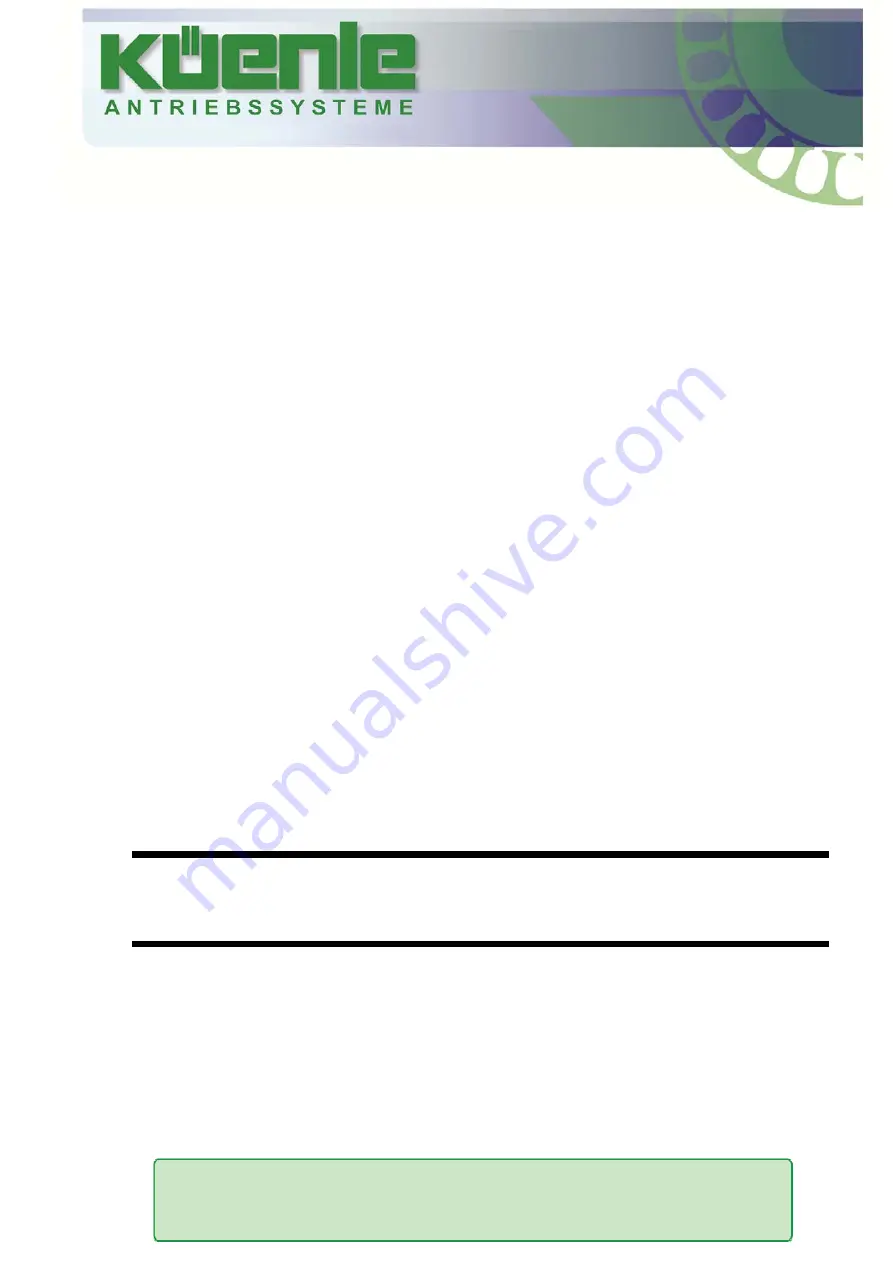
Küenle Antriebssysteme GmbH & Co. KG
Saarstraße 41-43 - 71282 Hemmingen - Telefon 07150 942-0
Fax 07150 942-270 - www.kueenle.de - [email protected]
Instruction Manual
Frequency Inverter
(incl. Control Unit MMI)
(incl. Extension Profibus)
Series KFU
tronic
400 V - 0,55 bis 22 kW
230 V - 0,55 bis 1,5 kW
KN 6400.2003