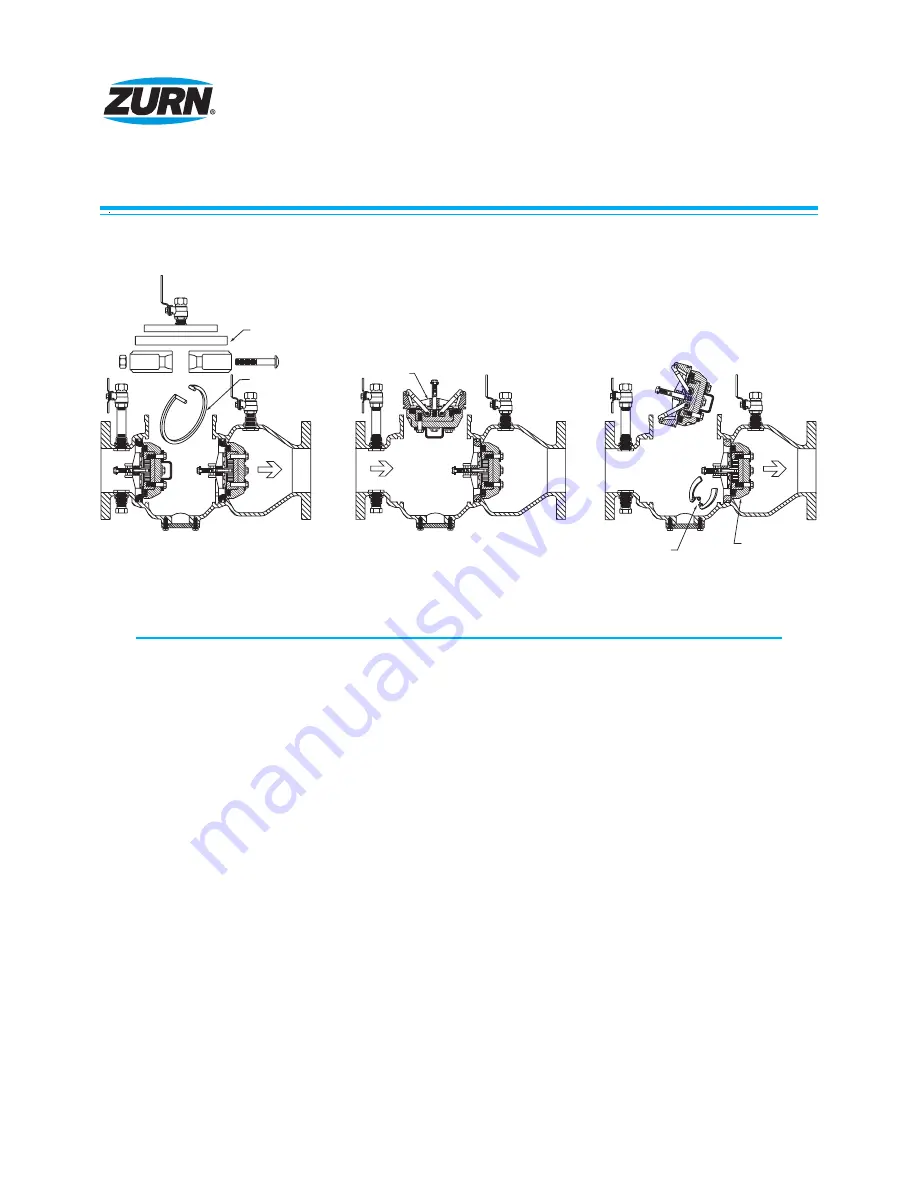
INST2018_Model350_65-250 Rev. 11/18
ZURN.COM.AU
ZURN WILKINS BACKFLOW
Double Check Valve Assembly
INSTALLATION & MAINTENANCE
MODEL 350 65-250mm
#2 PLATE RETAINER (4” & 6”)
(PLASTIC RETAINER MODELS 21/2” & 3”)
#2 CHECK ASSEMBLY
FIGURE 1
FIGURE 2
FIGURE 3
#1 CHECK ASSEMBLY
#1 RETAINER
GASKET
SERVICING CHECK VALVES
cont’d
PROBLEM
POSSIBLE
CAUSES
CORRECTIVE
ACTION
LEAKING CHECK VALVES
1. Debis on seat or seal ring
1. Clean seat area
2. Damaged seat area
2. Replace check assembly
3. Damaged seat o-ring
3. Replace seat o-ring
4. Damaged bolt o-ring(s) on check retainer
4. Replace o-ring(s)
LOW OR NO FLOW
1. Device installed backwards
1. Verify flow direction arrow
2. Gate valves not fully open
2. Turn handles counter-clockwise
3. Low supply pressure
3. Attach pressure gauge to testcock
#1 & verify pressure
TROUBLESHOOTING