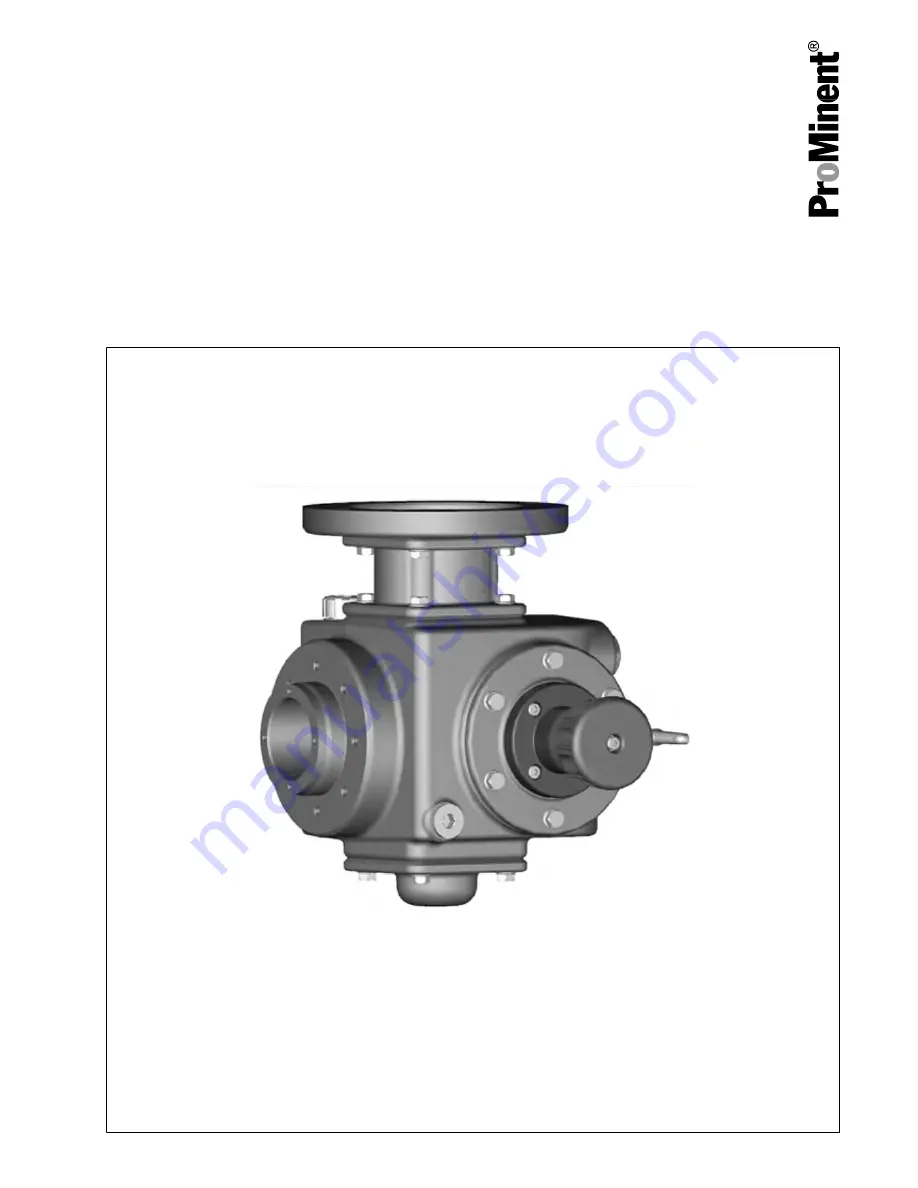
Drive unit
Orlita
®
Evolution
Operating instructions
These operating instructions form part of an operating manual and are only valid if used in conjunction with the documents
in this operating manual.
EN
983748
BA ORL 008 06/16 EN
Please carefully read these operating instructions before use. · Do not discard.
The operator shall be liable for any damage caused by installation or operating errors.
The latest version of the operating instructions are available on our homepage.