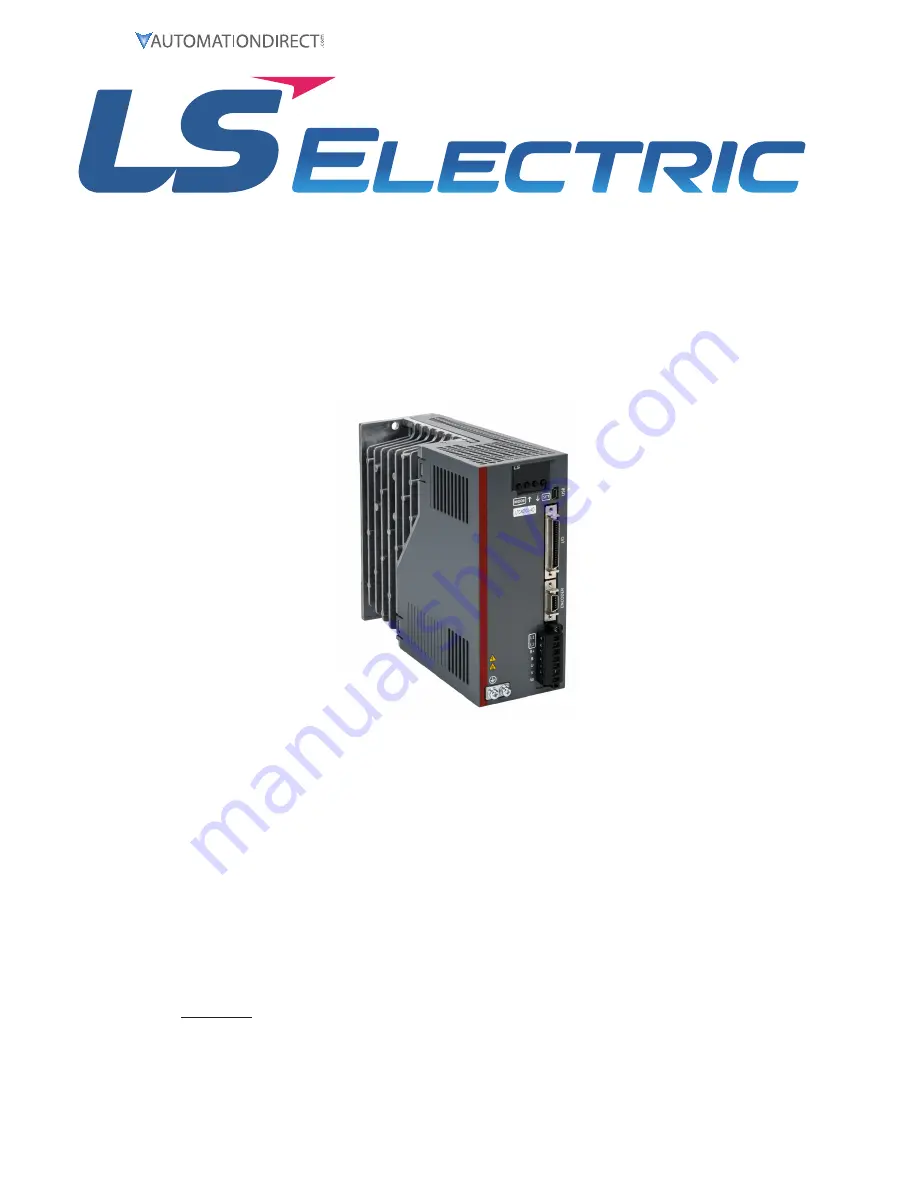
L7C Series AC Servo Drive
Quick Start Guide
1st Edition, Rev A, November 29th, 2021
AutomationDirect Foreword
This QuickStart Guide is designed to get an L7C servo system installed and running
quickly. This AutomationDirect Guide is a supplement to the LS Electric L7C User Manual.
This Guide does not replace the manufacturer’s User Manual. For advanced features
or options required by your application, you may still need to refer to the User Manual.
Download and reference both this QuickStart Guide and the L7C User Manual when
commissioning an L7C servo system.
A note on Part Numbers: LS Electric servo parts sold by AutomationDirect have part
numbers that end with a “-AD”. This suffix signifies special packaging and labeling for
AutomationDirect. All the LS servo products with the “-AD” function and behave exactly
the same as the standard LS Electric parts. Please note that when reading the LS electric
User Manual or using the Drive CM software, the “-AD” will NOT appear in any part
numbers.
Example:
AutomationDirect sells a 400W drive with part number L7CA004U-AD. All references to
the 400W drive in the LS Electric User Manual and Drive CM software will always show
L7CA004U.