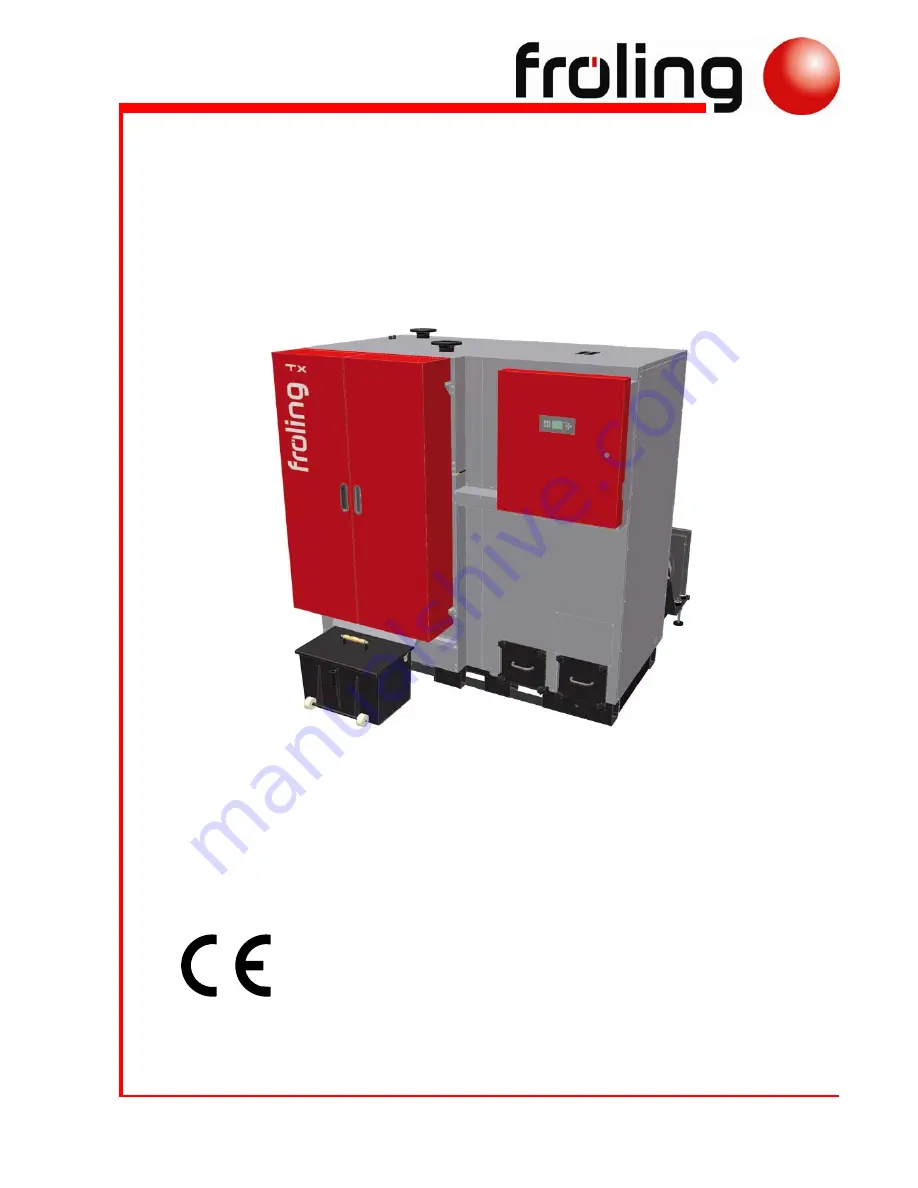
Fröling Heizkessel- und Behälterbau Ges.m.b.H
Industriestraße 12 A-4710 Grieskirchen
Tel +43 (0) 7248 606-0 Fax +43 (0) 7248 606-600 [email protected]
www.froeling.com
Operating Instructions
TX
English version of operating instructions for operators.
Read and follow the instructions and safety instructions!
Subject to technical change.