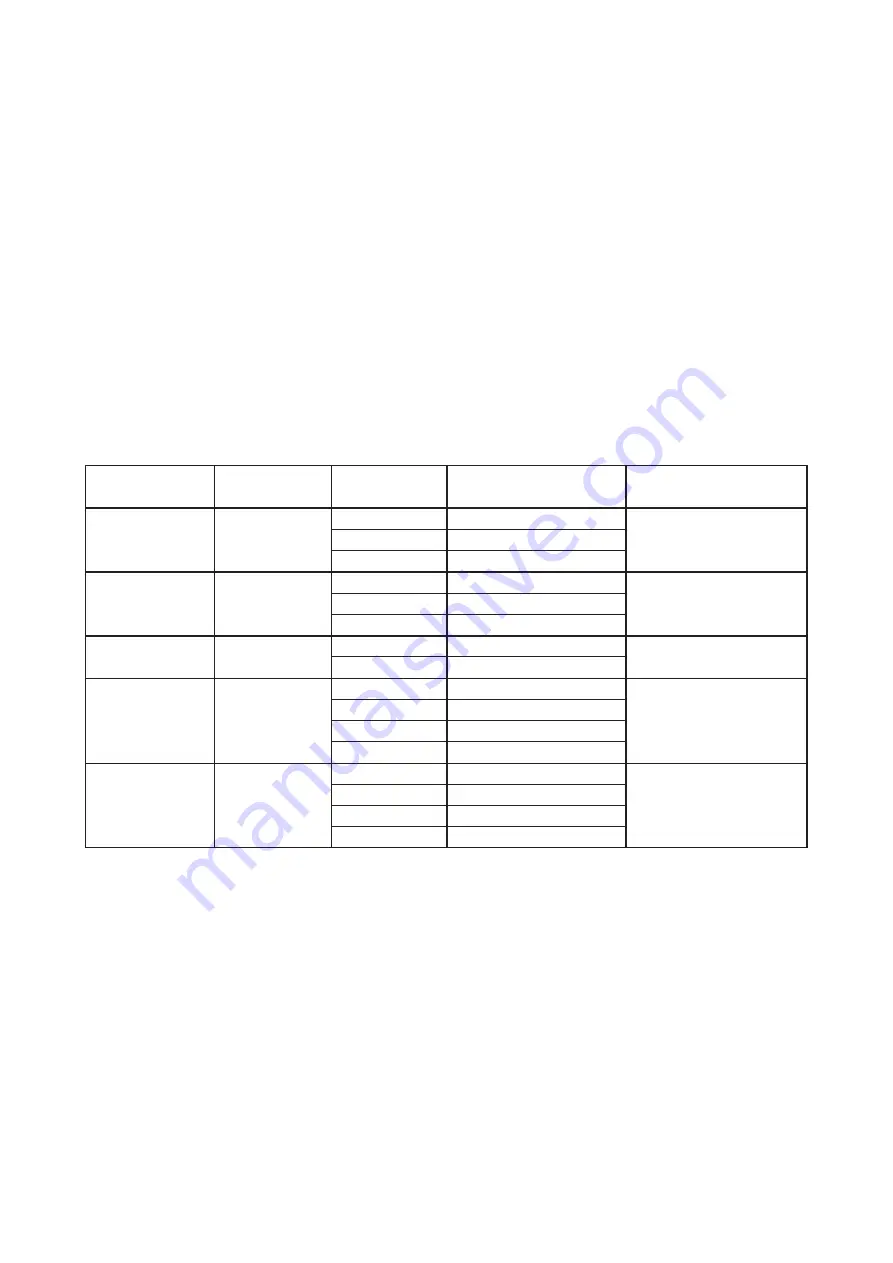
(position- and/or torque-limit)
of the actuator must be connected and set, and the position transmitter adjusted. If the
torque-limit switches are used as the limit switches it is necessary to verify that the actuator is able to exert required
tripping torque.
The auto-calibration should be started in each case of changed conditions, which can influence error-free function of
the regulator.
For instance, if adjustment of the actuator limit switches is changed or in case of a change in mechanical properties
of the valve
(tightened packing, replaced valve, etc.).
Function of push-buttons SW1 and SW2
The regulator parameters are set by means of the push-buttons SW1 and SW2.
Long pressing of the push-button
SW1 (L)
results in gradual change of the regimes Regulation, Setting and
Auto-calibration.
Long pressing of the push-button
SW2 (L)
is only used in common function with SW1 (L) in setting the backup parameters.
In the regime Setting, short pressing of the push-button
SW1
results is changing over between respective parameters;
short pressing of the push-button SW2 is used for choosing required value of the current parameter.
The procedure of setting the parameters is shown in the Graph.
The pilot lights
D3
and
D4
indicate the regulator response. In the regime Setting, blinking of
D3
signalizes the number
of current parameter and
D4
its chosen value.
Table shows in detail meaning of the signalization pilot lights and survey of values of respective parameters.
Values of parameters P1 – P5
Note to parameter
P5:
“Narrow”
– the actuator moves and/or steps exactly to the position determined by CS; parameter P4 is inactive.
“Wide” – the actuator moves and/or steps to the zone of insensitivity
(see parameter P4)
of the position determined
by CS.
“To torque”
– i n the vicinity of the limit values
(for the control signal 4 – 20 mA these values are smaller than 4.2 mA
a higher than 19.8 mA)
the actuator does not stop when the control and feedback signalsare identical but goes
on moving until the particular limit switch is activated. If the torque-limitswitch is connected as the limit switch
the valve is thus tightly closed.
“To position” – the actuator is always, even in the vicinity of the limit position, stopped in the position where FS = CS
(“narrow”)
or FS = CS – zone of insensitivity
(“wide”)
Recommended setting is “narrow, to position”.
Auto-calibration
The auto-calibration is started by shifting the position in the direction Open. To prevent an error, the actuator
should be set in advance to an intermediate position sufficiently distant from the limit positions. If the auto-calibration
is completed without errors the parameters are stored in the regulator memory and the regulator changes
17
Parametr
D3
(yellow)
D4
(red)
Value of parameter
Note
P1
Control signal
1x
P2
Response to signal
TEST and lost
control signal
2x
P3
Mirroring
3x
1x
0 – 20 mA
2x
4 – 20 mA
3x
0 – 10 V
1x
opens
2x
closes
3x
drive stop
1x yes
2x no
1x 1
%
2x 2
%
... …
10x 10
%
1x
narrow, to torque
2x
narrow, to position
3x
wide, to torque
4x
wide, to position
P4
Regulator
insensitivity
4x
P5
Regulation
method
5x
see Notes under
the table
FS - feedback signal
CS - control signal
lower signal opens
higher signal opens
Summary of Contents for Modact MOKP 100 Ex Series
Page 2: ......