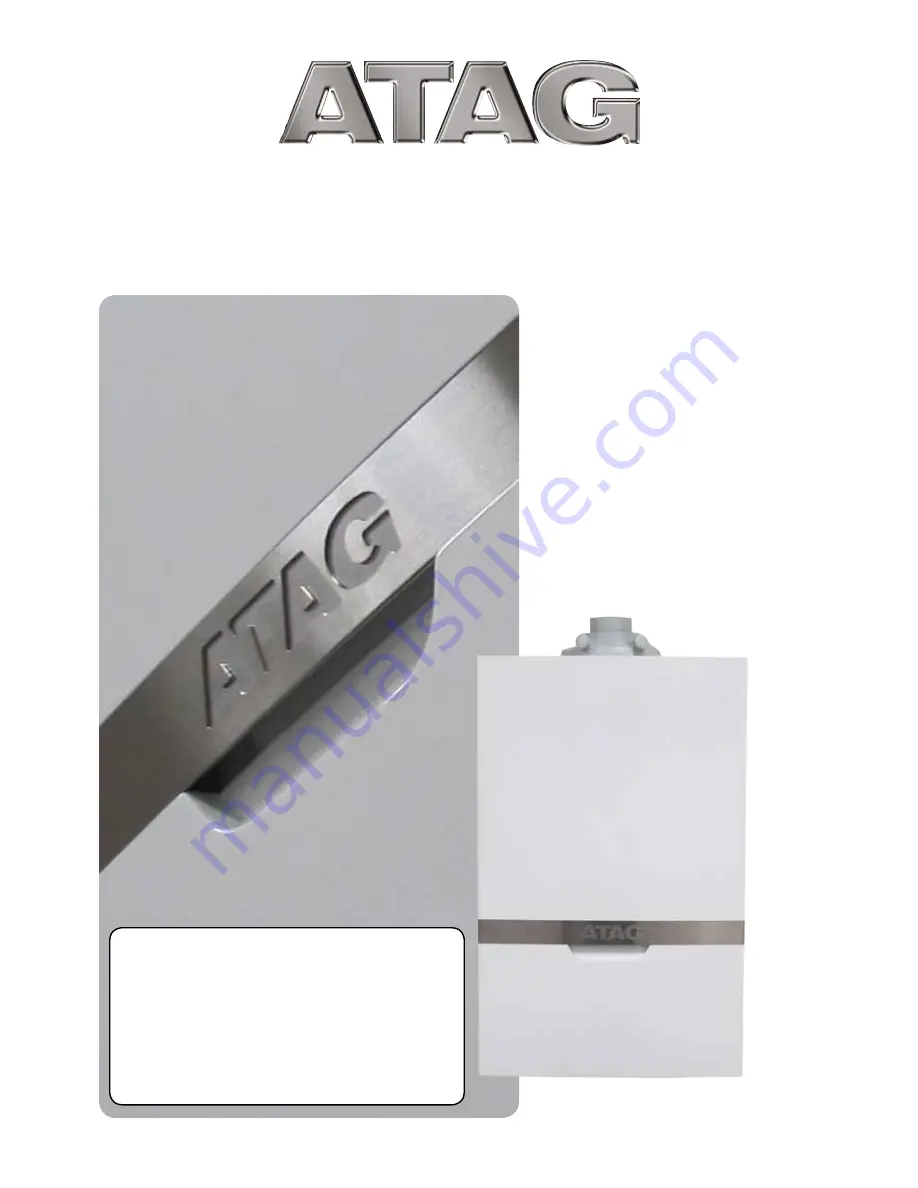
8G.51.82.04 / 09.16
Changes reserved. E.& O. E.
I n s t a l l a t i o n & S e r v i c i n g
Instructions
These instructions are to be retained by the user.
Natural Gas Boilers
Boiler
G.C No
iS 12
41-310-18
iS 15
41-310-20
iS 18
41-310-22
iS 24
41-310-24
iS 32
41-310-26
iS 40
41-310-28
Propane Gas Boilers
Boiler
G.C No
iS 12 LPG
41-310-19
iS 15 LPG
41-310-21
iS 18 LPG
41-310-23
iS 24 LPG
41-310-25
iS 32 LPG
41-310-27
iS 40 LPG
41-310-29
CE PIN 0063CQ3634
iS
12
iS
15
iS
18
iS
24
iS
32
iS
40