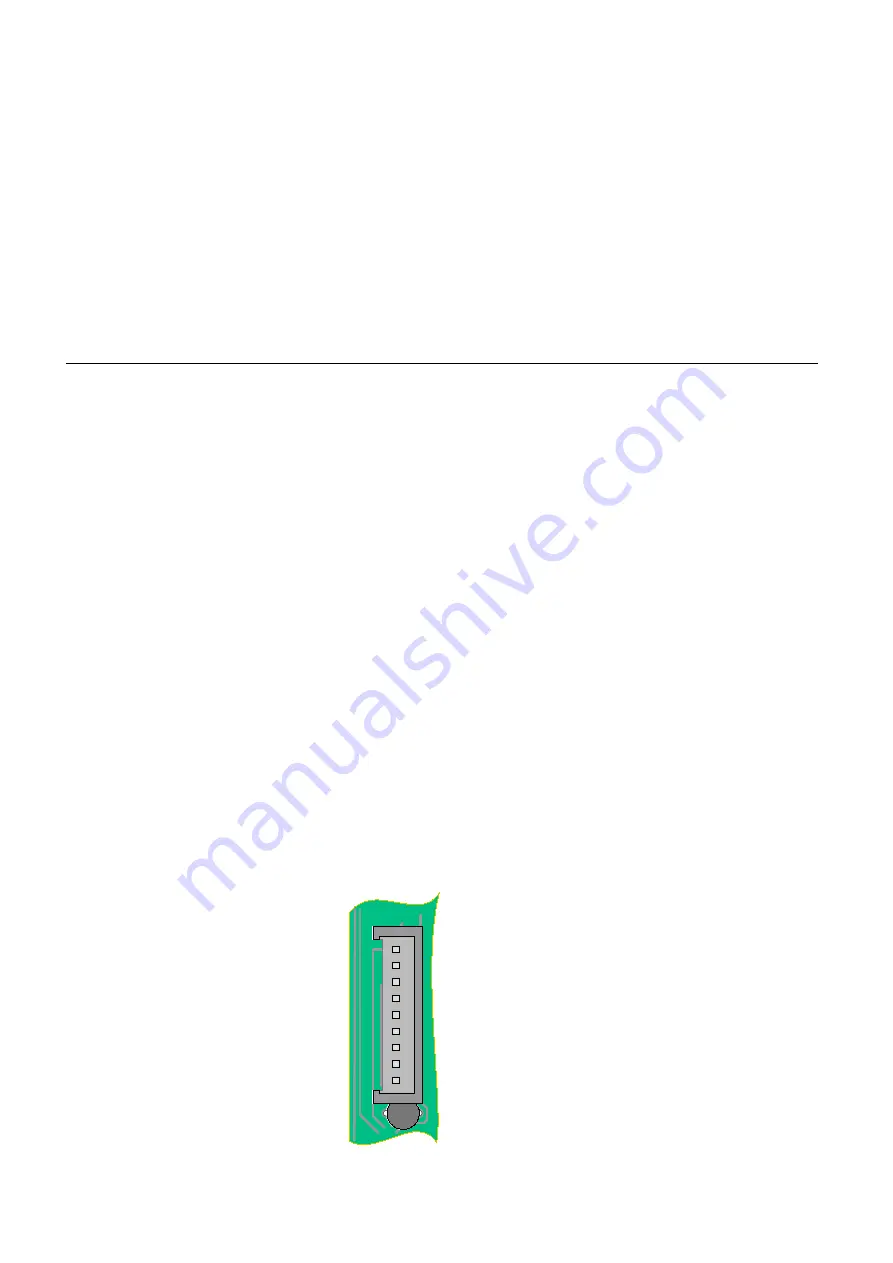
Page 11
Pro-120 controller instructions
12 ¶ Expansion connector
This 9 way connector may be fitted as an option.
Additional features (such as tachogenerator closed
loop control and IR compensation) can be added
here. It is also for ganging two Pro-120 controllers
together, to drive two motors simultaneously, when
the combination can control up to 240 amps of motor
current, making the combination quite suitable for
even high performance ride-on golf buggies. For
quantity orders 4QD can supply a slave version -
contact the factory for more information.
Double heading
When two standard controllers are used, one is the
master the second is the slave. This combination
might be used, for example, in an electric railway for
‘double heading’ a train with one engine at each end.
The controller which is to be the slave should have
its ignition switched off, it will be controlled by the
master.
The slave controller need have only battery
connections and connections to the second motor. It
is connected to the master Pro by a 4 way cable
between the two expansion connectors.
This cable should join as follows:
Pin numbers are printed on the circuit board.
The two controllers will work as one, controlling the
two motors together with the gain and ramp
adjustments of the master controlling both.
HPLO should however be disabled - either on both,
or just on the slave, or it will engage causing one
controller not to work (power relay will click on and
off).
Slaving is automatic: with the wire linked as shown
one will be slave (whichever you chose to drive
from!) and with the link disconnected, they will be
independent.
The two motors will perform identically but with
independent current limits. If two motors are used
off one single 200 amp controller, then the full 200
amps current is available to drive either motor in
stall conditions. With the Pro-120, each motor may
only draw up to 120 amps, limited by its own
controller. The system therefore offers more
protection to the motors. Also, if one motor gets
disconnected, the second motor will still be
protected. Lastly, if there is a failure in one
controller the chances are that the vehicle may still
be operable on the other controller, providing an
emergency ‘get you home’ service, albeit at reduced
performance.
Other Uses
The expansion connector is designed to allow
additional facilities to be fitted - so there are many
possibilities!
point, the parking brake is released.
MST. As the throttle is further advanced then,
normally just above the RAT, the controller starts to
modulate: i.e. it starts switching and voltage is fed to
the motor. This is the MST (Modulation Start
Threshold).
Because of stiction in the motors, they need a small
voltage before they start to rotate: this will occur at a
slightly higher throttle setting.
Full speed is reached approximately 3v above the
MST (measured on pin 6 of expansion connector).
In certain applications, altering these adjustments
can make for better low speed control, near zero
speed. For instance, increasing RAT could suppress
relay jitter in a radio control application.
Master Slave
Function
pin 1
pin 1
Ignition
pin 2
do not c9v
pin 3
do not connect Oscillator
pin 4
do not connect Oscillator
pin 5
pin 5
Speed
pin 6
do not connect Speed
pin 7
pin 7
Direction
pin 8
do not connect Current limit
pin 9
pin 9
0v
3
1 2 3 4 5 6 7 8 9
N