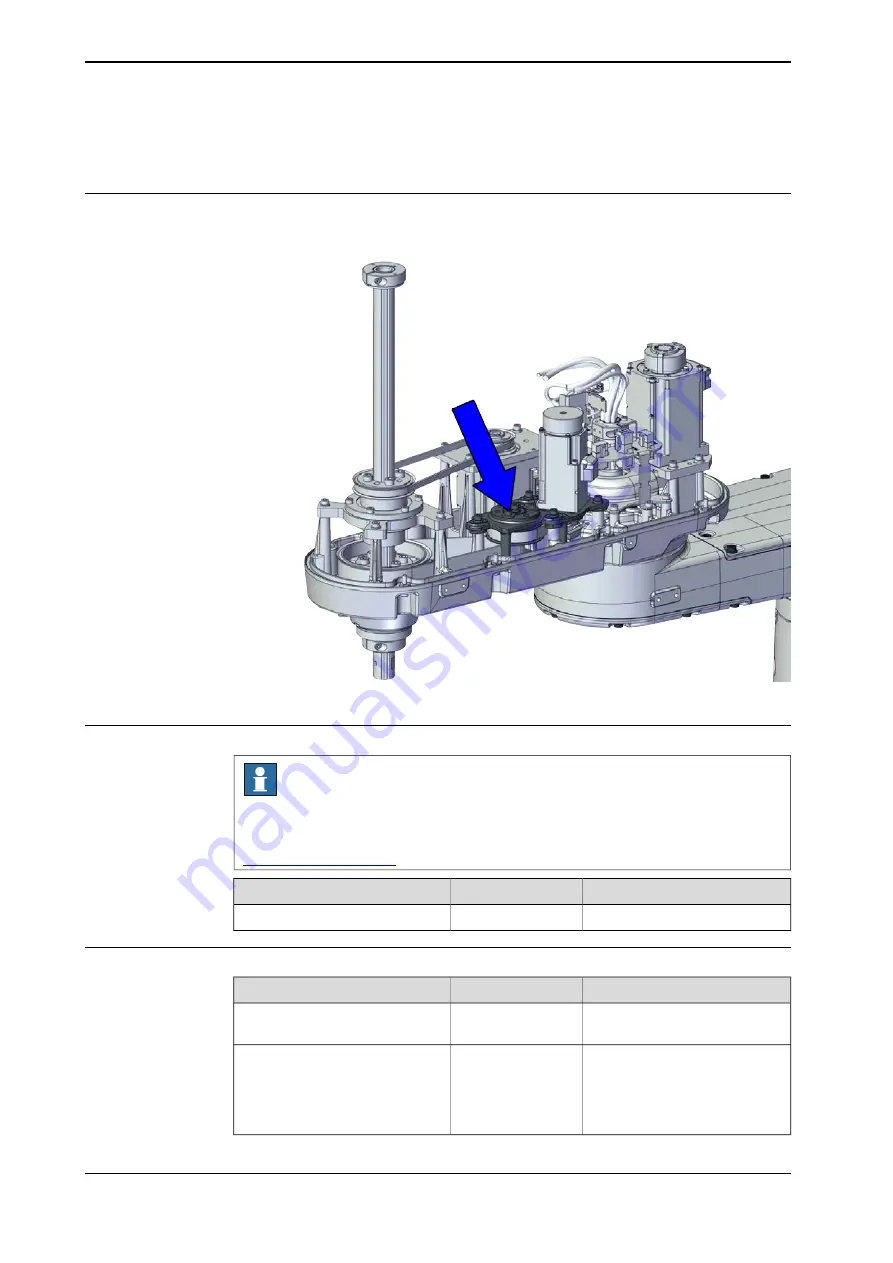
5.6.10 Replacing the transmission module
Location of the transmission module
The transmission module is located as shown in the figure.
xx2100001018
Required spare parts
Note
The spare part numbers that are listed in the table can be out of date. See the
latest spare parts of the IRB 920 via myABB Business Portal,
.
Note
Article number
Spare part
3HAC076579-001
Transmission module
Required tools and equipment
Note
Article number
Equipment
Content is defined in section
.
-
Standard toolkit
Delivered as a set of calibration
tools.
Required if Axis Calibration is the
valid calibration method for the
robot.
3HAC055412-001
Calibration toolbox, Axis Calibra-
tion
Continues on next page
626
Product manual - IRB 920
3HAC075721-001 Revision: C
© Copyright 2022 ABB. All rights reserved.
5 Repair
5.6.10 Replacing the transmission module
Содержание IRB 920
Страница 1: ...ROBOTICS Product manual IRB 920 ...
Страница 2: ...Trace back information Workspace 22A version a22 Checked in 2022 03 21 Skribenta version 5 5 019 ...
Страница 8: ...This page is intentionally left blank ...
Страница 14: ...This page is intentionally left blank ...
Страница 50: ...This page is intentionally left blank ...
Страница 110: ...This page is intentionally left blank ...
Страница 984: ...This page is intentionally left blank ...
Страница 1000: ...This page is intentionally left blank ...
Страница 1002: ...This page is intentionally left blank ...
Страница 1006: ......
Страница 1007: ......