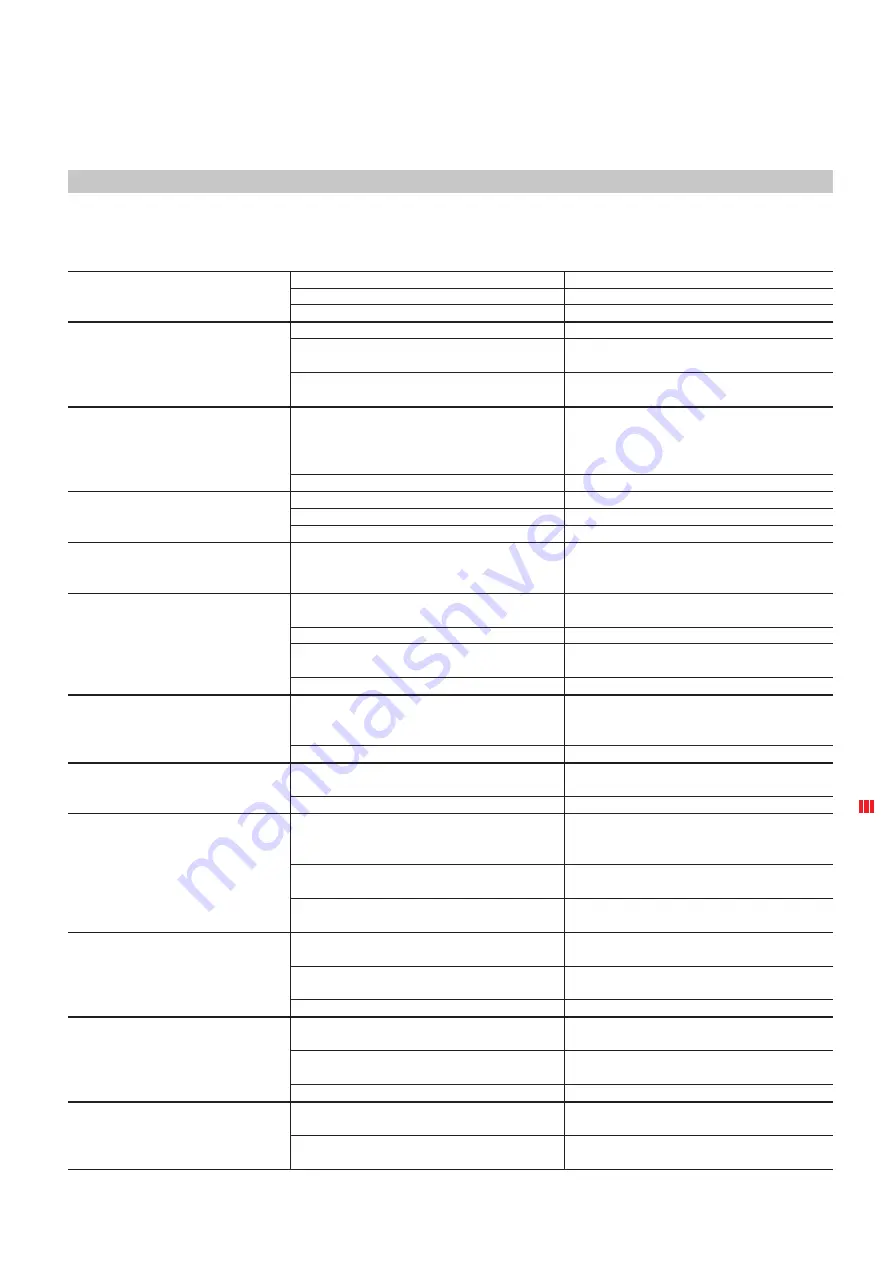
Fault
Possible cause
Remedy procedure
19
Operation manual
ACO Clara
An overview of possible faults of the technological plant equipment and
how they can be remedied can be found in the following table:
7
Troubleshooting
1.
2.
3.
4.
5.
6.
7.
8.
9.
10.
11.
12.
Blower does not work (no
motor noise).
Blower undercapacity (weak
aeration of activation, underca-
pacity of air-lift pumps).
Inadequate aeration of activati-
on (visually weak intensity of
tank agitation), or irregular
bubbles, but air-lift pumps are
running.
Some air-lift pumps do not
work.
The air-lift pump for pumping
raw water from the pretreat-
ment does not work repeatedly.
The plant smells strongly.
Repeated occurrence of floating
sludge in final sedimentation
tank.
The plant does not reach the
required purification efficiency.
The escape of flakes of activa-
ted sludge from the final sedi-
mentation tank to the outlet.
During sedimentation test no
deposit of activated sludge
occurred.
During sedimentation test no
sludge occurs in sample.
Abnormal occurence of foam on
water in activation tank.
Failure of circuit breaker for connection.
Disconnected or faulty socket for connection.
Faulty blower.
Clogged blower filter.
Disconnected air supply to air distributor, air-lift
pumps or aeration elements.
Blower defect (abnormal wear of membrane/lamella,
defect of blower aggregate).
Aeration elements and distribution line filled up with
condensate.
Fault of aeration elements.
Disconnected or clogged air supply to air-lift pump.
Clogged nozzle of air supply to air-lift pump.
Clogging of air-lift pump.
The layer of sludge in the sedimentation tank is so
high that the sludge overflows the partitions to the
air-lift pump.
Wrong function of ventilation of inner plant space.
Inadequate function of ventilation unit.
The plant is loaded with waste water above the
design value.
Other causes.
No observing of instructions for operation and main-
tenance (high concentration of sludge in activation
tank…).
Other cause.
Failure to observe instructions for operation and
maintenance.
Other causes.
The plant is hydraulically overloaded.
Result of inflow of harmful substances.
Other causes or failure to follow instructions for
operation and maintenance.
Result of inflow of harmful substances.
High concentration of activated sludge.
Other cause.
Low concentration of activated sludge.
The sludge was not developed because of low plant
load.
Other cause.
Result of inflow of harmful substances.
Increase of fibrous organisms.
Switch on the circuit breaker.
Reconnect the socket or ensure specialized repair.
Ensure specialized repair of blower – see Chap. 9.
Clean the blower filter – see Chap. 9.
Repair the line for air supply.
Ensure specialized repair of blower – see Chap. 9.
Make condensate outlet. If the condensate outlet
cannot be made or ensured, remove aeration ele-
ments and check them – see Chap. 6.4.14.
Replace aeration elements – see Chap. 6.4.14.
Repair the line for air supply.
Clean the nozzle.
Clean the air-lift pumps – see Chap. 6.4.13.
Pump the sludge from the sedimentation tank – see
Chap.6.4.11 and clean the air-lifts – see Chap.
6.4.13.
Provide ventilation for the inner plant space – see
chap. 5.3.
The same procedure as in faults 2 and 3.
Ensure technical expertise of qualified worker.
Ensure technical expertise of qualified worker.
Observation of instructions specified in Section 6.
Ensure technical expertise of qualified worker.
Observation of instructions specified in Section 6.
Ensure technical expertise of qualified worker.
Check the functioning of the air-lift pump for raw
sewage water. Find the source of the abnormal
supply of waste water.
Eliminate inflow of harmful substances, ensure tech-
nical expertise of qualified worker.
Ensure technical expertise of qualified worker.
Eliminate inflow of harmful substances; ensure tech-
nical expertise of qualified worker.
Observe instructions for removal of surplus sludge;
see Chap. 6.4.10.
Ensure technical expertise of qualified worker.
Observe instructions for removal of surplus sludge;
see Chap. 6.4.10.
Minimal mass load on plant makes 40% of designed
capacity.
Ensure technical expertise of qualified worker.
Eliminate inflow of harmful substances, break up the
foam with a stream of water.
Break up the foam with a stream of water, ensure
technical expertise of qualified worker.
Содержание ClarA 19-38
Страница 1: ...Waste water treatment plant ACO ClarA 19 38 24 48 30 60 38 76 48 96 60 100 Operation manual ...
Страница 28: ...28 Operation manual ACO Clara F2 F1 OFF O 0 OFF A C D B ...
Страница 29: ...29 Operation manual ACO Clara 3000 h 27 5mm DT 4 25 No 27 5mm 28mm DT 4 40 No 28mm xxxx H E F G ...
Страница 32: ...32 Operation manual ACO Clara p VACUUM p PRESSURE OFF O 0 OFF A C 1 C 2 B ...
Страница 33: ...33 Operation manual ACO Clara No D H XXXXX F D 1 D 2 E ...
Страница 36: ...36 Operation manual ACO Clara PRESSURE p p VACUUM OFF O 0 OFF A C 1 C 2 B ...
Страница 37: ...37 Operation manual ACO Clara D 75 mm H 170 mm No 909568 No D xxxx H p VACUUM PRESSURE p F D 1 D 2 E ...