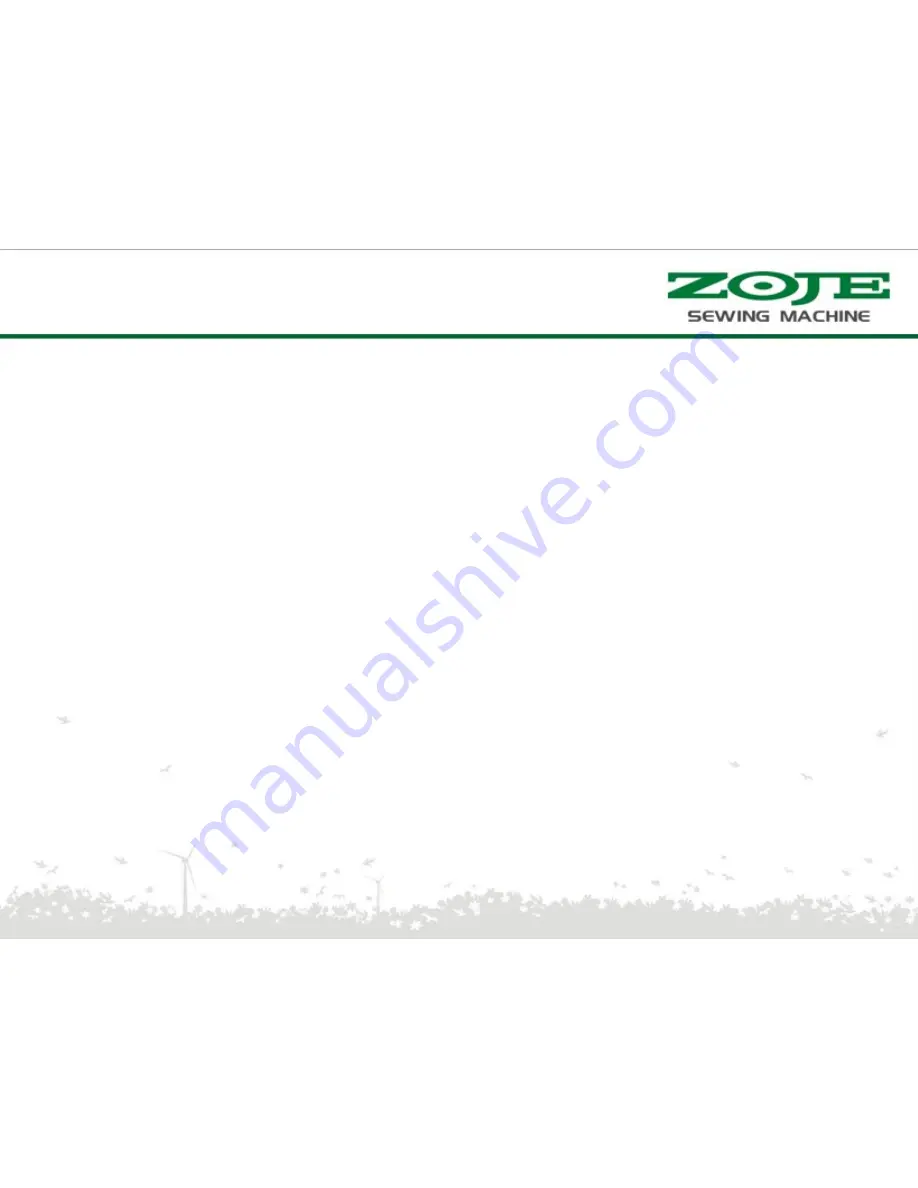
Safety Precautions
•
1, control box working voltage range :180V-260V.
•
2, Keep away from the high-frequency electric machinery to avoid
signals interference
•
3 Make sure the ground line is well conneted.
•
4 Machine is forbidden to work in high humidity environment.
•
5 when testing machine, do not plug or unplug when the power is on.
•
6 For safety considerations; please use 80V electric power
isolation transformer when repairing,
Following the above instruction will effectively ensure the life of
the machine and ensure staff safety.
Summary of Contents for WR580
Page 1: ...WR580 PRODUCT MANUAL V1 0 ...
Page 2: ...Application Model Code Hardware Structure Error Solution Catalogue ...
Page 5: ...Composition of the product ...
Page 9: ...Model description motor Motor model serial number ...
Page 21: ...Function Aging mode Press to enter the aging mode Then press to start press again to stop ...
Page 24: ...External interface definition power 1 2 3 4 Ground wire Power Socket definition L N ...
Page 28: ...Main board PCBA appearance ...
Page 29: ...Control box theory diagram ...
Page 60: ...谢 谢 ...