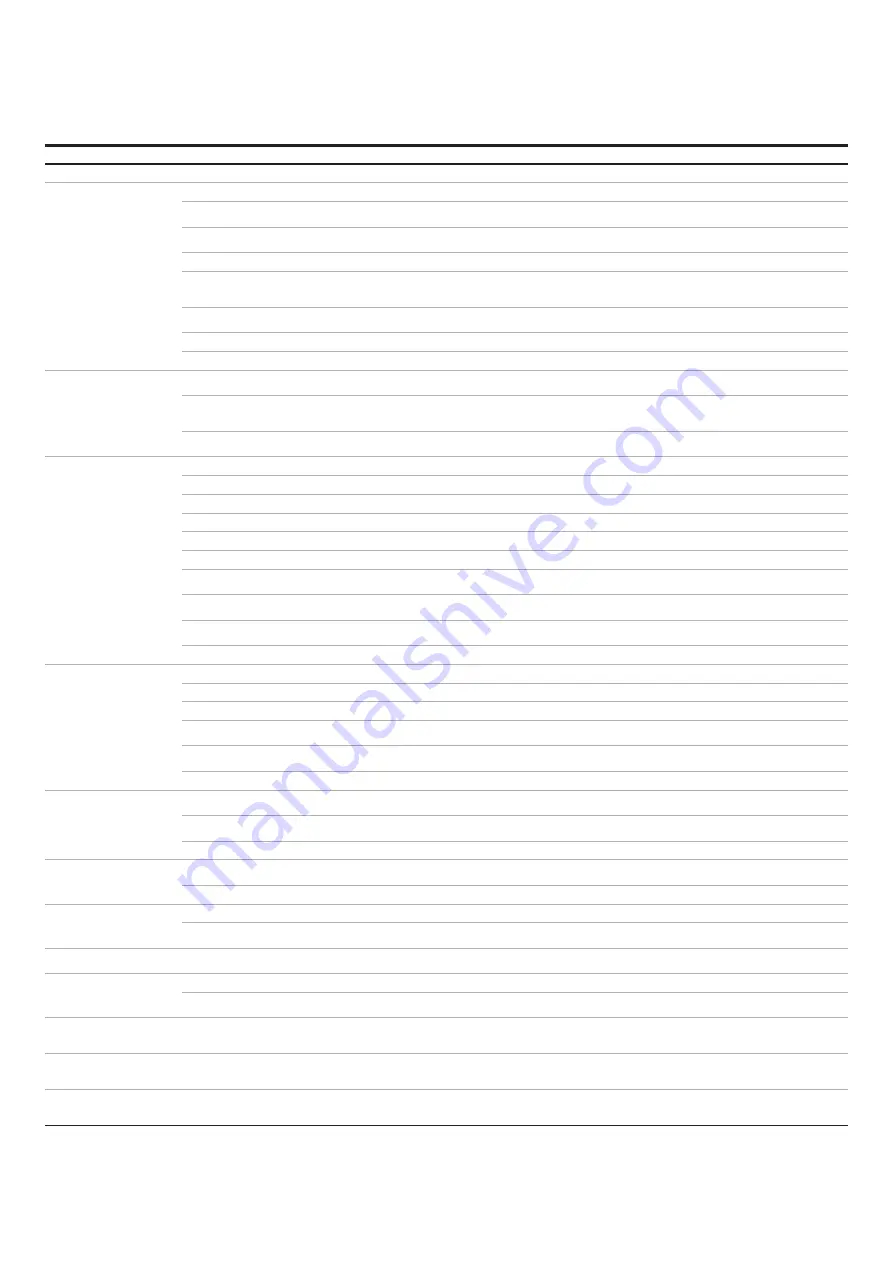
A B B I N T H E R A I LWAY S – M ED I U M VO LTAG E P R O D U C T S
31
A B B I N T H E R A I LWAY S – M ED I U M VO LTAG E P R O D U C T S
31
1V
S
R
6
3
0
2
0
6
E
N – e
n – E
D
O
-D
0
0
0
2
8
5
2
– I
n
st
ru
ct
io
n m
an
u
al – 2
0
21
.1
0 D
es
ig
n a
n
d s
p
ec
if
ic
at
io
n a
re s
u
b
je
ct t
o c
h
an
g
e w
it
h
o
ut n
o
ti
ce
—
11. Troubleshooting
Problem
Possible Causes
Possible Remedies
Ready
LED is Off
Auxiliary voltage supply has failed
Restore auxiliary voltage
(Unit
Not Ready
)
Actuator is not connected correctly or is defective
Check plug and continuity check of the coils
Position sensors are not connected correctly or are defective
Check connector and check operation with a metal ruler (change of LED
indicators)
Auxiliary voltage is interrupted and the capacitor charge has fallen below the
O-CO criterion
Restore auxiliary voltage
Push button panel is not connected correctly or is defective
Check connector or exchange component
The number of maximum permitted “unsuccessful” switching operations is
reached. As a result the apparatus is blocked.
Disconnect auxiliary voltage, COMPLETELY discharge capacitors so that
the function performs a counter reset.
General check of the apparatus
Actuator coil is defective
Disconnect auxiliary voltage, COMPLETELY discharge capacitors. Then
check actuator coils
Apparatus position in discordance
Movement is obstructed by object. Try to open by hand crank
Active signals from Remote system
Check the remote control unit
Ready
LED flashing
Apparatus is in the ON position and the closing coil of the actuator is
defective or not connected correctly
Only OFF cycle is possible. Open apparatus (Ready LED goes out) and
check defective actuator coil.
Auxiliary voltage supply has failed
In the ON position, the apparatus can still be switched OFF.
In the OFF position, a CO switching sequence can be executed.
Restore auxiliary voltage
During startup of the apparatus or after switching sequences during the
capacitor charging operation
Normal behaviour, wait for several seconds (charging time 1 to 3 min.)
A close operation
is not executed
Actuator closing coil is defective
Check actuator closing coil
ON Signal present
Check status of all input signals
Input Y6 is open
Close contact
Capacitors are not connected
Check the connection plug and capacitor cable
Ready
LED on the push button panel is off
See points “
Ready
LED
flashing
”
Push button panel is not connected correctly or is defective
Check plug or exchange component
Only for Version APPL.0: No switching possible from the push button panel
Check the Dip Switch I1004-5 configuration and the position of the
LOCAL/REMOTE selector switch (if fitted)
Only for Version APPL.0: No operation possible by the remote control
Check the Dip Switch I1004-5 configuration and the position of the
LOCAL/REMOTE or GLOBAL selector switch (if fitted)
Energy in the capacitors is too low for a CO operation
Restore auxiliary voltage.
See points “
Ready
LED
flashing
”
No remote control is possible
Check all external connections
An O operation is
not executed
Actuator opening coil is defective
Check actuator opening coil
Capacitors are not connected
Check the connection plug and capacitor cable
Remote signals for opening are not given
Check the connections of the signal cable
Setting of Jumper JP1001 with function and input BI Y4 are not correct
Check the correct Jumper setting. With a PR5xy device, JP1001 must be
in position 1+2.
Undervoltage monitoring is not activated
Correct setting of the undervoltage threshold and delay with dip switch
I1001 and I1004
Push button panel is not connected correctly or is defective
Check plug or exchange component
Apparatus closes and
opens automatically
Position sensor for ON position is not connected correctly or is defective
Check connector and check operation with a metal ruler (change of LED
indicators)
Apparatus does not go to the final ON position
Check whether foreign bodies obstruct movement.
Status check of the drive mechanism
Capacitors are defective
Check the voltage (80V) and change components if necessary
Apparatus opens if the
auxiliary voltage supply
is disconnected
Undervoltage monitoring is activated and the undervoltage signal input is
connected with the same power supply
Connect undervoltage signal input with a different power supply
Capacitor energy failure function is activated
If possible, deactivate function with dip-switch I1004
All output signals are open
The voltage of the capacitors is less than 46VDC
Restore auxiliary voltage
Same behaviour immediately after disconnecting the auxiliary voltage
supply. Ready LED goes out at the same time.
Check the connection plug and capacitor cables
Apparatus has been
switched off by signal at Y3
Signal input Y3 is configured as “Safe OFF” and CPU is defective
Contact ABB
The “Auto-Reclose”
function is not executed.
Apparatus only opens
Signal input Y6 “Lock in open“ is not active
Close signal input and repeat procedure
ON signal is not active (signal inputs or ON button of the push button panel)
To obtain a “re-close” after a normal ON switching action, the ON signal
must be cancelled and reactivated.
The “Auto-Reclose” function
is only executed once
Faulty ON signal sequence (signal inputs or ON button of the push button
panel)
After every “Reclose” function, the ON signal must be cancelled. For a
series of repeat functions, the ON signal must be cancelled and
reactivated
No correct startup of the
apparatus or unusual
Ready LED indicated
Check whether jumpers other than those described in the operating manual
are set
Remove those jumpers not described and perform restart after
complete discharge of the capacitors
No change in function
after jumper or dip-
switch changes
Auxiliary voltage supply was not disconnected or capacitors still have
voltage
Disconnect auxiliary voltage supply and discharge capacitors
completely. After a restart, the new setting is activated.