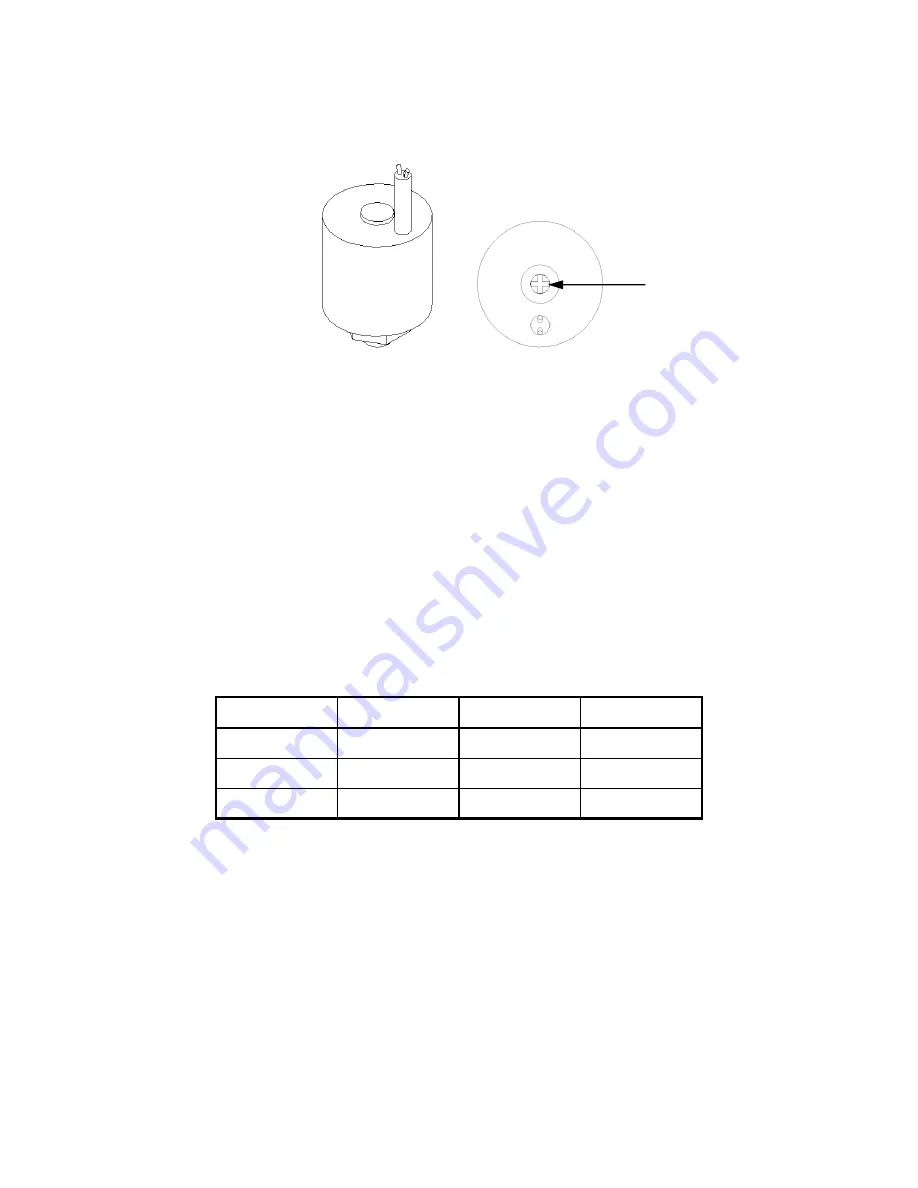
TC110 Series
Water Temperature Control Units 882.03888.00
•
09/19/2018
37
Figure 6: Pressure Switch - Side View and Top View
Under the plug is a Phillips-head adjusting screw:
Turn the screw counterclockwise to reduce the pressure.
- or -
Turn the screw clockwise to increase the pressure.
A quarter turn (90° rotation) approximates 15 psi (103 kPa/ 1.0 bar).
Replace the plug on the top of the switch.
If the plug gets damaged, the switch is still sealed internally.
Make sure that the high limit on the controller is set to the values listed in the following
table, based on the switch adjustment. This prevents the pump from cavitating and
damaging the seal, the switch, and heater element(s).
psig
kPa
Max. temp. °F
Max. temp. °C
5 psig
34 kPa
227°F
108°C
10 psig
69 kPa
240°F
116°C
15 psig
103 kPa
250°F
121°C
Safety Thermostat
Disconnect main power. Open the electrical enclosure and disconnect the neutral lead on
the safety thermostat from the terminal strip. Protect the stripped lead to prevent short
circuits. Close the enclosure, reconnect main power, and push the START button and press
ON/OFF switch to the ON position. The heater should not turn on and the Over
Temperature indicator should illuminate. Disconnect main power before reconnecting the
thermostat lead.
Phillips head screw