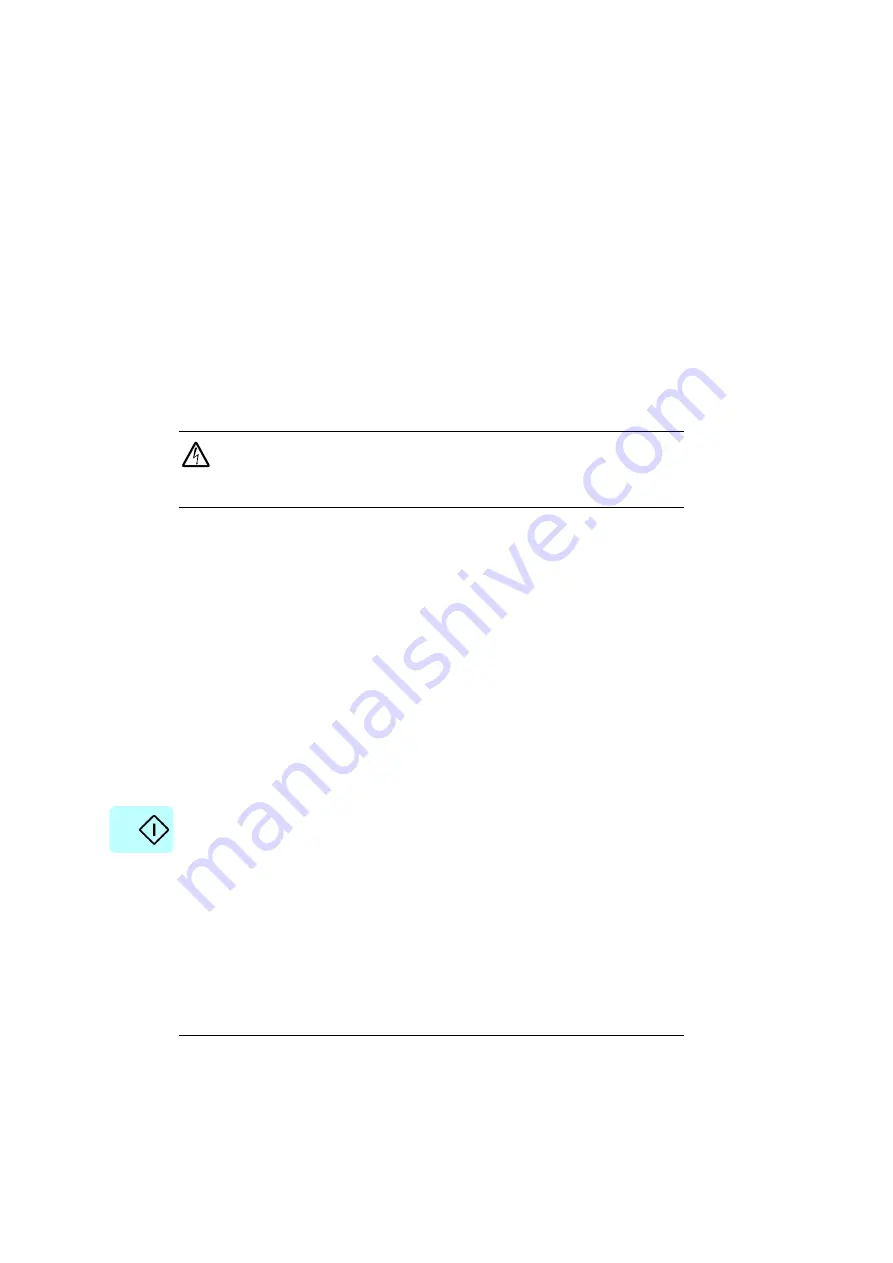
180 Resistor braking
Commissioning the braking circuit
For more information, see the
firmware manual
.
1. Enable the brake chopper function. Please note that a brake resistor must be
connected when the chopper is enabled from group
43 Brake chopper
.
2. Switch Off the overvoltage control of the drive with parameter
30.30 Overvoltage
control
.
3. Adjust any other relevant parameters in group
43 Brake chopper
.
WARNING!
If the drive is equipped with a brake chopper but the chopper is not
enabled by the parameter setting, the internal thermal protection of the drive
against resistor overheating is not in use. In this case, the brake resistor must be
disconnected.
Note
: Some brake resistors are coated with oil film for protection. At the start-up, the
coating burns off and produces a little bit of smoke. Ensure proper ventilation at the
start-up.
Содержание ACS880-M04
Страница 1: ...ABB machinery drives Hardware manual ACS880 M04 drive ...
Страница 4: ......
Страница 12: ...12 Table of contents ...
Страница 20: ...20 Safety instructions ...
Страница 28: ...28 About the manual ...
Страница 38: ...38 Operation principle and hardware description ...
Страница 48: ...48 Planning the cabinet installation ...
Страница 54: ...54 Mechanical installation ...
Страница 72: ...72 Planning the electrical installation ...
Страница 98: ...98 Electrical installation ...
Страница 102: ...102 Start up ...
Страница 108: ...108 Maintenance ...
Страница 140: ...140 Technical data ...
Страница 158: ...158 Mains chokes ...
Страница 164: ...164 EMC filters 7 Attach the terminal blocks to the filter 1 6 5 4 3 ...
Страница 166: ...166 EMC filters 6 Attach the terminal blocks to the filter 1 2 3 4 ...
Страница 168: ...168 EMC filters ...
Страница 182: ...Dimension drawings 182 Frame size R1 H1 H2 W D ...
Страница 183: ...Dimension drawings 183 Frame size R2 H2 H1 W D ...
Страница 184: ...Dimension drawings 184 Frame size R3 D W H1 H2 ...
Страница 185: ...Dimension drawings 185 Frame size R4 W H1 H2 D ...
Страница 187: ...187 Dimension drawings EMC filters type JFI x1 JFI A1 ...
Страница 188: ...Dimension drawings 188 JFI B1 ...
Страница 189: ...189 Dimension drawings EMC filters type JFI 0x ...
Страница 191: ...191 Dimension drawings Brake resistors type JBR xx ...
Страница 193: ...193 Dimension drawings ...
Страница 195: ...www abb com drives www abb com drivespartners 3AXD50000028613 Rev A EN 2016 04 11 Contact us ...