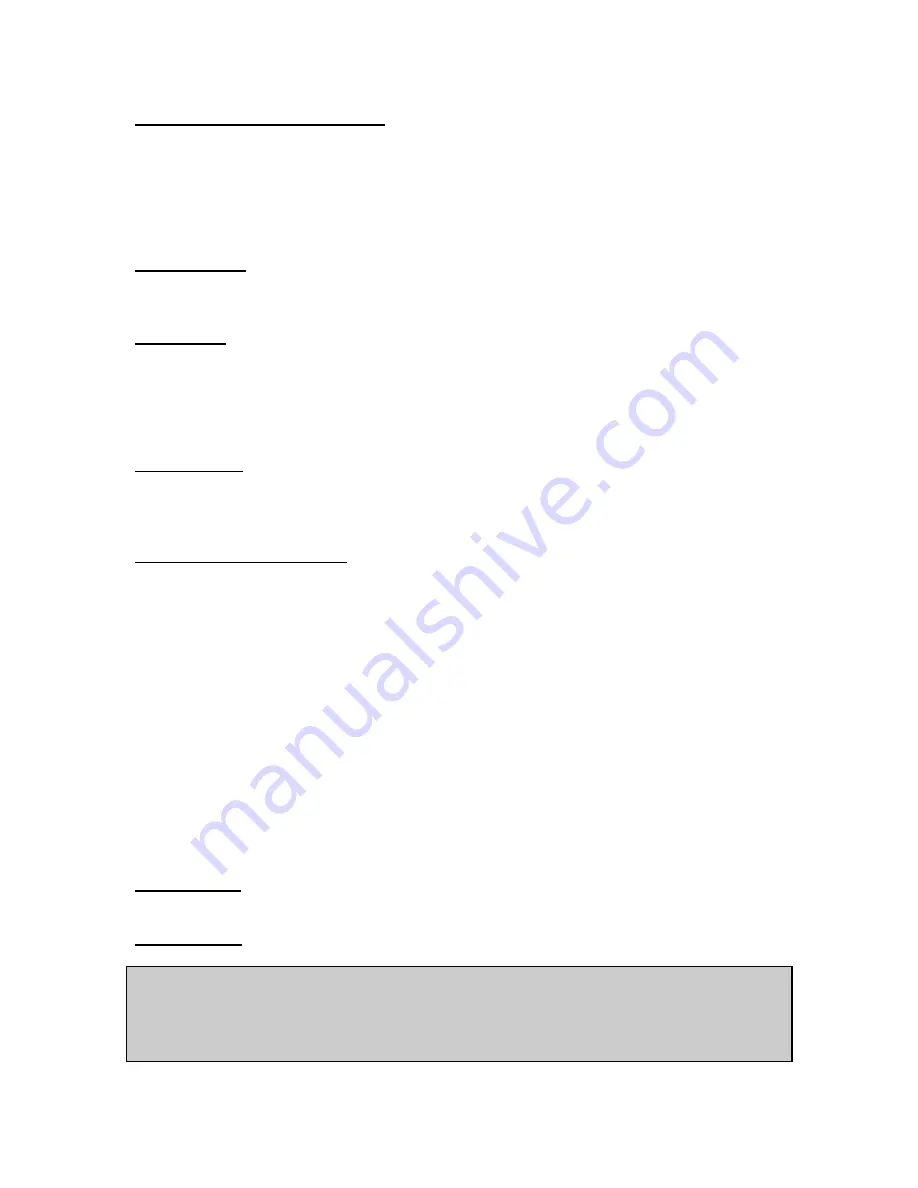
14
Driveshaft Speed (VSS) Input
– Receives information from a speed sensor located
on the driveshaft. Multiple tooth sensors can be used to increase resolution and
accuracy by adjusting the Number of Pulses/Revolution setting located in the
configuration page of the DataMap software. A Hall Effect type (3-wire), or Variable
Reluctance-IPU type (2-wire) sensor can be used with this controller by setting
Dipswitch #5 on the Printed Circuit Board to the appropriate position. See Driveshaft
Signal type on Page 16 of this manual to properly configure this feature.
HEGO Output
– Mimics the output of a conventional narrow-band oxygen sensor. A
0.1 volt output is the leanest possible reading, and a 0.9 volt output is the richest
possible reading.
Main +12V
– Voltage source for the controller. This wire should be connected to a
sw12V source for the controller to operate. If you are NOT connecting this
controller to an Accel DFI Gen 7+ Engine Management system, it is recommended to
install a 30-amp fuse on this line for short circuit protection. Note that on some
models, this input must remain powered until data is read from the integrated
internal data logger or else the stored data will be lost.
12V
– Power source for the heater element inside the oxygen sensor,
must be properly connected for sensor to operate. For units with Firmware versions
2.0.0 and higher, this wire is replaced by the Keep-Alive Voltage Input, and heater
voltage is drawn from the Main +12 Volt input.
Keep-Alive Voltage Input
– Connect this wire to an auxiliary voltage source to
retain the contents of the Data Logger memory after the Main +12 Volt input is
switched off. Any logged data will be preserved as long as at least 9 volts are
supplied to this input, regardless of the state of the Main +12 Volt input line.
Dual Channel models are also equipped with a memory backup that allows the Data
Logger to retain the contents of its memory after the device is disconnected from
any main or auxiliary voltage supply. Data can be retained for approximately 48
hours before power must be reapplied to the Keep-Alive input wire.
Single Channel units with Firmware versions less than 2.0.0 cannot fully use the
Keep-Alive Voltage input wire. In those units, the keep-alive wire is internally tied to
the Main +12 Volt input. You must keep those units fully powered until the logged
data can be downloaded to your computer. Connection of this wire to a +12 volt
supply may require a 1N4007 (or equivalent) Diode to be placed inline with the Main
+12 Volt supply wire to prevent back feeding of voltage to the switched source.
Place the Diode with the negative side pointing toward the Engine Analyzer module.
Data Ground
– Ground source for the communication circuit between the controller
and the laptop PC being used to configure it.
Main Ground
– Ground source for the controller’s main power supply.
If not connecting this controller to an Accel DFI Generation 7+ Engine Controller
harness, make sure to connect this wire to an adequate ground source. As with any
electronic equipment in your car, the negative battery terminal is the recommended
grounding point. Inadequate grounding of electronic equipment such as this can
result in equipment malfunction or damage!