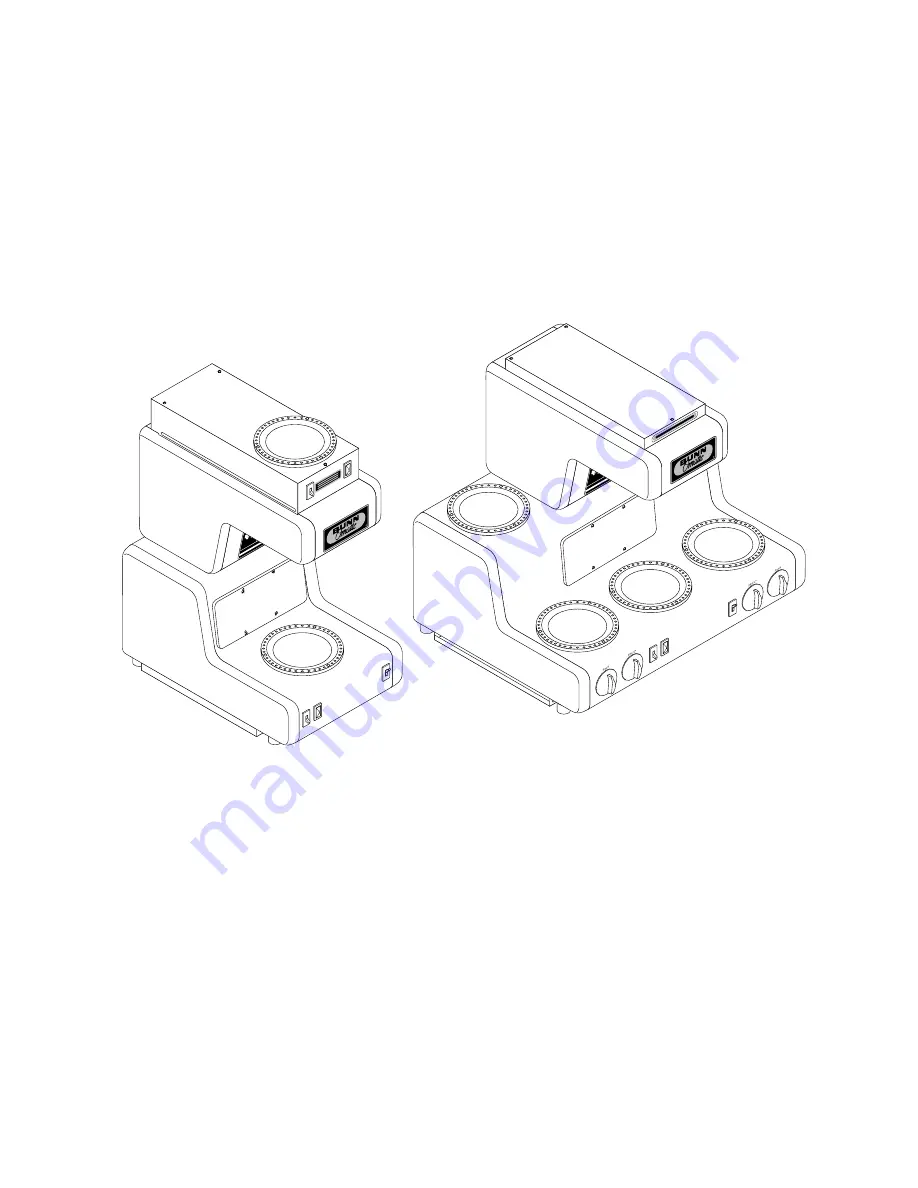
OT & RT
10021.0000G 7/00 © 1989 BUNN-O-MATIC CORPORATION
BUNN-O-MATIC CORPORATION
POST OFFICE BOX 3227
SPRINGFIELD, ILLINOIS 62708-3227
PHONE: (217) 529-6601 FAX: (217) 529-6644
BUNN
®
OPERATING & SERVICE MANUAL
WA
RN
IN
G
!
HIGH HEA
T W
ARMER
DO
N
OT
B
OIL
D
EC
AN
TE
R D
RY
KE
EP
C
OM
BU
ST
IB
LE
S A
WA
Y
FA
ILURE
TO
COMPL
Y RISKS
GLASS F
AILURE/HO
T LIQ
UID
BU
RNS AND FIRE H
AZARD
CAUTION
DIS
CA
RD
DE
CA
NT
ER
IF:
. C
RA
CK
ED
. S
CR
AT
CH
ED
. B
OIL
ED
DR
Y
. H
EA
TE
D W
HE
N E
MP
TY
. U
SE
D O
N H
IGH
FL
AM
E
. O
R E
XP
OS
ED
EL
EC
TR
IC
E
LE
ME
NT
S
FA
ILU
RE
TO
CO
MP
LY
RI
SK
S I
NJ
UR
Y
PN
: 6
58
19
85
BU
NN-O
-M
AT
IC C
OR
PO
RA
TIO
N
FU
NN
EL
CO
NT
EN
TS
AR
E H
OT
!
CAUTION
DIS
CA
RD
DE
CA
NT
ER
IF:
. C
RA
CK
ED
. S
CR
AT
CH
ED
. B
OIL
ED
DR
Y
. H
EA
TE
D W
HE
N E
MP
TY
. U
SE
D O
N H
IGH
FL
AM
E
. O
R E
XP
OS
ED
EL
EC
TR
IC
E
LE
ME
NT
S
FA
ILU
RE
TO
CO
MP
LY
RI
SK
S I
NJ
UR
Y
PN
: 6
58
19
85
BU
NN
-O
-M
AT
IC C
OR
PO
RA
TIO
N
FU
NN
EL
CO
NT
EN
TS
AR
E H
OT
!