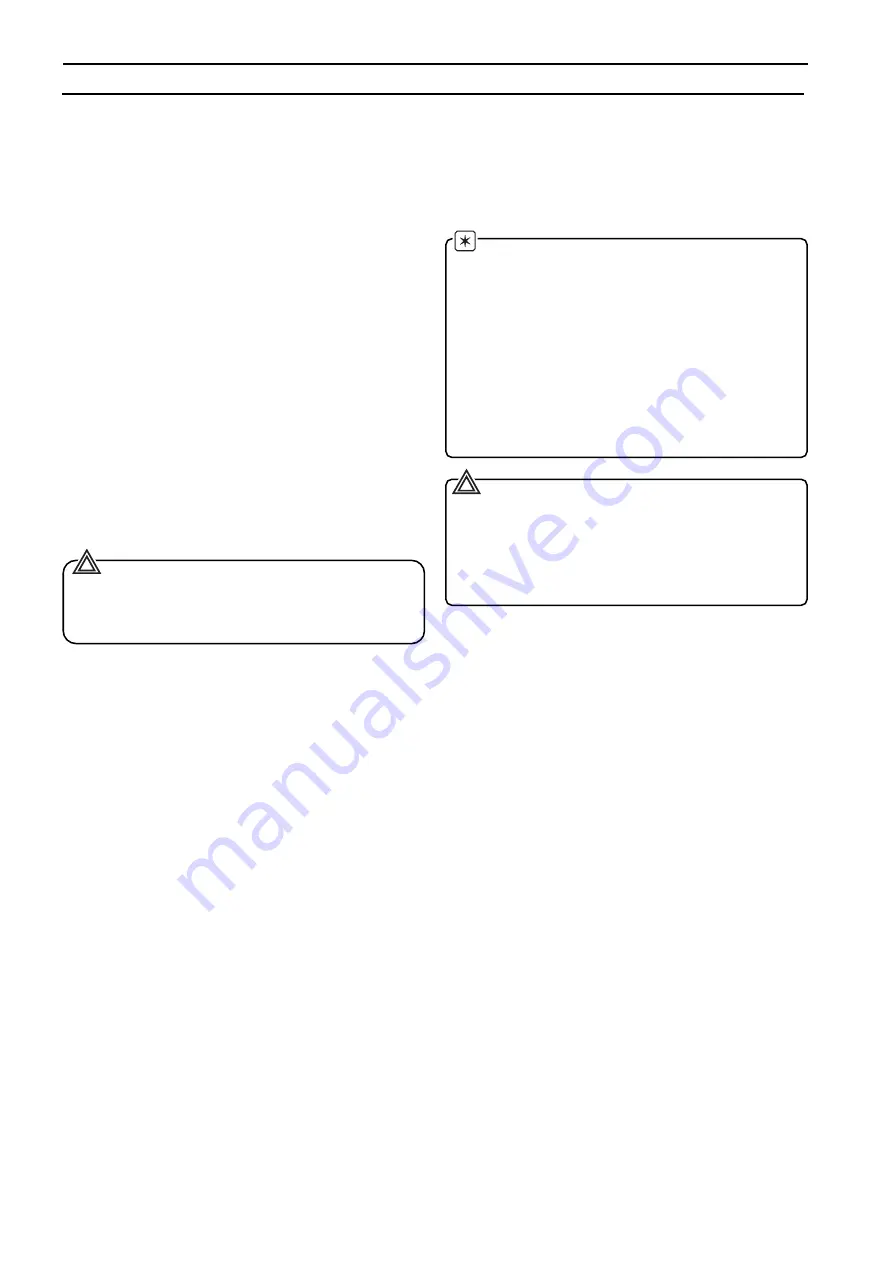
- 6 -
2.5
CORROSION
Be sure that the process fluid is compatible with the material of
the process flanges and sensor diaphragm.
A fluid / material compatibility table is available at www.abb.com
(inserting in the “search” tool the keyword “TB/COR”) or from
local ABB representatives.
NOTE
Data of the table are based on information from
manufacturers.
All data is based on a temperature of 20
°
C, 70
°
F unless
noted otherwise.
Since corrosion involves many more variables than this
table considers, such as trace contaminants, aeration or
temperature-concentration profile, stress corrosion cracking
and pitting, the table should be used only as a reference in
narrowing the choice of materials that merit further
investigation. Suitability of a particular material is best
determined by field test. At this purpose, please contact our
local ABB representatives.
WARNING
For safety purpose the design corrosion allowance of
differential pressure instrument flanges is of about 1.5 mm
0.04 in. Therefore from the viewpoint of safe containment
of liquids compatible with a specific material according to
the table, the expected instrument lifetime is more than 10
years, but the previous note apply.
2.6
SPECIAL SERVICES
In case of Oxygen or Hydrogen or other special services, the
transmitter has to be handled with a special care in order to
prevent contamination with impure substances. It is
recommended to use “sterile” gloves and that the removal of
protection bags be done only immediately before the installation.
Do not flush with impure fluids.
PHASE 1 - PRELIMINARY CHECKS
2.4
ENVIRONMENTAL LIMITS
2.4.1
Electromagnetic compatibility (EMC)
Complies with EN 50081–1 for emission and EN 50082–2 for
immunity requirements and test;
Radiated electromagnetic immunity level: 30V/m (according to
IEC 1000-4-3, EN61000-4-3).
Conducted electromagnetic immunity level : 30V (according to
IEC 1000-4-6, EN 61000-4-6).
Surge immunity level (with surge protector): 4kV (according to
IEC 1000-4-5 EN 61000-4-5).
Fast transient (Burst) immunity level: 4kV (according to IEC
1000-4-4 EN 61000-4-4).
2.4.2
Humidity
Relative humidity: up to 100% annual average
Condensing, icing: admissible
2.4.3
Vibration resistance
Accelerations up to 2g at frequencies up to 1000Hz
(according to IEC 60068-2-26)
2.4.4
Shock resistance
Acceleration: 50g
Duration: 11ms (according to IEC 60068-2-27)
WARNING !
Transmitters located in hazardous areas must be installed
in such a way to prevent the ignition of explosive atmosphere
because of impact and friction, even in case of rare events.
2.4.5
Wet and dust-laden atmospheres
The transmitter is dust and sand tight and protected against
immersion effects as defined by IEC EN 60529 (1989) to IP 67
(that can be considered equivalent to NEMA 4X and JIS
C0920).
2.4.6
Fill fluid warning
Be sure that the fill fluid (indicated on label Ref. B) can mix
safely with the process fluid in case of rupture of the sensor
membrane.