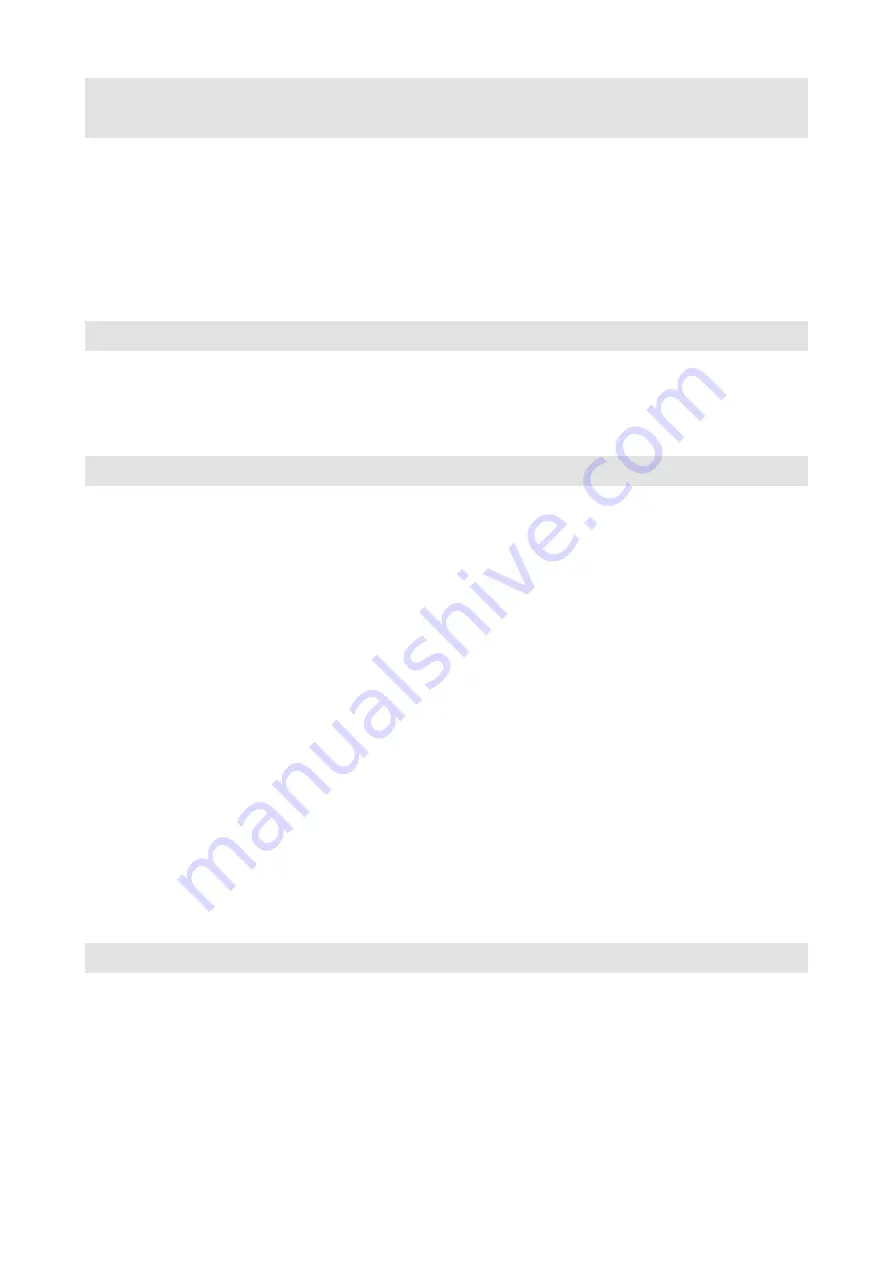
16
7. VERIFICATION OF FUNCTION OF THE DEVICE
AND PLACEMENT
Before starting to install the device, again check actuator for any damage suffered in the course of storage.
The function of electric motor can be verified by connecting it to power supply through a switch and by powering it
up shortly. It is sufficient to observe if the electric motor starts up and if the output shaft starts rotating. Actuators must
be located in an area providing easy access to manual control wheel, terminal box and control box. Also, i t must be
verified again if the location meets the provisions of section
“Operating Conditions”.
If local conditions require another
method of installation, manufacturer’s approval must be obtained.
For working position of rotary actuators see the paragraph
“Working position”.
8. INSTALLATION
Set actuator onto the valve so that its output shaft reliably fits into the valve coupling. Use four
(eight)
screws to
connect actuator with valve. Turn hand wheel to check correct connection between actuator and valve. Remove cover
of terminal box and carry out electrical connection of actuator according to internal connection diagram.
9. ACTUATOR ADJUSTMENT
Having fitted the actuator onto the valve and checked for correct mechanical connection, proceed with the actual set-up
and adjustment.
1. Shift the actuator manually to an intermediate position,
2. Connect actuator to power supply line, and shortly switch to verify correct rotation direction of the output shaft. When
looking inside the control box, the input shaft will rotate clockwise, while moving in
“closing"
direction.
3. Electrically set actuator close to
“closed”
position, use hand wheel to arrive precisely at the
“closed”
position. In this
“closed” position set the positional unit
(PZ micro-switch)
as under 5e and the resistance transmitter as under 5d,
4. Set output shaft to a position, where the signalling switch SZ is supposed to change over. Adjust SZ switch according
to instructions specified under point 5b.
5. Turn the actuator output shaft by the required number of revolutions and set switch to PO
“open”
position as described
under point 5e and resistance transmitter as described under point 5d. Several times verify the adjustment of position
and signalling switches, and the adjustment of resistive transmitter.
6. Set output shaft to a position, where the signalling switch SO is supposed to change over. Adjust SO switch according
to instructions specified under point 5b.
Notice
The control box cover must be removed by sliding it along the extended axis of the actuator output shaft while
avoiding any damage to position indicator. While installing valve onto pipe, use hand wheel of actuator to set the valve
into its central position. Shortly run the electric motor to verify if the actuator is rotating in the correct direction. If not,
swap over the two phase wires on the motor terminal board.
10. OPERATION AND MAINTENANCE
Correct operation of rotary actuators is determined by operational conditions and is usually limited to giving
impulses for the various functional tasks. In the event of power supply interruption, change the position of the
controlled valve by means of hand wheel. If the actuator is connected to automatic control circuit
(this does not
mean regulating operation),
we recommend you to install elements for remote control in the circuit so that the
actuator can be operated also in case of such automatic control circuit breakdown.
Operating personnel must ensure that the prescribed maintenance is carried out and that the actuator is
protected against harming ambient impacts and weather conditions unspecified in section
“Operating Conditions”.
Torques in the actuators are set and operate if the actuator is energized. In the case that manual control is used,
ie. the actuator is controlled mechanically, the torque setting does not work and can cause damage to the valve.