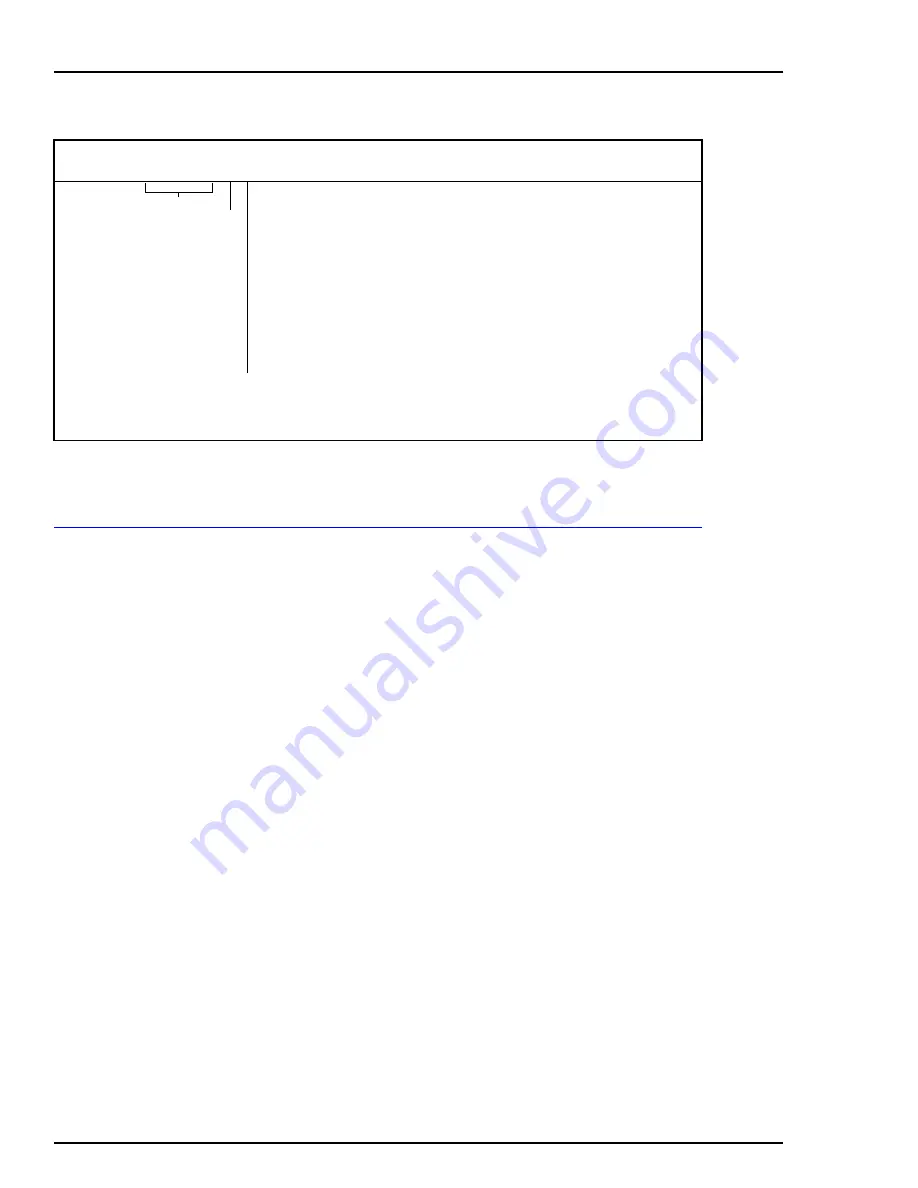
QUICK START
MOUNTING THE POSITIONER
B - 2
MOUNTING THE POSITIONER
Install the positioner as required on the actuator. Figures
and
show typical mounting arrangements. Use the following pro-
cedure for mounting guidelines.
NOTE:
If the actuator is equipped with a Type AV positioner as
ordered, verify that all the connections are secure and make any
adjustments as required.
1.
Set the actuator at the zero position. Connect the adjustable link-
age to the drive arm. The drive arm holes correspond to stroke length
of the actuator. Refer to Figure
for the stroke length for each drive
arm hole.
2.
Install the cam (black, direct acting; or red, reverse acting) that
will provide the required direction of rotation.
NOTE:
Cams have three mounting holes: A, square root; B, linear;
C, square. Each mounting hole is star shaped so the cam can be
rotated in 45
°
increments to suit the application.
3.
With the actuator in the closed position, adjust the connecting
linkage so that the zero radial line on the cam intersects the center of
the cam roller (Fig.
).
4.
Lock all linkage components in place.
Drive Shaft
0
Standard with feedback arm for linear motion
1
0.500-in. square end
2
0.342-in. square end for older DeZurik actuators
3
0.250 in. across flats (UP1 and UP2 after August, 1995)
4
0.375 in. square for DeZurik PowerRac
®
actuators
5
0.156 in. across flats for NAMUR rotary actuators
Other Options
0
Standard (no other options)
N
NEMA 4X enclosure rating (when installed per drawing C258567)
P
Performance Series — high pneumatic gain for large actuators
NOTES:
1. High temperature Type AV1 positioners are only available without manifolds or position transmitters; however, gage blocks are permitted.
2. Explosionproof Type AV2 positioners are not available with position transmitters or manifolds.
3. No longer available as of October 2003.
Table B-1. Nomenclature
(continued)
Position
1
2
3
4
5
6
7
8
9
Type A V
_
_
_
_
_
_
_
Characterizable Positioners
Previous Page
Содержание AV1
Страница 1: ...Characterizable Pneumatic Positioners Operating Instructions Actuators Positioners Models AV1 AV2 ...
Страница 24: ......
Страница 42: ......
Страница 51: ...CALIBRATION TROUBLESHOOTING CALIBRATION ADJUSTMENTS 4 9 Figure 4 7 I P Adjustment T00779A ...
Страница 52: ......
Страница 60: ......
Страница 70: ...REPAIR AND REPLACEMENT PILOT VALVE STROKE ADJUSTMENT 8 10 ...
Страница 88: ......
Страница 108: ......
Страница 116: ......
Страница 124: ...Index 4 Index continued Zero suppression 4 4 Zero suppression 4 4 Graph 4 4 ...
Страница 125: ......