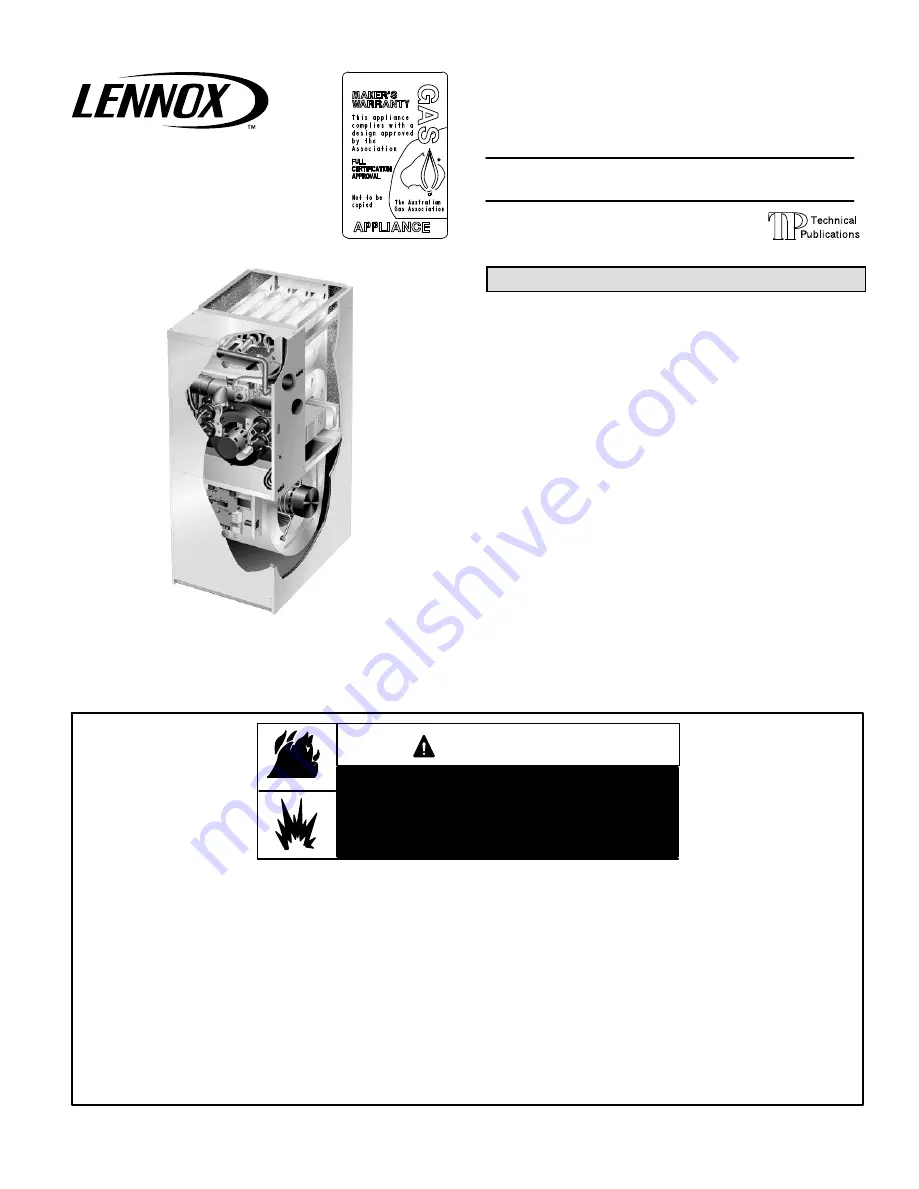
Page 1
06/09
*2P0609*
505,187M
*P505187M*
RETAIN THESE INSTRUCTIONS
FOR FUTURE REFERENCE
E
2006 Lennox Industries Inc.
Dallas, Texas, USA
INSTALLATION
INSTRUCTIONS
G61MPVT SERIES UNITS
GAS UNITS
505,187M
06/2009
Table of Contents
Unit Dimensions
2
. . . . . . . . . . . . . . . . . . . . . . . . . . . . . . .
G61MPVT Parts Arrangement
3
. . . . . . . . . . . . . . . . . . .
Shipping and Packing List
4
. . . . . . . . . . . . . . . . . . . . . . .
Safety Information
4
. . . . . . . . . . . . . . . . . . . . . . . . . . . . . .
Installation − Setting Equipment
5
. . . . . . . . . . . . . . . . . .
Filters
9
. . . . . . . . . . . . . . . . . . . . . . . . . . . . . . . . . . . . . . . . .
Duct System
9
. . . . . . . . . . . . . . . . . . . . . . . . . . . . . . . . . . .
Pipe & Fittings Specifications
10
. . . . . . . . . . . . . . . . . . .
Vent Piping Guidelines
11
. . . . . . . . . . . . . . . . . . . . . . . . .
Joint Cementing Procedure
12
. . . . . . . . . . . . . . . . . . . . .
Venting Practices
13
. . . . . . . . . . . . . . . . . . . . . . . . . . . . . .
Gas Piping
21
. . . . . . . . . . . . . . . . . . . . . . . . . . . . . . . . . . .
Electrical
23
. . . . . . . . . . . . . . . . . . . . . . . . . . . . . . . . . . . . .
Integrated Control Board
27
. . . . . . . . . . . . . . . . . . . . . . .
Unit Start−Up
34
. . . . . . . . . . . . . . . . . . . . . . . . . . . . . . . . . .
Gas Pressure Adjustment
35
. . . . . . . . . . . . . . . . . . . . . .
Manifold Pressure & High Altitude Information
35
. . . .
Other Unit Adjustments
36
. . . . . . . . . . . . . . . . . . . . . . . .
Heating Sequence of Operation
37
. . . . . . . . . . . . . . . . .
Service
38
. . . . . . . . . . . . . . . . . . . . . . . . . . . . . . . . . . . . . .
Requirements
40
. . . . . . . . . . . . . . . . . . . . . . . . . . . . . . . . .
General
40
. . . . . . . . . . . . . . . . . . . . . . . . . . . . . . . . . . . . . .
Combustion, Dilution & Ventilation Air
41
. . . . . . . . . . . .
Ignition Control Board Diagnostic Codes
44
. . . . . . . . .
Troubleshooting
45
. . . . . . . . . . . . . . . . . . . . . . . . . . . . . . .
Repair Parts List
51
. . . . . . . . . . . . . . . . . . . . . . . . . . . . . .
Vent Pipe Sizing Worksheet
51
. . . . . . . . . . . . . . . . . . . .
Start−Up & Performance Check List
52
. . . . . . . . . . . . . .
WHAT TO DO IF YOU SMELL GAS:
Do not store or use gasoline or other
flammable vapors and liquids in the
vicinity of this or any other ap-
pliance.
Installation and service must be
performed by a qualified installer,
service agency or the gas supplier.
D
Do not try to light any appliance.
D
Do not touch any electrical switch; do not
use any phone in your building.
D
Immediately call your gas supplier from a
neighbor’s phone. Follow the gas supplier’s
instructions.
D
If you cannot reach your gas supplier, call
the fire department.
FIRE OR EXPLOSION HAZARD.
Failure to follow safety warnings exact-
ly could result in serious injury, death,
or property damage.
WARNING
D
Leave the building immediately.
Litho U.S.A.