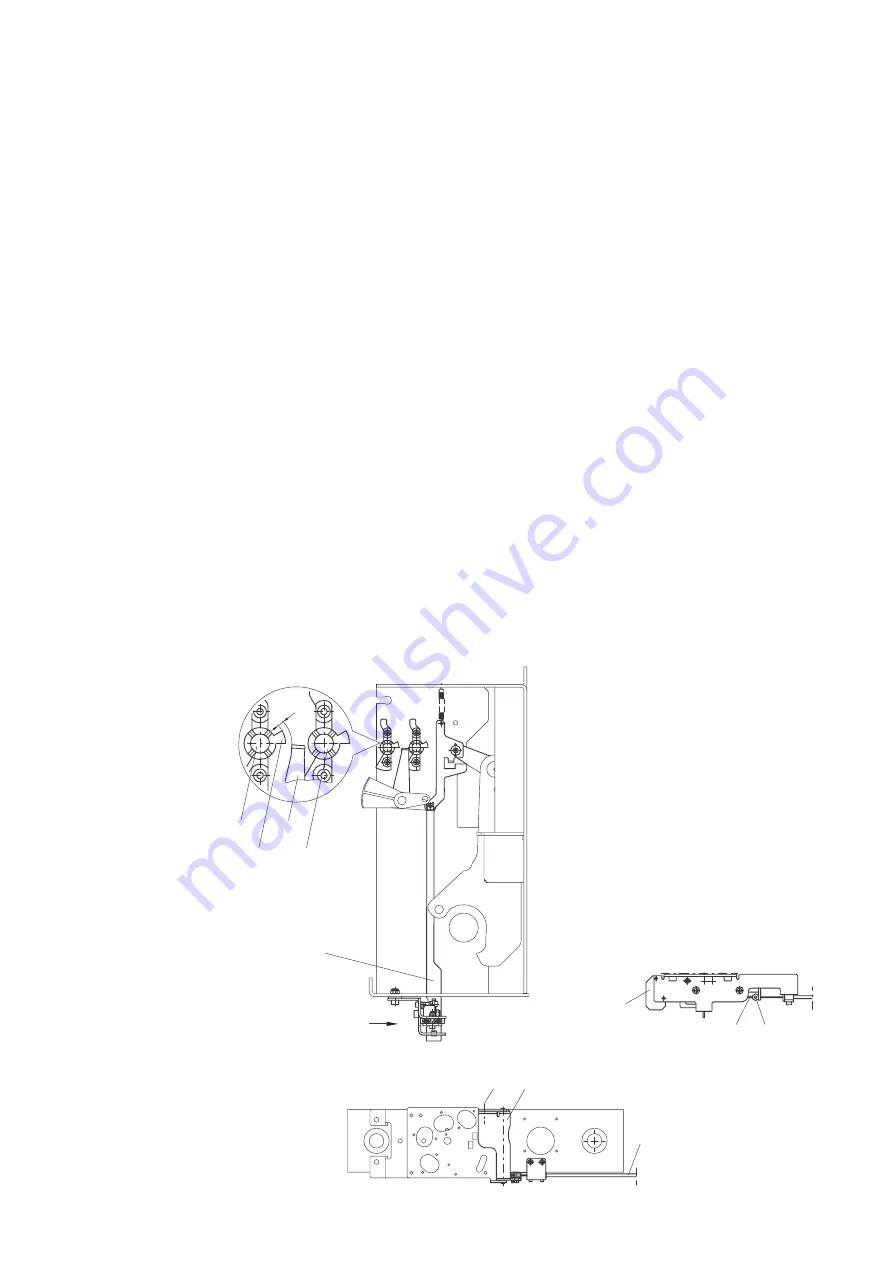
42
ZX1.5-R
I N S T R U C T I O N M A N U E L
Maintenance serves to preserve trouble-free
operation and achieve the longest possible
working life of the switchgear.In accordance
with DIN 31 051 and IEC 62271-1, it comprises
the following closely related activities:
Inspection:
Determination of the actual condition
Servicing:
Measures to maintain the specified
condition
Repair:
Measures to re-establish the specified
condition
7.1 General
It is essential to observe the following during
all maintenance work:
•
The relevant regulations in section 1.2.2
•
The notes on safety at work in section 6
•
Standards and specifications in the country
where the switch gear is erected
It is recommended that ABB after sales service
personnel be called in to perform servicing and
repair work.
Follow/observe the instructions on SF
6
systems
and the ABB instruction manual on the handling
of insulating gases and procedures for fault
conditions.
•
Keep these instructions and manual permanently
on display and available in the switchroom
The inspection and servicing intervals for the
switching devices are determined by fixed criteria
such as switching frequency and number of
short-circuit breaking operations.
The length of the intervals for inspection and
servicing of the control cabinet and its equipment
is influenced by ambient conditions (for instance
pollution and aggressive atmosphere).
7.2 Inspection/servicing
•
Under normal operating conditions (see section
1.3), inspection (visual examination) of the
operating mechanisms is to be carried out bya
suitably qualified electrician after 5,000 operating
cycles of the circuit breaker and 1,000 operating
cycles of the three position switch. Attention is
also drawn to instruction manual 1YHA000118
•
In exceptional operating conditions (including
adverse climatic conditions) and/or particularly
adverse environments (including heavy
contamination and aggressive atmosphere)
inspection at shorter intervals may be required
•
Inspection is first and foremost to be visual
examination for contamination, corrosion
and moisture
•
The inspection should however also include
checking of the mechanical and electrical
functions of the following devices
-
Switching devices
-
Multifunction protection and switchbay
control unit.
•
If an incorrect condition is found, the
corresponding repair work is to be initiated
immediately
Cleaning of external surfaces
•
Remove dry, poorly adhering dust deposits with
a soft, dry cloth
•
Clean off more strongly adhering dirt with slightly
alkaline household cleanser and a moist cloth,
not allowing any liquid to penetrate inside the
low voltage compartment and the operating
mechanism bays. Observe the manufactures
instruc tions for cleaning of the front surfaces
of the equipment installed in the door
7.2.1 Vacuum circuit breaker
•
The vacuum circuit breaker has a long service life.
It has a low maintenance operating mechanism
and the breaker poles are maintenance-free
Consult the relevant sections of instruction
manual BA 463/E for further information.
7.2.2 Three-position switch
•
The three-position switch is maintenance-free
for 2000 operating cycles
7.2.3 Gas system and gas servicing
•
Consult the relevant sections of instruction
manual for further information
•
Caution when working in the gas
compartment con cerned! The gas
concentration may causea danger of
asphyxiation!
Circuit breaker compartment
Circuit breaker
Circuit breaker operating mechanism
Pressure relief disk, above
Test socket
Blind plug
Measuring sockets for capacitive voltage
indicator
Plug-in cable socket
Pressure sensor for circuit breaker
compartment
Pressure relief duct (optional)
Absorber (optional)
Drying agent bag, circuit breaker
compartment
Bushing circuit breaker compartment /
busbar compartment
Filling valve for circuit breaker compartment
Protection cover for current transformer
terminal board
Cover for metering cables
Handling bracket (to be removed after
handling)
Edge protection
Socket head screw M 8x25
Hexagon nut M 8
Dished washer8
Centre of gravity
ON-release shaft
OFF-release shaft
Cam
Mechanical interlock circuit breakerr/
three-position switch
Lever
Clamping piece
Clamping screw
Tee-off conductor, bus-coupler
Tee-off conductor bus-riser
Front plate
On push button
OFF push button
Operating cycle counter
Mechanical position indicator
Rating plate
Charging condition indicator
Recess for charging lever (6.3)
Terminal board for current transformer
Auxiliary switch
Busbar compartment
Three-position switch
Three-position switch operating
mechanism
Pressure sensor for busbar compartment
Busbar
Plug-in busbar connector
Tee-off conductor, metering panel
1.0
1.1
1.2
1.3
1.4
1.5
1.6
1.7
1.8
1.9
1.10
1.11
1.12
1.14
1.16
1.17
1.18
1.19
1.20
1.21
1.22
1.23
1.24
1.25
1.26
1.27
1.28
1.29
1.30
1.31
1.32
1.33
1.34
1.35
1.36
1.37
1.38
1.39
1.40
1.41
1.42
2.0
2.1
2.2
2.3
2.4
2.5
2.6
Support
Plug-in socket for voltage transformer
Isolating system for voltage transformer
Tee-off conductor
Pressure relief disk for busbar
compartment
Drying agent bag, busbar compartment
Busbar socket
Insulating part
O-Ring
Socket head bolt M 10x50
Guide pin
Hexagon nut M 10
Dished washer 10
Socket head bolt M 10
Bus connector
Flap
Bore for padlock
Central gas connector for busbar
compartment
Drive motor for three-position switch
Hollow shaft (emergency manual
operation shaft)
Mechanical switch position indicator
Sensor, disconnector ON
Sensor, disconnector OFF
Sensor, earthing switch ON
Sensor, earthing switch OFF
Bore for padlock
Contact ring
Manual drive for isolating device
Tie wire
Auxiliary switch
Microswitch, disconnector on
Microswitch, disconnector off
Microswitch, earthing switch off
Microswitch, earthing switch on
Blocking magnet
Slide (mechanical operation circuit
breaker ON)
Cable termination compartment
Main earthing bar
Panel / panel connecting link
Cable mounting (optional)
Cable plug
Pressure relief flap, optional
Lower pressure relief duct
High voltage cable
Parallel connector PB50,
GCE 0909125P0100
Floor plate splitted
Reducer ring
Cable mounting
Supporting section, at earth potential
Rear panel compartment
Supporting section, at earth potential
Pressure relief flap, optional
Socket for fully insulated bar
Fully insulated bar
Venti lator
Control cabinet
Central unit of the Bay Control and
Protection Unit
HMI of the Bay Control and Protection Unit
Control cabinet door
Door-lock
Measuring sockets for capacitive
voltage indicator, optional
Light-emitting diode (LED)
LC-Display of the Bay Control and
Protection Unit
Closing lever
Double bit lock or security lock
Measuring facilities
Current transformer
Plug-in voltage transformer
Block-current transformer
Terminal board for current transformer
Accessories
Hand crank
Double bit key
Charging lever for emergency manual
operation
Test plug for high voltage tests, optional
Test plug for current tests, optional
2.7
2.8
2.9
2.10
2.11
2.12
2.13
2.14
2.15
2.16
2.17
2.18
2.19
2.20
2.21
2.22
2.23
2.24
2.25
2.26
2.27
2.28
2.29
2.30
2.31
2.32
2.33
2.34
2.35
2.36
2.37
2.38
2.39
2.40
2.41
2.42
3.0
3.1
3.2
3.3
3.4
3.5
3.6
3.7
3.8
3.9
3.10
3.11
3.12
3.13
3.14
3.15
3.16
3.17
3.18
4.0
4.1
4.2
4.3
4.4
4.5
4.6
4.7
4.8
4.9
5.0
5.1
5.2
5.3
5.4
6.0
6.1
6.2
6.3
6.4
6.5
Foundation frame
Longitudinal bracket, (this one for panel
width 600 mm)
Longitudinal bracket, internal (this one
for panel width 600 mm)
Transverse bracket, left (this one for
panel depth 1300 mm)
Transverse bracket, right (this one for
panel depth 1300 mm)
Fixing angle bracket
Connecting link
Transverse bracket for two panel frame,
(this one for panel depth 1300 mm)
Connecting angle
Screwed connection for foundation frame
Socket head bolt M 8x25
Socket head bolt M 10x25
Socket head bolt M 8x25
Socket head bolt M 8x25, frame height 40 mm
Socket head bolt M 8 x 35, frame height
50 mm
Partition plate
Dished washer8
Dished washer 10
Washer8
Nut M10
Fixing dowel
7.0
7.1
7.2
7.3
7.4
7.5
7.6
7.7
7.8
7.9
7.10
7.11
7.12
7.13
7.14
7.15
7.20
7.21
7.22
7.23
7.30
•
Sealed pressure system according to IEC 62271-1
SF
6
gas contained in this system shall be recycled
and not released into the atmosphere.
7.3 Repair
7.3.1 Replacement of drive mechanism parts and
accessories
Only remove and reassemble drive mechanism
parts and accessories when the breaker has been
switched off and the working area is to be isolated
and secured against reclosing. The spring energy
store must be discharged.
All supply voltage sources must be disconnected
and secured against reclosing during the removal
and installation work.
7.3.2 Checking the dimensional accuracy of the
settings (Figure 7/1)
After work which may be necessary on the circuit
breaker or three-position switch when the optional
mechanical interlock is fitted, the following checks
are necessary:
•
The distance between lever (1.28) operated bya
link rod and plastic cam (1.26) is to be 2
+1
mm
•
There must be space between lever (1.28) and
OFF release shaft (1.25)
•
If correction is necessary,tie wire (2.35) is to
be adjusted:
-
Release clamping screw (1.30) on clamping
piece (1.29)
-
Align flap (2.22) in such a way that the two
bores (2.23) are in alignment
-
Fasten tie wire (2.35) with clamping screw
(1.30) in such away that the
abovementioned distance of 2
+1
mm is
achieved. The tie wire must not be tensioned
7.3.3 Touch up of surfaces
•
Sheet steel parts, painted
-
Remove rust, e.g. with a wire brush
-
Grind off paint coat and grease
-
Apply anti-rust primer and top coat
-
Use top coat paint in the standard colour
RAL 7035, or the relevant special colour
•
Sheet steel parts, with aluminium-zinc surface
and passivated functional parts
-
Remove white rust with a wire brush or
cleaning pad (e.g. Scotch-Brite white)
-
Remove loosely adhering particles with a
dry cloth
-
Apply zinc spray or zinc dust primer
•
Functional parts, phosphated
-
Remove rust with a wire brush or cleaning
pad (e.g. Scotch-Brite white)
-
Clean with a dry cloth
-
Grease with Isoflex Topas NB 52
1.42
2
1
+
X
1.28
X
1.24
1.25
1.26
1.27
1.29
1.30
2.23
2.22
2.35
b) Three- position switch, front view
a) Circuit breaker, side view
—
Figure 7/1: Interlock
between the circuit
breaker and the
three-position switch
Figure 7/1
Содержание ZX1.5-R
Страница 2: ......