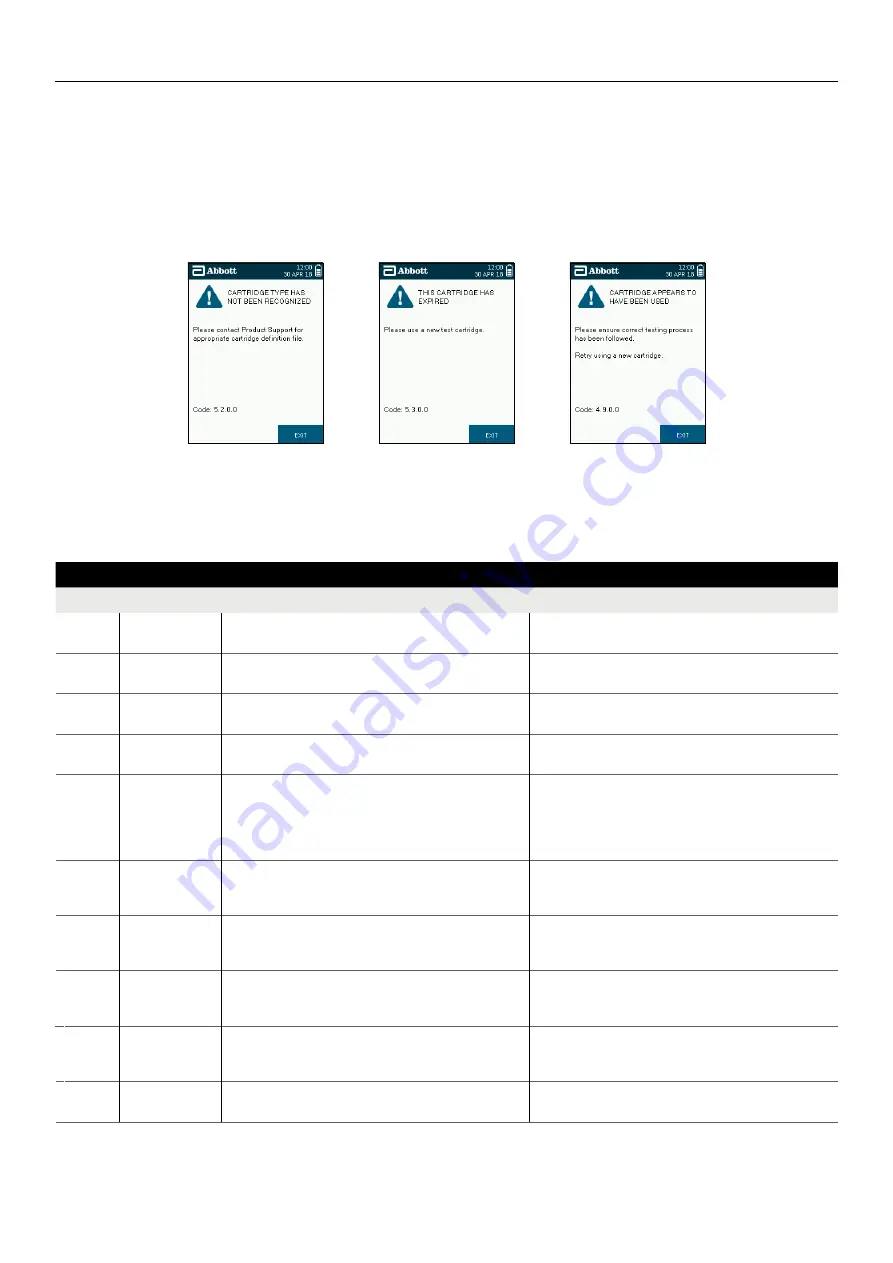
SOTOX A™ MOBILE ANALY ZER | USER GUIDE
29 | EN
11. TECHNIC AL SUPPORT, CODES AND TROUBLESHOOTING
11.
Technical Support, Codes and Troubleshooting
11.1
Technical support
In the event of an incomplete test or SoToxa™ Mobile Analyzer issue on-screen feedback will be provided, in most cases, to the user to assist
with diagnosis and resolution of the issue. In some cases, the analyzer will report specific codes – please refer to the list of codes on the
following pages for interpretation. If the issue cannot be resolved using this guide, please contact Customer Service.
Examples of screens:
11.2
Codes and troubleshooting
Please note, the codes listed below are examples. When displayed by the SoToxa™ Mobile Analyzer, the characters denoted by ‘X’ will be
numbers. The first and second numbers are used to denote the type of code.
CODES AND TROUBLESHOOTING
Code
Description
Possible cause
Solution
1.1.X.X to
1.5.X.X
Cartridge analysis
incomplete.
The test cartridge was not detected correctly. Can be due to
dirty optics, a damaged test cartridge or a hardware fault.
Initiate a QC test, if the QC test fails contact Customer
Service. If the QC tests pass complete the test.
1.6.X.X
Insufficient
sample.
The reference band has not been detected; the sample has not
run on the test cartridge.
Ensure that the test process has been correctly followed.
1.7.X.X
Insufficient
sample.
The sample has not run sufficiently on the test cartridge. Can
be due to insufficient sample collection, incorrect test process.
Ensure that the test process has been correctly followed.
1.8.X.X to
1.10.X.X
Cartridge analysis
incomplete.
The test cartridge was not detected correctly. Can be due to
dirty optics, a damaged test cartridge or a hardware fault.
Initiate a QC test, if the QC test fails contact Customer
Service. If the QC tests pass complete the test.
2.1.X.X to
2.6.X.X
Cannot read
barcode.
During the barcode analysis the analyzer has detected a fault
this could be due to the cartridge/barcode being damaged, dirty
optics or a hardware fault.
Initiate a QC test. If the QC test passes, verify that the
inserted test cartridge is not used and its barcode is not
damaged. If the test cartridge or its barcode is damaged,
dispose of the test cartridge and start a new test with a new test
cartridge. If the QC test fails, contact Customer Service.
2.7.X.X
Barcode
not valid.
The barcode data cannot be interpreted into valid cartridge
information. The barcode may have been tampered with or a
newer barcode version has been introduced.
Please contact Customer Service for assistance.
3.1.X.X
and
3.2.X.X
Issue detected
with hardware.
Analyzer hardware issue.
Unable to complete test process. Please contact Customer
Service for assistance.
3.3.X.X
Analyzer
calibration
required.
The analyzer appears not to be calibrated or has lost its
calibration settings.
Tests cannot be completed until the analyzer is calibrated.
Contact Customer Service for assistance.
3.4.X.X
and
3.5.X.X
Test result
inconclusive.
Issue detected during the test analysis, analyzer unable to
interpret the result.
Restart analyzer and start test process again if applicable.
3.6.X.X
Start-up checks
have failed.
The analyzer has detected a fault during the initial checks and
will not be able to complete a test.
Unable to complete test process. Contact Customer Service
for assistance.