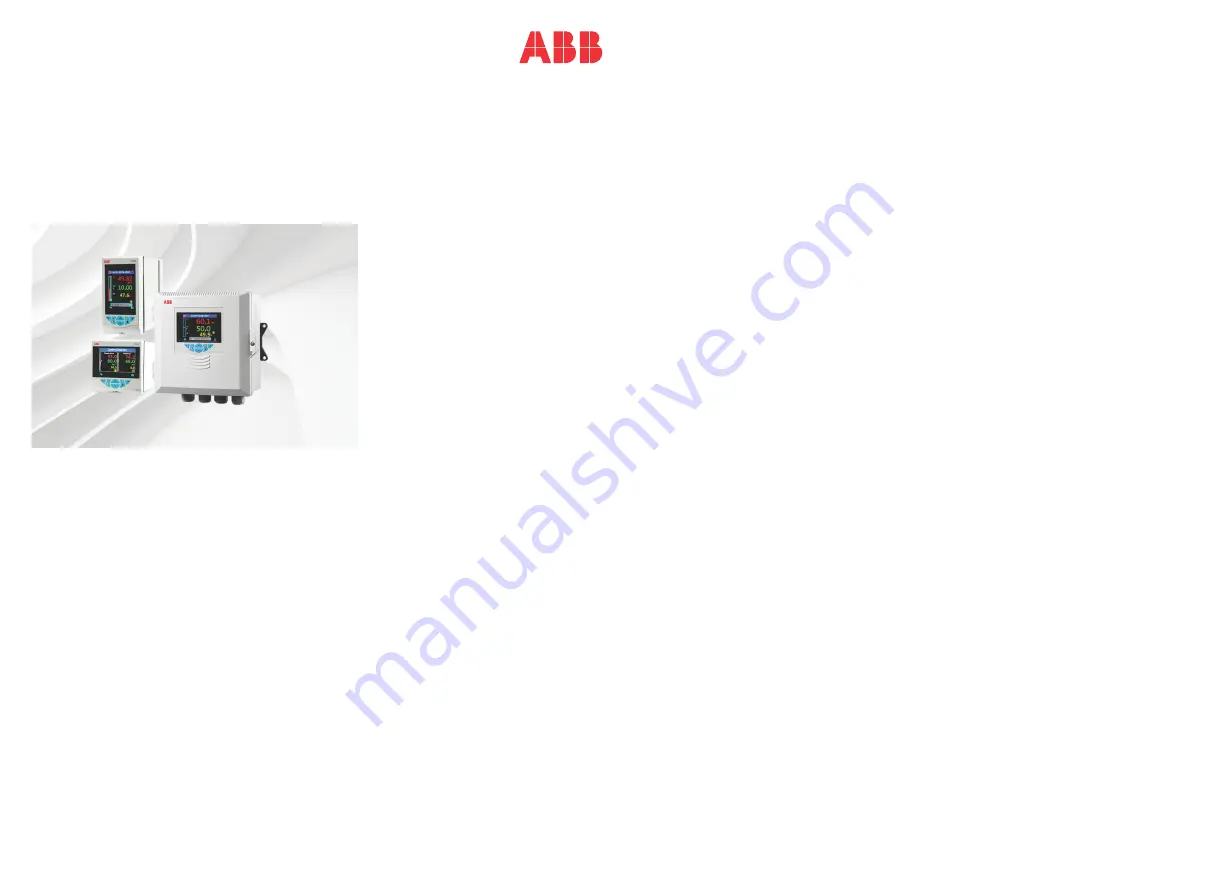
—
ABB ME A SUREMENT & ANALY TICS | USER GUIDE
ControlMaster CM30, CM50 and CMF310
Universal process controllers –
¼, ½ DIN and fieldmount
Measurement made easy
User Guide – Extended / Dual Functionality IM/CM/ED–EN Rev. X
ControlMaster CM30, CM50 and CMF310
Universal process controllers,
1
/
4
,
1
/
2
DIN and
fieldmount
The Company
We are an established world force in the design and manufacture of instrumentation for industrial
process control, flow measurement, gas and liquid analysis and environmental applications.
As a part of ABB, a world leader in process automation technology, we offer customers application
expertise, service and support worldwide.
We are committed to teamwork, high quality manufacturing, advanced technology and unrivalled
service and support.
The quality, accuracy and performance of the Company's products result from over 100 years
experience, combined with a continuous program of innovative design and development to
incorporate the latest technology.