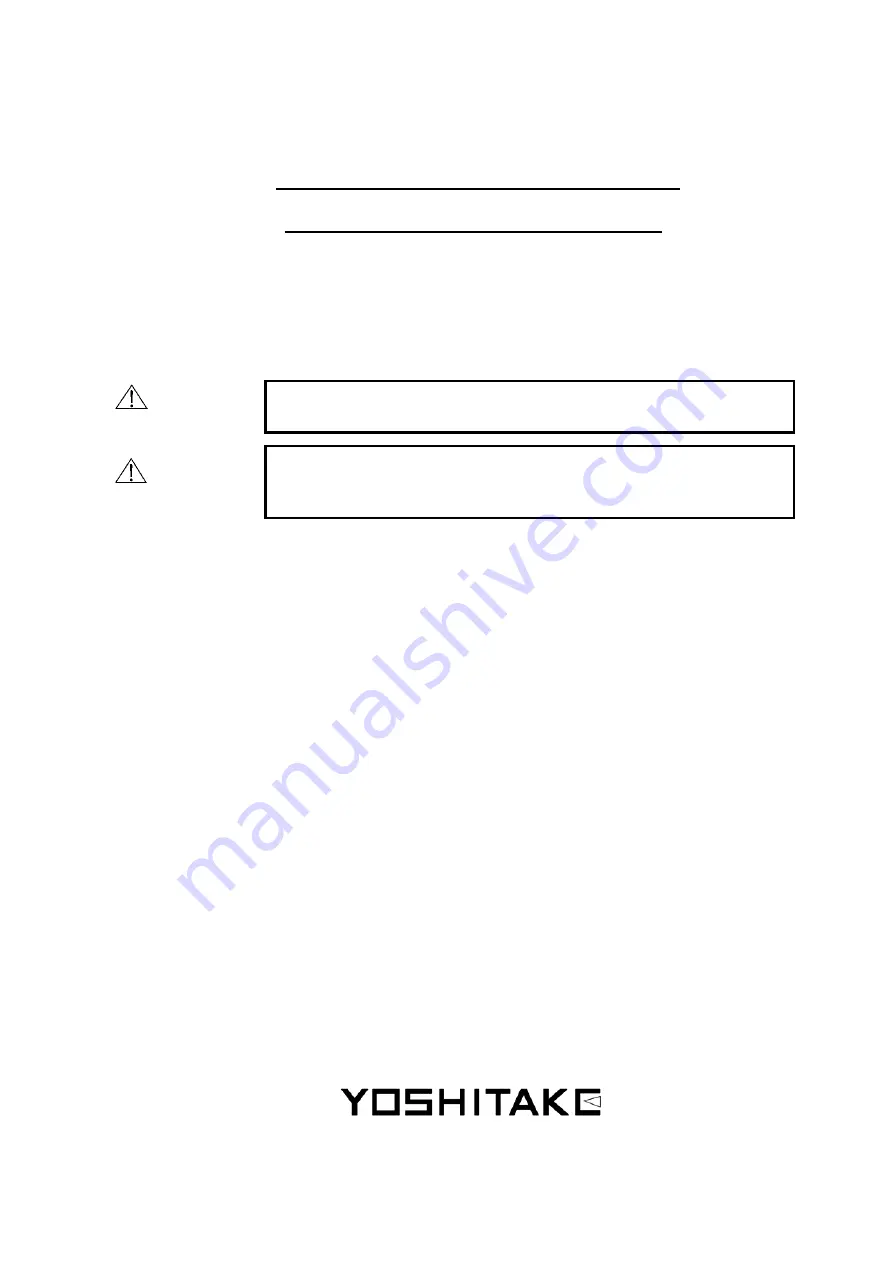
■
EPDT-098a
■
Model GPK-2001, GPK-2003
PRESSURE REDUCING VALVE
Installation & Operation Manual
Thank you very much for choosing the Yoshitake’s product. To ensure the correct and safe use
of the product, please read this manual before use. This manual shall be kept with care for
future references.
―――――――The following safety symbols are used in this manual. ――――――――
Warning
Caution
Contents
1. Specifications ···························································· 1~2
2. Dimensions and Weights ············································· 2~3
3. Operation ································································· 4~6
4. Nominal Size Selection Method
4.1 Specifications selection chart ····································· 7
4.2 Safety valve setting pressure chart ······························ 7
4.3 Characteristics chart ················································· 8
4.4 Nominal size selection chart ······································· 9
4.5 Nominal size selection calculation formula ···················· 10
5. Installation
5.1 Precautions for installation ········································ 11
5.2 Installing accessories··············································· 11
5.3 Piping before and after the pressure reducing valve ········ 12
5.4 Example of piping ··················································· 13
6. Operating Procedure
7.1 Precautions for operation ·········································· 14
7.2 Adjustment procedures ············································ 14
7. Maintenance Procedure
8.1 Troubleshooting ··················································· 15~16
8.2 Precautions for maintenance and inspection ················· 16
8.3 Disassembly ······················································· 16~17
8.4 Precautions during reassembly ·································· 17
8.5 Exploded drawing ················································ 18~19
Warranty Information
This symbol indicates a potentially hazardous situation that, if not
avoided, could result in death or serious injury.
This symbol indicates a hazardous situation that, if not avoided, may
result in minor or moderate injury. (“Caution” may also be used to
indicate other unsafe practices or risks of property damage.)
Summary of Contents for GPK-2001
Page 20: ...EPDT 098a 19...