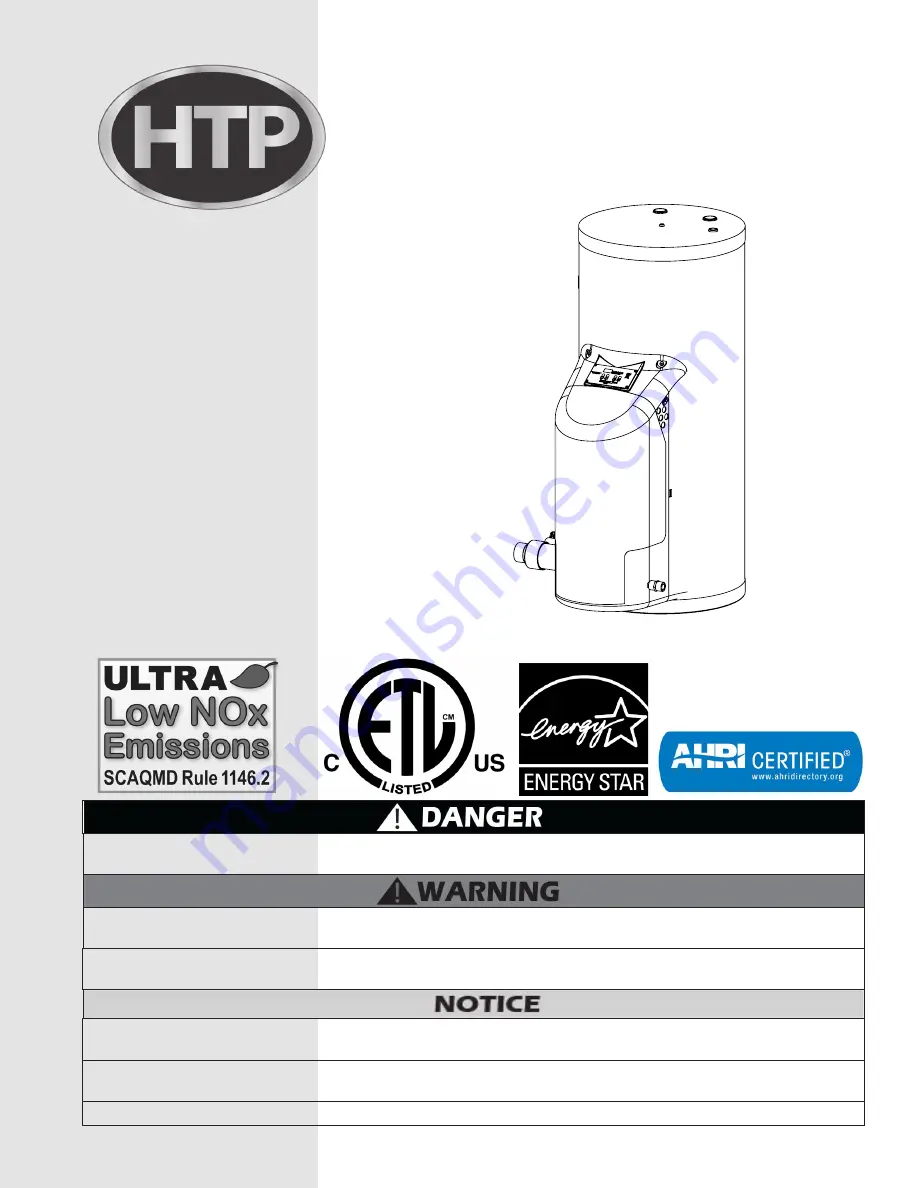
Pioneer
Heating Appliance
Installation
Start-Up
Maintenance
Parts
Warranty
PHR100 / 130 / 160 / 199 Models*
* “LP” Denotes Propane Gas Operation
This manual must only be used by a qualified installer / service technician. Read all instructions in this manual before installing.
Perform steps in the given order. Failure to do so could result in substantial property damage, severe personal injury, or death.
HTP reserves the right to make product changes or updates without notice and will not be held liable for typographical errors
in literature.
NOTE TO CONSUMER: PLEASE KEEP ALL INSTRUCTIONS FOR FUTURE REFERENCE.
272 Duchaine Blvd.
New Bedford, MA 02745
www.htproducts.com
LP-325 Rev. 009 Rel. 004 Date 12.2.20
Improper installation, adjustment, alteration, service, or maintenance could void product warranty and cause property
damage, severe personal injury, or death.
California Proposition 65 Warning: This product contains chemicals known to the State of California to cause cancer, birth
defects, or other reproductive harm.
The surfaces of these products contacted by potable (consumable) water contain less than 0.25% lead by weight as required
by the Safe Drinking Water Act, Section 1417.
This Manual For Use With Appliances Manufactured After
April 10, 2017