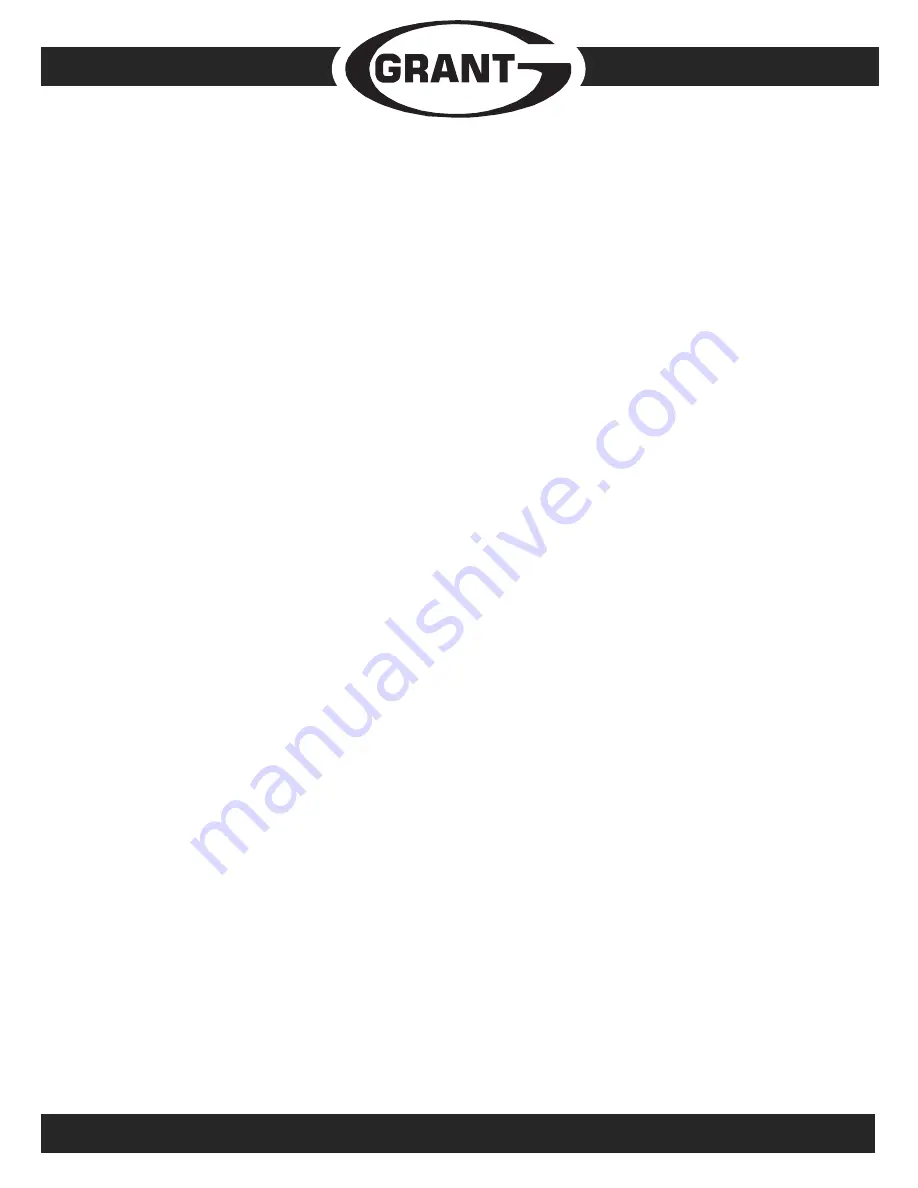
Part No. IRL 005 Rev: 0 Jan 07
USER, INSTALLATION
and
SERVICING INSTRUCTIONS
Outdoor Combi 90 V3
Combi Max
Outdoor Condensing Combi 26 and 36
For use with Kerosene or Gas Oil (Condensing Combi Kerosene only)
After installing the boiler leave these instructions with the User
This appliance is deemed a controlled service and specific regional statutory
requirements may be applicable