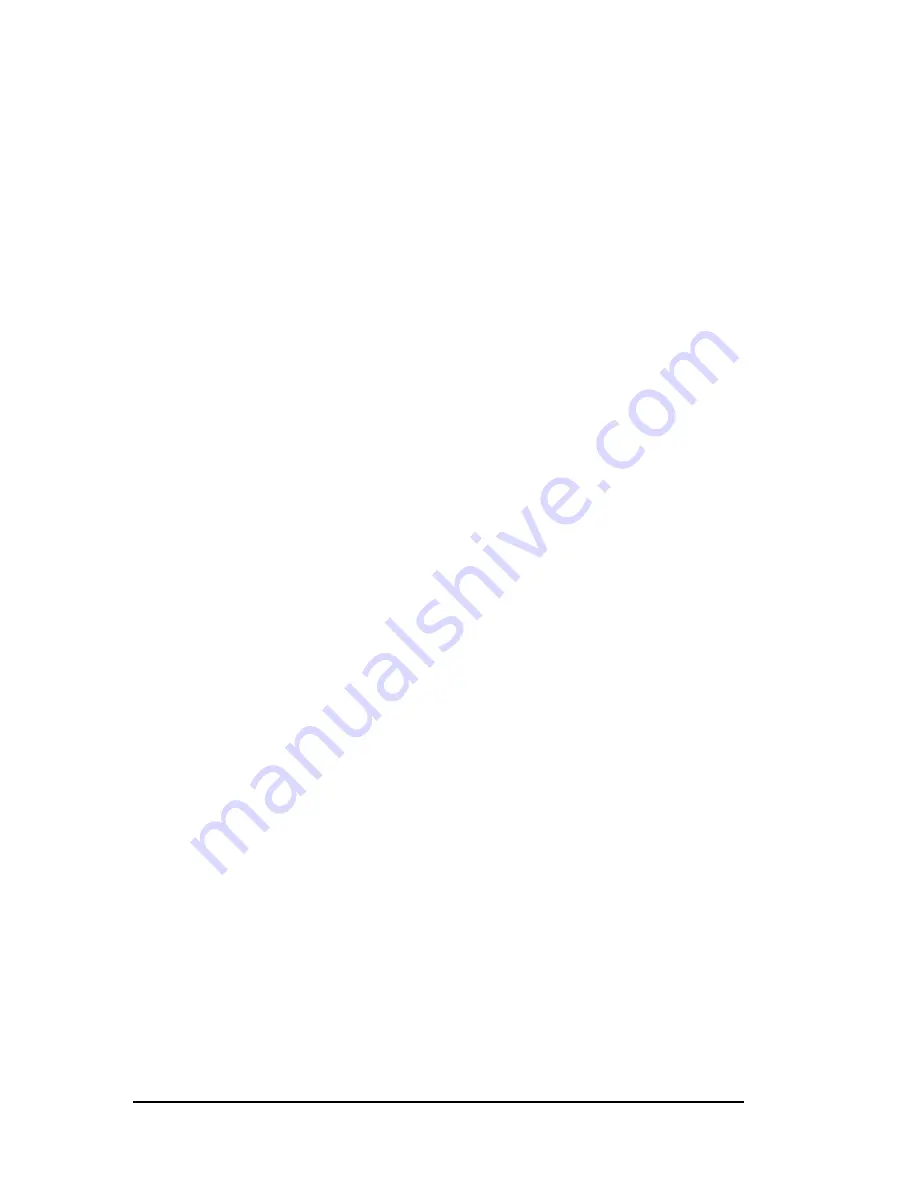
SERIES I/O SERVER MODULE
MIL-STD-1553A/B Bus Interface Module
________________________________________________________________________
15
Acromag, Inc. Tel:248-295-0310 Fax:248-624-9234 Email:[email protected]
www.acromag.com
To select the external time tag clock input as the Micro ACE time tag clock: write bits
TTR2:0 in configuration register #2 with the bit pattern “111”. Write the tag clock source
(bit 7) of the IOS I/O space control register with the value 1.
Note: the selection of tag clock source in the IOS I/O space control register will affect both
1553 channels of an IOS-572 module.
STATIC MICRO ACE INPUTS
The SUBSYSTEM/EXT_TRIG Micro ACE input signal is permanently connected to logic 1
in the FPGA. The functions controlled by this static input signal have alternate methods of
control through host writes to Micro ACE registers. The subsystem flag bit can be set by
the host writing to bit 8 of Configuration Register #1 in RT mode. In BC mode, a frame can
be started by writing bit 1 of the Start/Reset Register with the value 1.
REMOTE TERMINAL ADDRESS
The RT address and parity signals for each of the 1553 channels are available at the P2
connector. Each of the signals has an adjacent ground signal on the connector for
convenient programming of the RT address through an attached wire harness. Each of the
address lines and parity bit has a pull up resistor on it. An unconnected input results in that
bit reading as logic 1. Grounding the input causes the bit to read as logic 0. The RT
address parity is odd, so the sum of the RT address input bits and the RT parity bit must be
odd. The RT address may be latched in the Micro ACE. The RT address latch signal is
controlled by the IOS I/O control register. Bit 9 controls the RT address latch signal for
channel 1, bit 1 controls the RT address latch signal for channel 0.
See section 6.29 RT Address Inputs of the Enhanced Mini-ACE® Series Users Guide for a
complete description of the options available for setting the RT address.
BUS CONNECTION
The IOS-57x modules may be connected to the1553 bus using either of two methods:
direct coupled (short stub) or transformer coupled (long stub). Both of these connection
methods are provided for both of the dual redundant (A and B) channels of each of the
1553 channels (0 and 1).
DIRECT COUPLING METHOD
Using the direct coupling method the IOS-57x module may be connected to the
1553 bus without any additional components. The transformer and isolation
resistors are included on the IOS-57x. The stub length may not exceed 1 foot.
The distance the signals travel across a carrier board must be subtracted from the
1 foot maximum length.
TRANSFORMER COUPLING METHOD
Using the transformer coupling method, stub lengths may be up to 20 feet. With
this method the IOS-57x does not connect directly to the 1553 bus. The IOS-57x
must connect to the bus through a bus coupler.
Transformer coupling provides improved thermal performance when compared with direct
coupling since the heat dissipated in the isolation resistors is located outside of the I/O
Server.
SERVICE AND REPAIR
Surface-Mounted Technology (SMT) boards are generally difficult to repair. It is highly
recommended that a non-functioning board be returned to Acromag for repair. The board
can be easily damaged unless special SMT repair and service tools are used. Further,