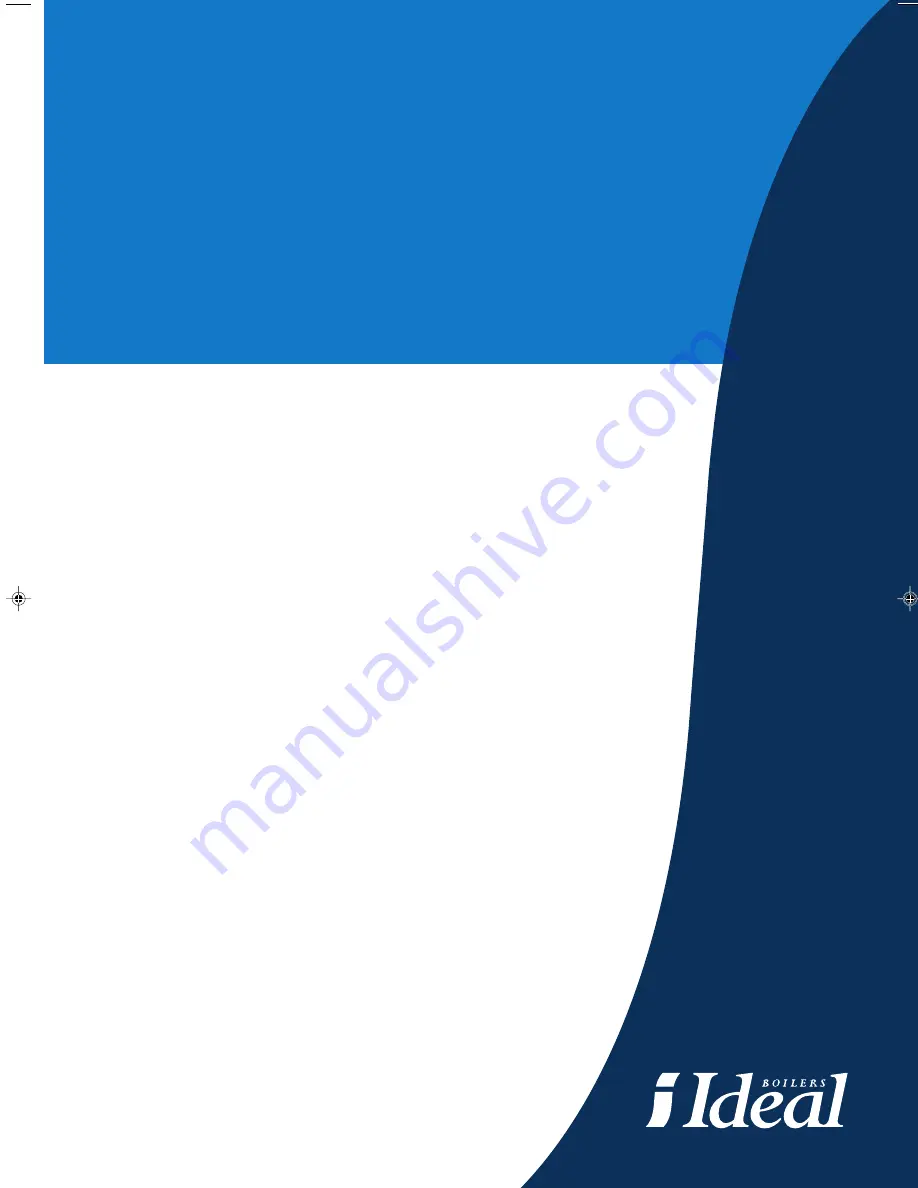
installation and
servicing
Mexico Super
Your Ideal installation and servicing guide
See reverse for
Mexico Super
users guide
ENGINEERED FOR PEACE OF MIND
When replacing any part on this appliance use only spare parts that you can be
assured conform to the safety and performance specification that we require. Do not
use reconditioned or copy parts that have not been clearly authorised by Ideal Boilers.
FF4100 & FF4125
June 2004 UIN 200 940 A02
200940-2.pmd
6/7/2004, 10:41 AM
1