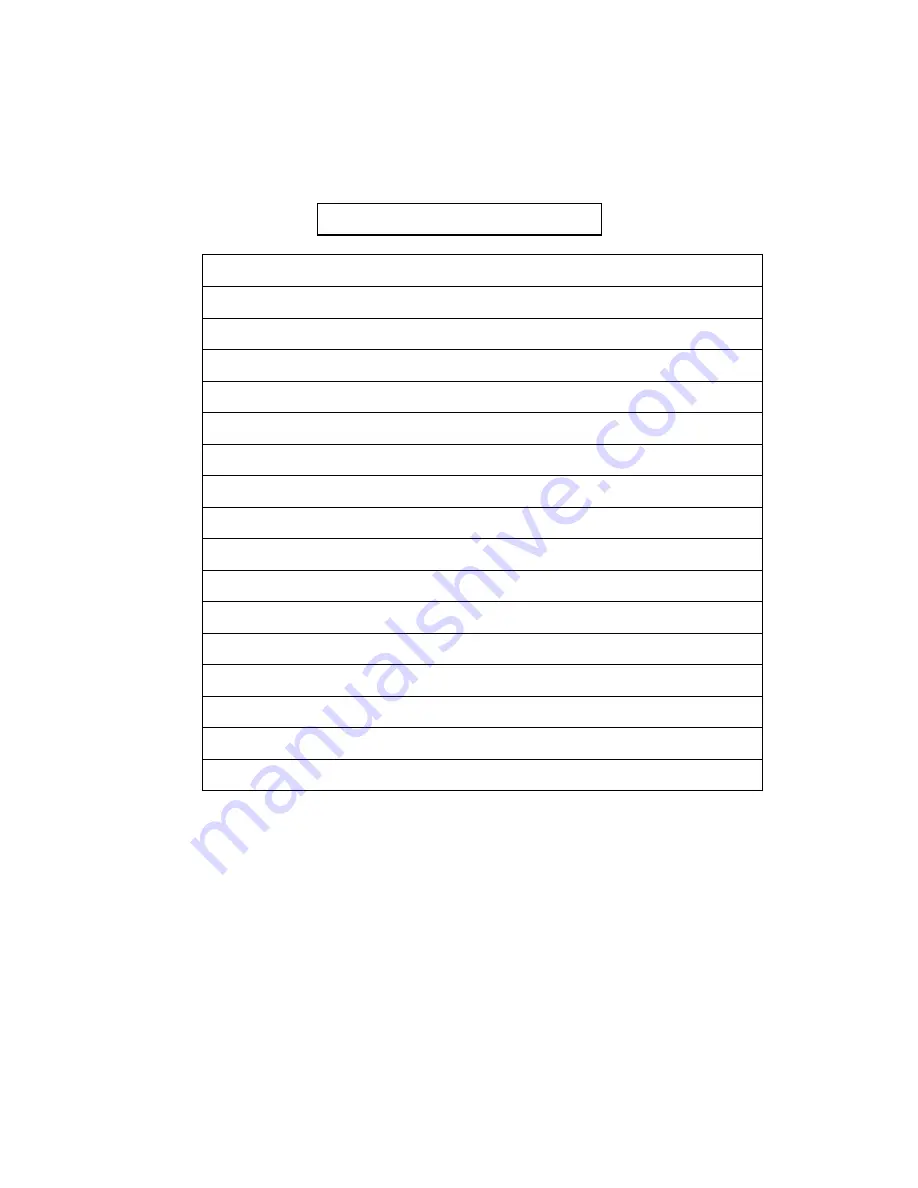
1
CONTENTS
GENERAL INFORMATION
1.Information
…
…
…
…
…………………………………..…….…
2
2
2
2
2.Maintenance………………………………………...…..6
3.EngineRemoval&Installation…
…
…
…
…
……………...…..13
ENGINE
4.LubricationSystem………...…………………………15
5.FuelSystem…………………………………………….19
6.CylinderHEAD&CylinderValve………...……….…..30
7.Cylinder&Piston……………………………………..46
8.V-Beltdrivingsystem…………………………………54
9.ACG&Startonewayclutch……………...…………..67
10.CoolingSystem……………...……………………..76
CHASSIS
11.SteeringSuspension…………..………................84
12.FrontWheel&BrakeSystem……………...……….90
13.RearWheel&BrakeSystem…………………….….95
14.ElectricalSystem…………………………………..97
15.TroubleShooting…………………………………..107
Summary of Contents for ATV300
Page 79: ...79 10 4 Trouble Diagnosis for Cooling System...
Page 80: ...80...
Page 103: ...103...
Page 108: ...108 15 2 POOR PERFORMANCE AT LOW AND IDLE SPEEDS 15 3 POOR PERFORMANCE AT HIGH SPEED...
Page 109: ...109 15 4 LOSS POWER...
Page 110: ...110 15 5 POOR HANDLING...