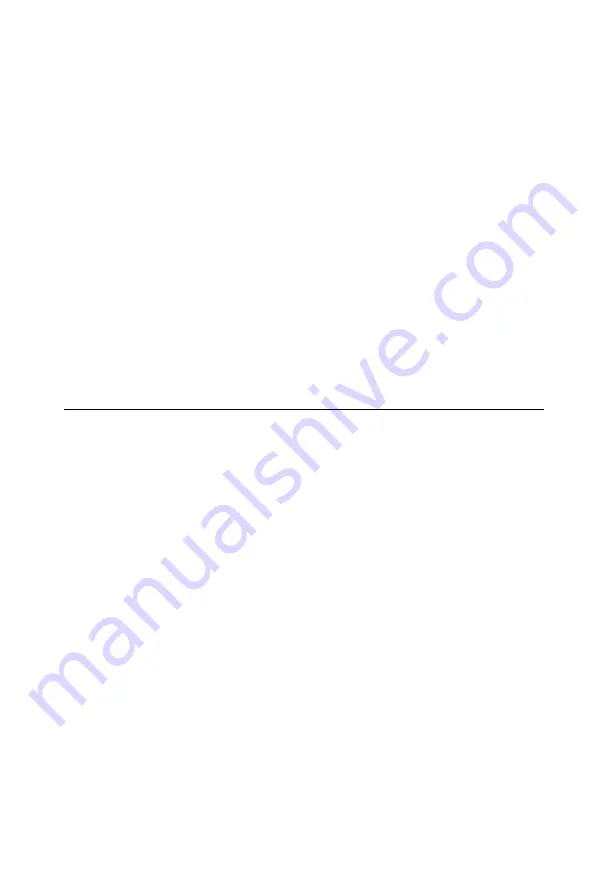
SVF-G7
SVF-G7
SVF-G7
SVF-G7 Series
Series
Series
Series High-performance
High-performance
High-performance
High-performance Vector
Vector
Vector
Vector
Control
Control
Control
Control
General-purpose
General-purpose
General-purpose
General-purpose
Frequency
Frequency
Frequency
Frequency
Inverter
Inverter
Inverter
Inverter
Operation
Operation
Operation
Operation Manual
Manual
Manual
Manual
Material Version
:
V6.0
Date of Filing
:
2012-08-10
Company Standard
::::
Q/0300SSC 001-2012
CHINSC ELECTRIC (CHINA) CO., LTD. could supply all-round
technology support for clients. The users could contact the nearby
agency or customer service center of CHINSC ELECTRIC
(CHINA) CO., LTD., and also could contact the manufacturer
directly.
All rights reserved. Any alteration is made without notice.
Head office: CHINSC ELECTRIC (CHINA) CO., LTD.
Customer hotline: 86-0533-6285662
Service hotline: 86-13375338006;
86-13375338007
URL: www.chinsc.com
E-mail: [email protected];