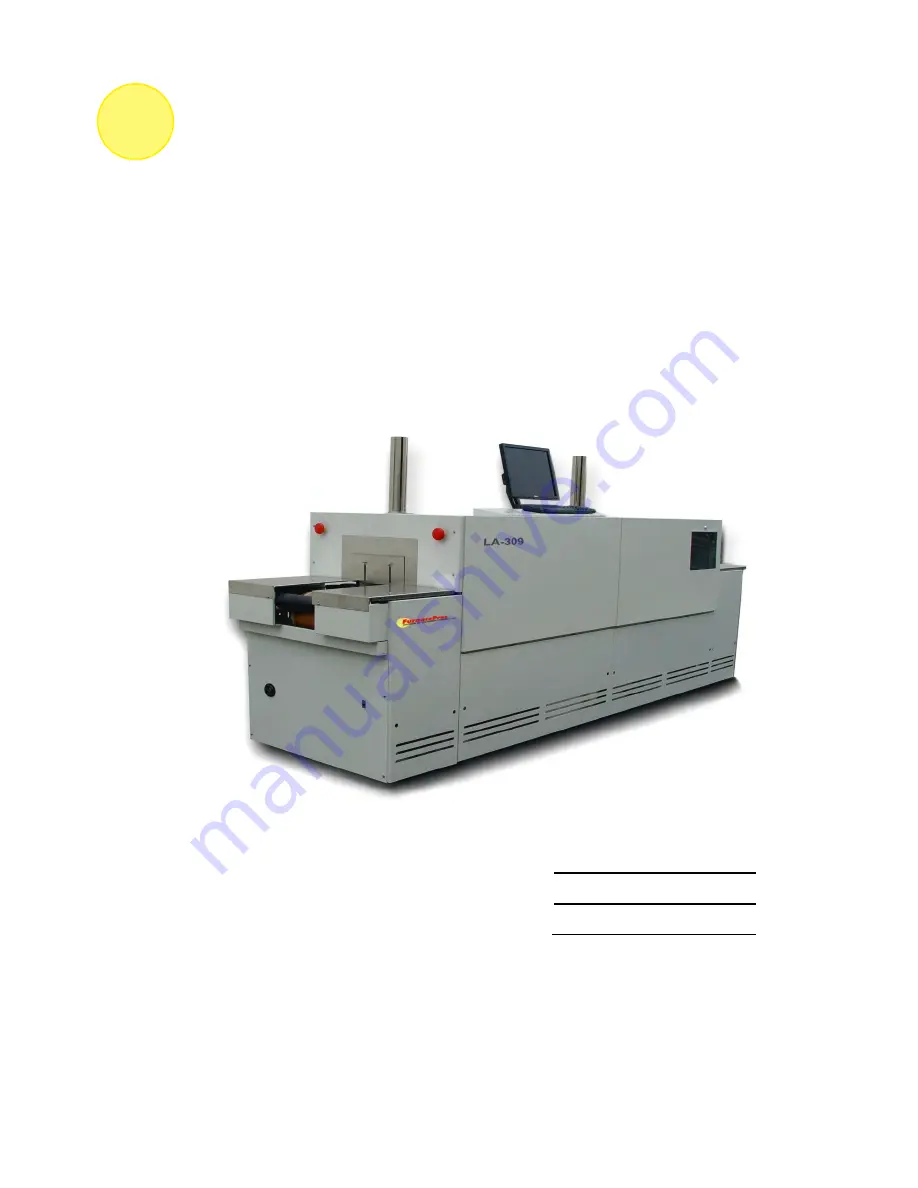
CONTINUOUS BELT IR FURNACE
Model LA-309
Owner’s Manual
Revision 3
MODEL:
LA-309
SERIAL NUMBER:
1303091001
FACTORY ORDER NUMBER:
10-004
LCI FurnacePros
30025 Alicia Pkwy, #417
Laguna Niguel, CA 92677 USA
+1 (949) 218-4996
Email: [email protected]
FurnacePros
DIVISION OF LOCHABER CORNWALL, INC.
Summary of Contents for LA-309
Page 5: ...10 004 676 110000 v WARRANTY Warranty goes here ...
Page 6: ...vi LA 309 Owner s Manual ...
Page 12: ...Contents xii LA 309 Owner s Manual ...
Page 20: ...Section 1 1 8 LA 309 Owner s Manual ...
Page 68: ...Section 3 3 28 LA 309 Owner s Manual ...
Page 70: ...Section 4 4 2 LA 309 Owner s Manual ...
Page 72: ...Section 4 4 4 LA 309 Owner s Manual ...
Page 98: ...Section 5 5 2 LA 309 Owner s Manual ...
Page 100: ...Section 5 5 4 LA 309 Owner s Manual ...
Page 106: ...Section 5 5 10 LA 309 Owner s Manual ...
Page 108: ...Section 5 5 12 LA 309 Owner s Manual ...
Page 110: ...Section 5 5 14 LA 309 Owner s Manual ...
Page 112: ...Section 6 6 2 LA 309 Owner s Manual ...
Page 114: ......
Page 115: ......
Page 126: ...Section 7 1 Fiberfrax Cements MSDS 042006 Owner s Manual ...
Page 139: ...MSDS 2 Fiberfrax Duraboard MSDS 042006 MATERIAL SAFETY DATA SHEETS ...
Page 140: ...Section 7 2 Fiberfrax Duraboard MSDS 042006 Owner s Manual ...
Page 153: ...MSDS 3 Fiberfrax Fibers MSDS 042006 MATERIAL SAFETY DATA SHEETS ...
Page 154: ...Section 7 3 Fiberfrax Fibers MSDS 042006 Owner s Manual ...
Page 167: ...MSDS 4 Fiberfrax Papers MSDS 042006 MATERIAL SAFETY DATA SHEETS ...
Page 168: ...Section 7 4 Fiberfrax Papers MSDS 042006 Owner s Manual ...
Page 181: ...MSDS 5 Magnaform MSDS 050406 MATERIAL SAFETY DATA SHEETS ...
Page 182: ...Section 7 5 Magnaform MSDS 050406 Owner s Manual ...
Page 183: ......
Page 184: ......
Page 185: ...Section 7 6 RTU Silicone Red Hi Temp 042006 Owner s Manual ...
Page 186: ...MSDS 6 RTU Silicone Red Hi Temp 042006 MATERIAL SAFETY DATA SHEETS ...
Page 189: ...Section 7 7 Kaowool Insulation MSDS 050406 Owner s Manual ...
Page 190: ...MSDS 7 Kaowool Insulation MSDS 050406 MATERIAL SAFETY DATA SHEETS ...
Page 201: ...Material Safety Data Sheets 7 15 Notes ...
Page 202: ...Section 7 7 16 Owner s Manual ...
Page 204: ...Section 8 Owner s Manual ...
Page 206: ...Section 8 Owner s Manual ...
Page 212: ...iv Operation and Troubleshooting ...
Page 214: ...vi Operation and Troubleshooting ...
Page 224: ...Page 10 Operation and Troubleshooting ...
Page 231: ...9 1 Section 9 APPENDIX B 9 1 EC913 CALIBRATION REPORT 9 2 SERIES EC900 OXYGEN ANALYZERS ...
Page 232: ...Section 8 Owner s Manual ...
Page 233: ......
Page 234: ...Section 8 Owner s Manual ...
Page 279: ...Section 8 Owner s Manual ...
Page 281: ...MSDS MATERIAL SAFETY DATA SHEETS ...
Page 282: ...16 Notes ...