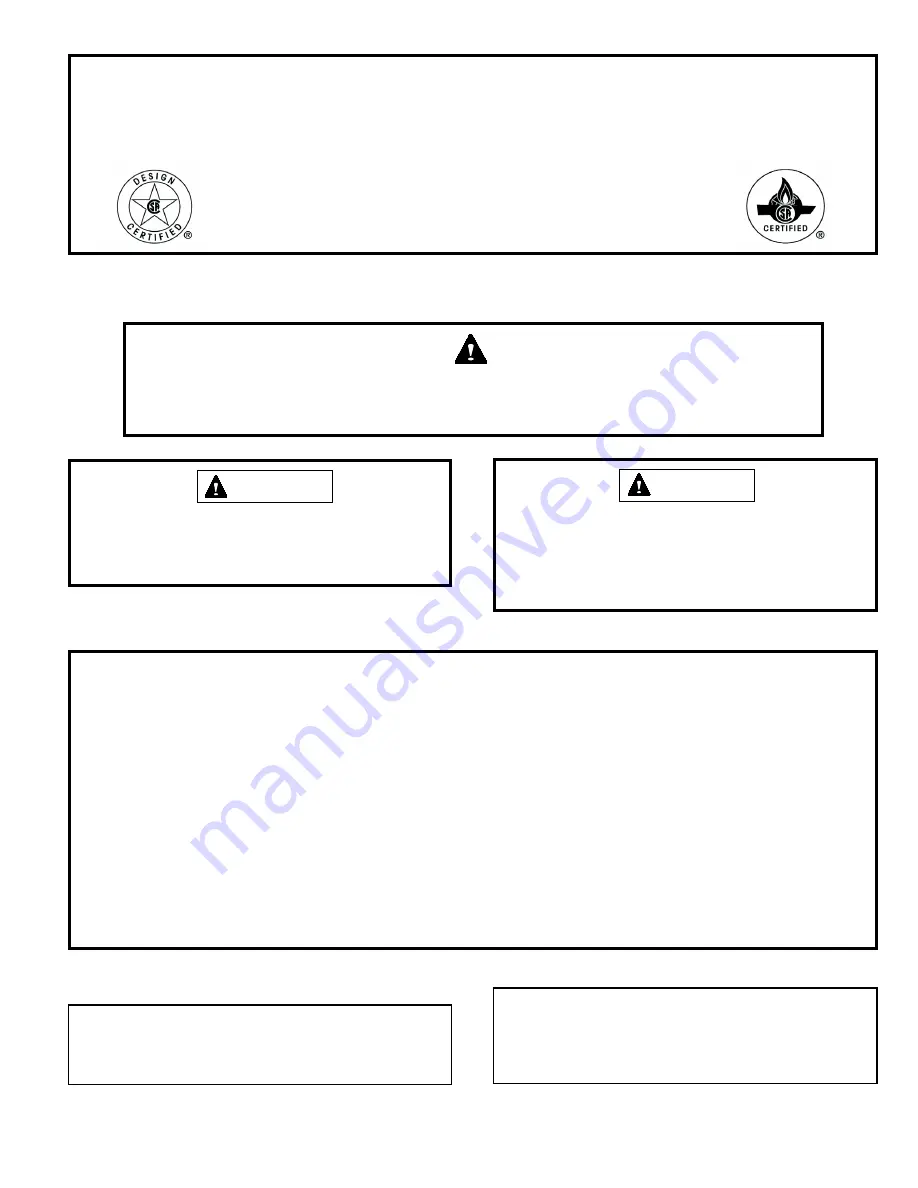
507271-02
Page 1 of 52
Issue 1621
This is a safety alert symbol and should never be ignored. When you see this symbol on labels or in
manuals, be alert to the potential for personal injury or death.
As with any mechanical equipment, personal injury can
result from contact with sharp sheet metal edges. Be
careful when you handle this equipment.
CAUTION
Manufactured By
Allied Air Enterprises LLC
A Lennox International, Inc. Company
215 Metropolitan Drive
West Columbia, SC 29170
Improper installation, adjustment, alteration, service
or maintenance can cause property damage, personal
injury or loss of life. Installation and service must
be performed by a licensed professional installer (or
equivalent), service agency or the gas supplier.
WARNING
(P) 507271-02
*P507271-02*
INSTALLATION INSTRUCTIONS
A95DF1D, A93DF1D, 95G1DF-P & 92G1DF-P
Warm Air Gas Furnace
Downflow Air Discharge
This manual must be left with the homeowner for future reference.
TABLE OF CONTENTS
Unit Dimensions ................................................................ 2
Parts Arrangement............................................................. 3
Gas Furnace ...................................................................... 4
Shipping and Packing List ................................................. 4
Safety Information ............................................................. 4
Use of Furnace as Construction Heater ............................ 5
General .............................................................................. 6
Combustion, Dilution & Ventilation Air ............................... 6
Setting Equipment ............................................................. 9
Filters ............................................................................... 12
Duct System .................................................................... 12
Pipe & Fittings Specifications
.......................................... 12
Joint Cementing Procedure ............................................. 14
Venting Practices ............................................................. 14
Vent Piping Guidelines .................................................... 16
Gas Piping ....................................................................... 32
Electrical .......................................................................... 34
Unit Start-Up .................................................................... 38
Gas Pressure Adjustment ................................................ 40
High Altitude Information ................................................. 40
Other Unit Adjustments.................................................... 43
Blower Motor Performance .............................................. 44
Service............................................................................. 46
Planned Service .............................................................. 48
Diagnostic Codes ............................................................ 48
Repair Parts List .............................................................. 49
Start-Up & Performance Check List ................................ 50
Summary of Contents for 92G1DF-P
Page 17: ...507271 02 Page 17 of 52 Issue 1621 A95DF 95G1DF and A93DF 92G1DF Table 7 ...
Page 18: ...507271 02 Page 18 of 52 Issue 1621 A95DF 95G1DF and A93DF 92G1DF Table 8 ...
Page 31: ...507271 02 Page 31 of 52 Issue 1621 Figure 49 Trap Drain Assembly Using 1 2 PVC or 3 4 PVC ...
Page 36: ...507271 02 Page 36 of 52 Issue 1621 Figure 56 Typical Wiring Diagram For A93DF 92G1DF ...
Page 37: ...507271 02 Page 37 of 52 Issue 1621 Typical Wiring Diagram Figure 57 For A95DF 95G1DF ...
Page 50: ...507271 02 Page 50 of 52 Issue 1621 Start Up Performance Check List ...