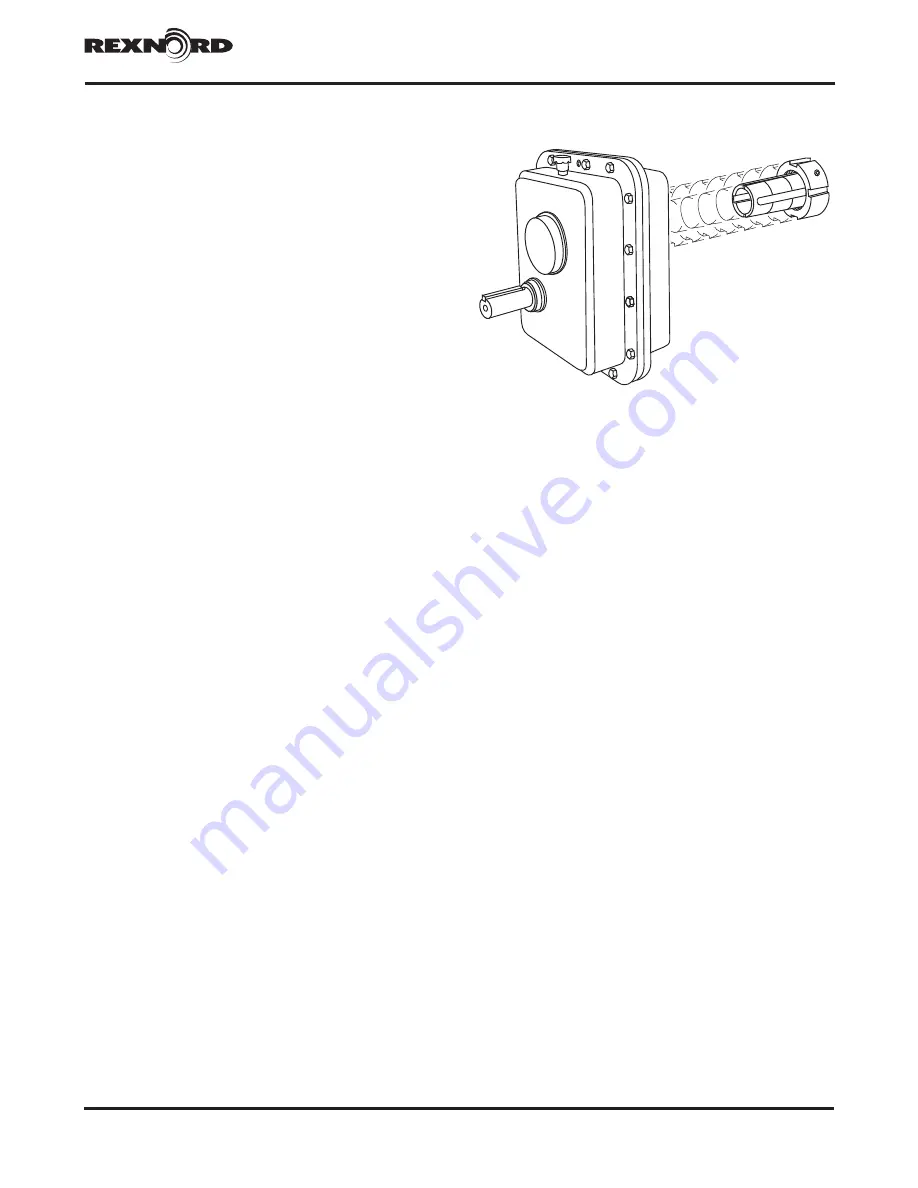
Falk
®
Quadrive
®
Shaft Mounted Drives Model A • Owners Manual
Sizes 5107-5315
(Page 1 of 52)
Rexnord (PN-2128394)
378-200
3001 W. Canal St., Milwaukee, WI 53208-4200 USA
January 2019
Telephone:
414-342-3131
Fax:
414-937-4359
www.rexnord.com
Supersedes 04-17
TABLE OF CONTENTS
Introduction 2
Drive Identification
3
SECTION I — DRIVE INSTALLATION
Outfitting 4
Installation 7
Lubrication 9
Start-up 9
SECTION II
— DRIVE SERVICE & REPAIR
Preventive Maintenance 10
Oil Changes 10
Stored & Inactive Drives 10
Repair & Replacement 10
Drive Disassembly 12
Identifying & Ordering Parts 14
Recommended Spare Parts 14
Parts List of Falk Part Numbers 16
Bearing Cross Reference Numbers 17
Seal Cross Reference Numbers 17
SECTION III — DRIVE REASSEMBLY
Drive Reassembly 18
APPENDICES
Appendix A: Lubrication Recommendations 23
Appendix B: Backstop Installation 32
Appendix C: TA Removal Tool 34
Appendix D: Motor Mount Installation 36
Appendix E: Vertical Standpipe Installation 38
Appendix F: Modifications for Non-Standard
Mounting Positions 40
Appendix G: Retaining Rings for Bushing Nuts and
Thrust Plates, Tooth Combinations for
Vibration Analysis & JSC Lip Seal
Accessory 42
Appendix H: Drive Shaft Recommendations for
Tapered Drive Shafts 43
Appendix J: Drive Shaft Recommendations Using
TA Taper Bushing 41
Appendix K: Drive Shaft Recommendations Using
(TCB) Kit 46
Appendix L: V-Belt Guard Installation 48
Appendix M: Electric Fan Installation 51
Appendix N: Reliability Package 52