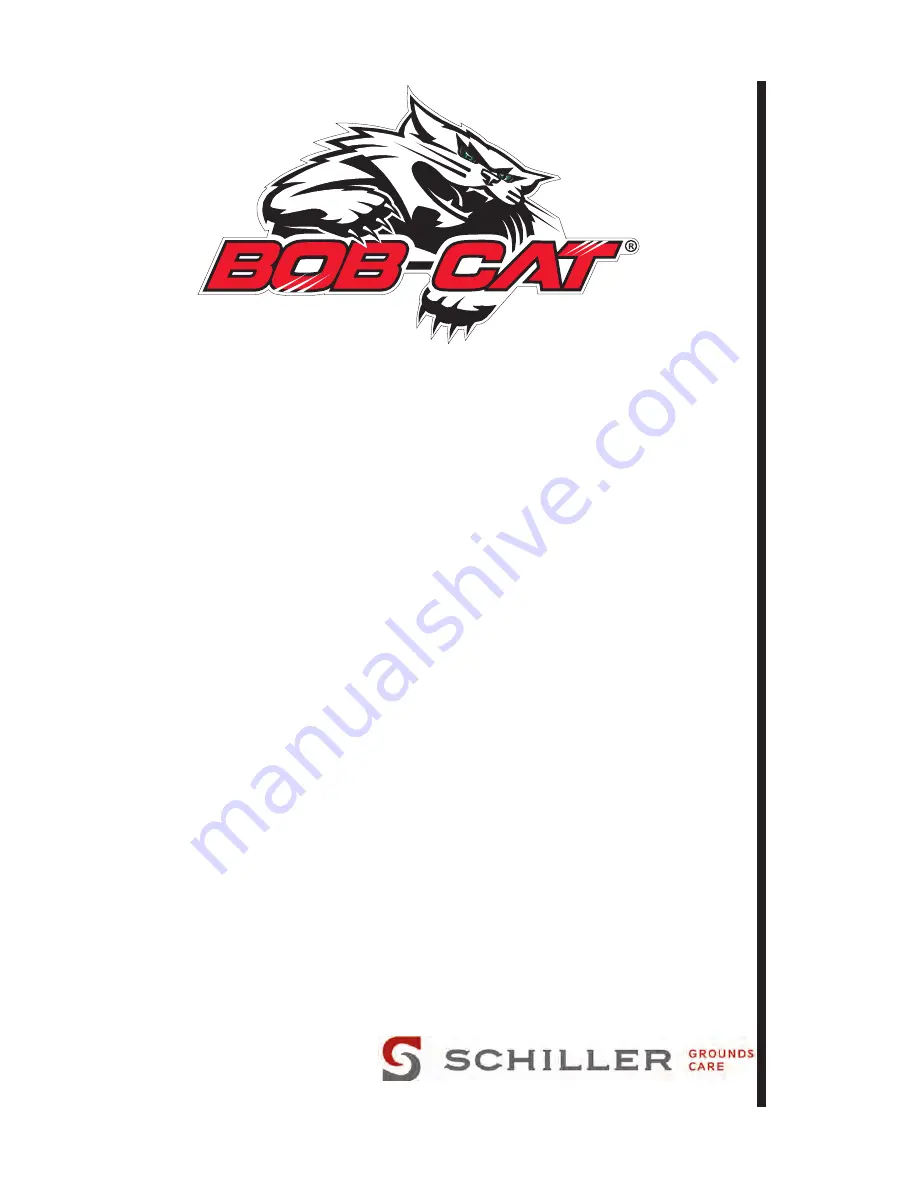
OPERA
T
OR’S MANUAL
MAN 4165707
Rev
.
A
1
1-2010
PARTS
MANUAL
4165706
www.bobcatturf.com
942512G
PREDATOR PRO 33HP GEN W/61” SIDE DISCHARGE
942513G
PREDATOR PRO 33HP GEN W/72” SIDE DISCHARGE
942514G
PREDATOR PRO 34HP KAW W/61” SIDE DISCHARGE
942515G
PREDATOR PRO 37HP KAW DFI W/61” SIDE DISCHARGE
942516G
PREDATOR PRO 37HP KAW DFI W/72” SIDE DISCHARGE