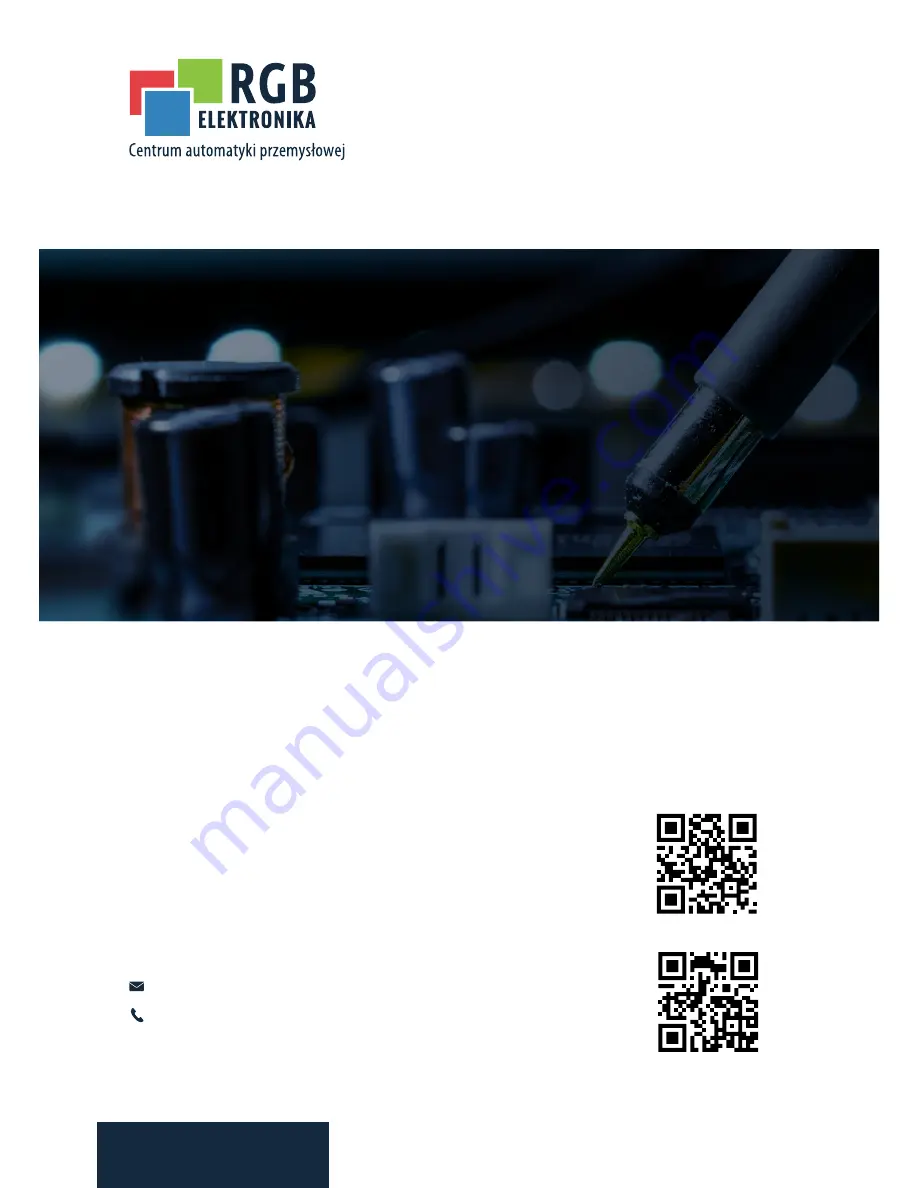
RGB ELEKTRONIKA AGACIAK CIACIEK
SPÓŁKA JAWNA
Jana Dlugosza 2-6 Street
51-162 Wrocław
Poland
[email protected]
+48 71 325 15 05
www.rgbautomatyka.pl
www.rgbelektronika.pl
DATASHEET
www.rgbautomatyka.pl
www.rgbelektronika.pl
OTHER SYMBOLS:
MR-J2S-200A
MRJ2S200A, MRJ2S 200A, MRJ2S-200A, MR J2S200A, MR J2S 200A, MR J2S-200A, MR-J2S200A, MR-J2S 200A,
MR-J2S-200A
MITSUBISHI ELECTRIC
Summary of Contents for MR-J2S-*A series
Page 37: ...1 18 1 FUNCTIONS AND CONFIGURATION MEMO ...
Page 139: ...5 34 5 PARAMETERS MEMO ...
Page 167: ...7 12 7 GENERAL GAIN ADJUSTMENT MEMO ...
Page 177: ...8 10 8 SPECIAL ADJUSTMENT FUNCTIONS MEMO ...
Page 179: ...9 2 9 INSPECTION MEMO ...
Page 199: ...11 8 11 OUTLINE DIMENSION DRAWINGS MEMO ...
Page 207: ...12 8 12 CHARACTERISTICS MEMO ...
Page 273: ...14 28 14 COMMUNICATION FUNCTIONS MEMO ...
Page 339: ...15 66 15 ABSOLUTE POSITION DETECTION SYSTEM MEMO ...