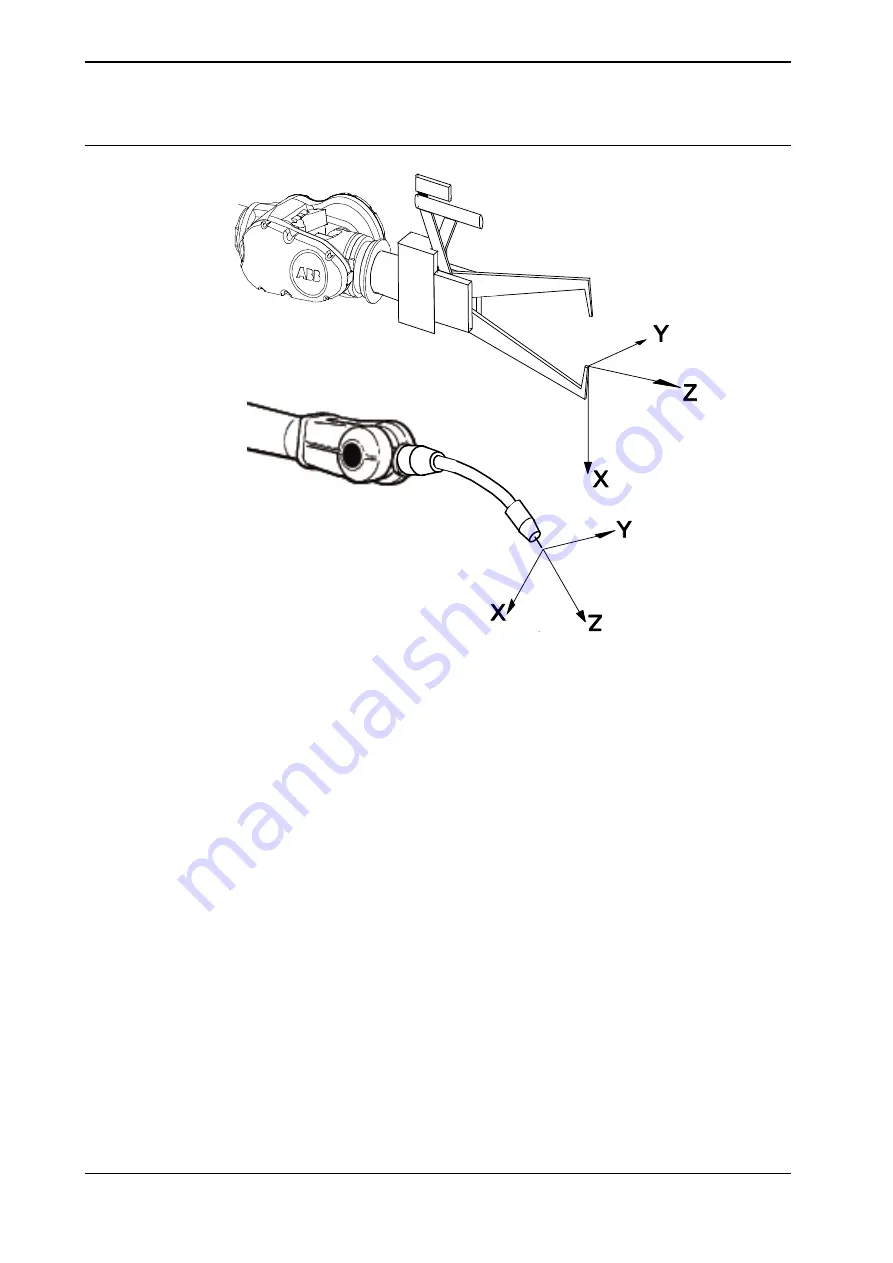
The tool coordinate system
The tool coordinate system has its zero position at the center point of the tool. It
thereby defines the position and orientation of the tool. The tool coordinate system
is often abbreviated TCPF (Tool Center Point Frame) and the center of the tool
coordinate system is abbreviated TCP (Tool Center Point).
It is the TCP that moves to the programmed positions, when executing programs.
This means that if you change the tool (and the tool coordinate system) the robot’s
movements will be changed so that the new TCP will reach the target.
All robots have a predefined tool coordinate system, called
tool0
, located at the
wrist of the robot. One or many new tool coordinate systems can then be defined
as offsets from
tool0
.
When jogging a robot the tool coordinate system is useful when you don’t want to
change the orientation of the tool during the movement. For example, moving a
saw blade without bending it.
Following is an example of tool coordinate system in use:
•
Use the tool coordinate system when you need to program or adjust
operations for threading, drilling, milling, or sawing.
Continues on next page
78
Operating manual - OmniCore
3HAC065036-001 Revision: J
© Copyright 2019-2021 ABB. All rights reserved.
5 Jogging
5.2 Coordinate systems for jogging
Continued
Содержание OmniCore
Страница 1: ...ROBOTICS Operating manual OmniCore ...
Страница 2: ...Trace back information Workspace 21D version a1 Checked in 2021 11 26 Skribenta version 5 4 005 ...
Страница 8: ...This page is intentionally left blank ...
Страница 24: ...This page is intentionally left blank ...
Страница 62: ...This page is intentionally left blank ...
Страница 72: ...This page is intentionally left blank ...
Страница 98: ...This page is intentionally left blank ...
Страница 234: ...This page is intentionally left blank ...
Страница 242: ...This page is intentionally left blank ...
Страница 264: ......
Страница 265: ......