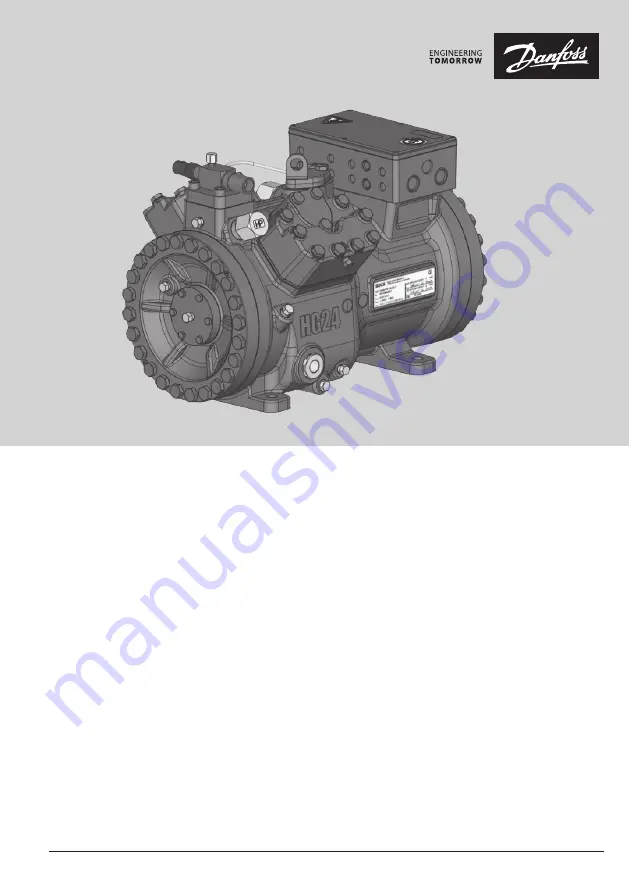
AQ452526009526en-000401
Operating guide
BOCK
®
HGX
2
4
CO
2
T
HGX24/55-4 ML CO
2
T
HGX24/35-4 S CO
2
T
HGX24/55-4 SH CO
2
T
HGX24/70-4 ML CO
2
T
HGX24/55-4 S CO
2
T
HGX24/70-4 SH CO
2
T
HGX24/90-4 ML CO
2
T
HGX24/70-4 S CO
2
T
HGX24/90-4 SH CO
2
T
HGX24/110-4 ML CO
2
T
HGX24/90-4 S CO
2
T
HGX24/110-4 SH CO
2
T
HGX24/110-4 S CO
2
T
HGX24/55 MLP 6 CO
2
T
HGX24/55 SP 7 CO
2
T
HGX24/55 SHP 7 CO
2
T
HGX24/70 MLP 7 CO
2
T
HGX24/70 SP 9 CO
2
T
HGX24/70 SHP 9 CO
2
T
HGX24/90 MLP 8 CO
2
T
HGX24/90 SP 12 CO
2
T
HGX24/90 SHP 12 CO
2
T
HGX24/110 MLP 10 CO
2
T
HGX24/110 SP 15 CO
2
T
HGX24/110 SHP 15 CO
2
T
Translation of the original instructions