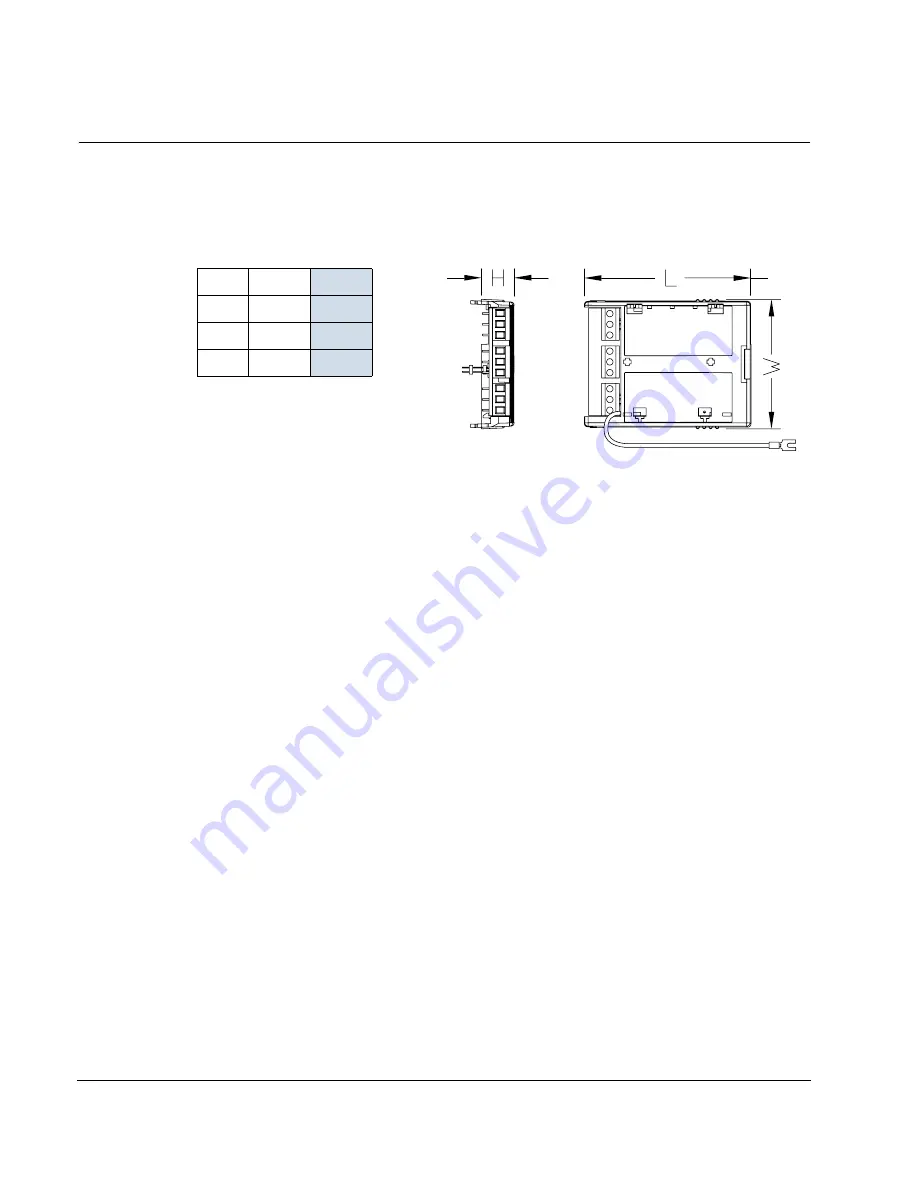
18
Technical Data
Technical Data
Dimensions
Module dimensions are:
Enclosure Degree of Protection
The module is mounted inside the drive enclosure. Refer to the drive’s
rating.
Ambient Conditions
The module is mounted inside the drive enclosure. Refer to the drive’s
requirements.
Connectors
Connectors on the module:
• 6-pin connector
• Three, 3-pin, screw-type, non-detachable terminal blocks that accept
wire connectors up to 1.5 mm
2
(16 AWG).
• Ground lead
Ref.
mm
in
H
14.5
0.57
L
77.8
3.06
W
58.8
2.31
X0063
Phone: 800.894.0412 - Fax: 888.723.4773 - Web: www.clrwtr.com - Email: [email protected]