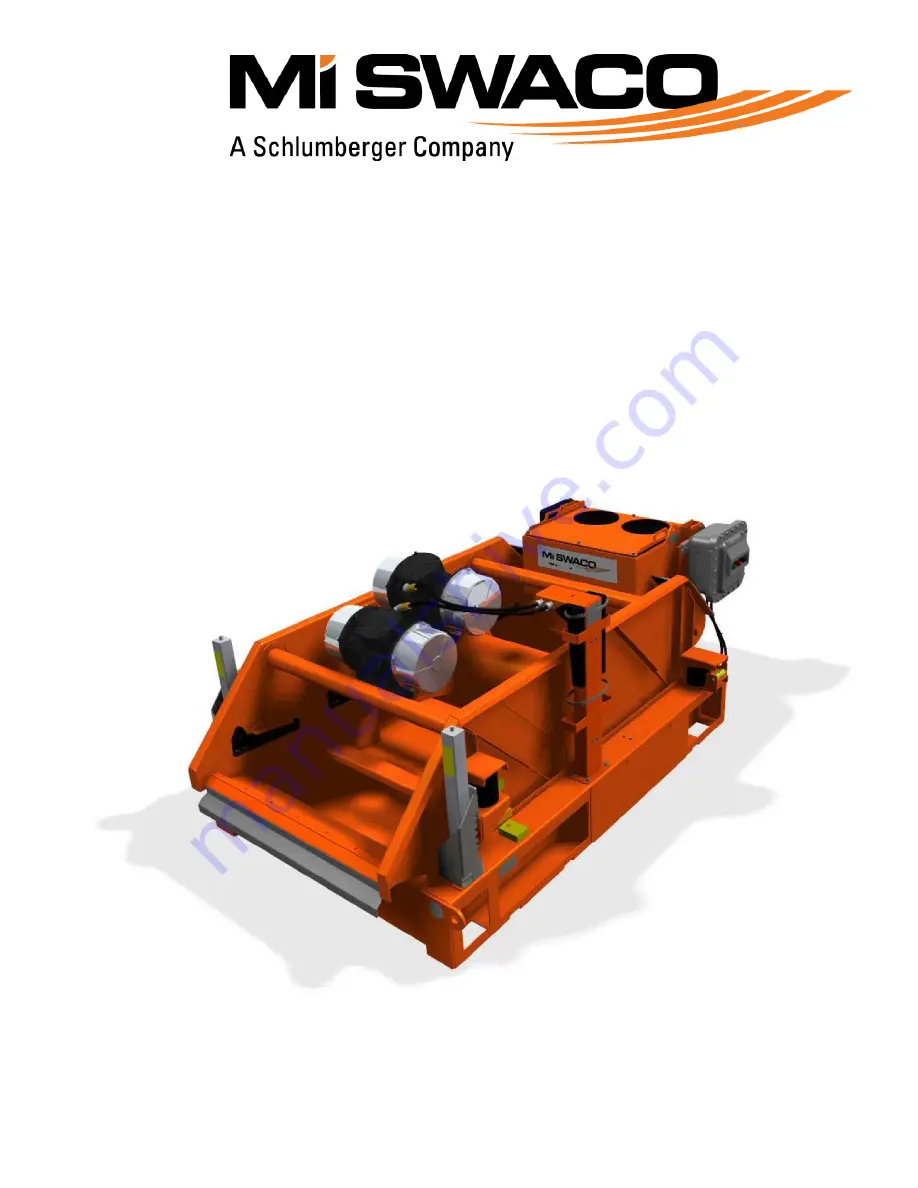
9092F02001AENG (D)
Publication Date: 6 JUL 2018
MONGOOSE PRO
Shale Shaker
Field Installation and Operation Manual
For Assemblies: 9675300-XXAD, 9675320-XXAD, 9675360-XXAD, 9675365-XXAD, 9675370-XXAD,
9675375-XXAD, 9675385-XXAD, 9675400-XXAD, 9675410-XXAD, 9675450-XXAD, 9675460-XXAD,
9675480-XXAD, 9675500-XXAD, 9675510-XXAD, 9675520-XXAD, 9675530-XXAD, 9675680-XXAD,
9675770-XXAD, 9675980-XXAD, 9675990-XXAD
For Configurations Certified to UL, ATEX, or IECEx Specifications