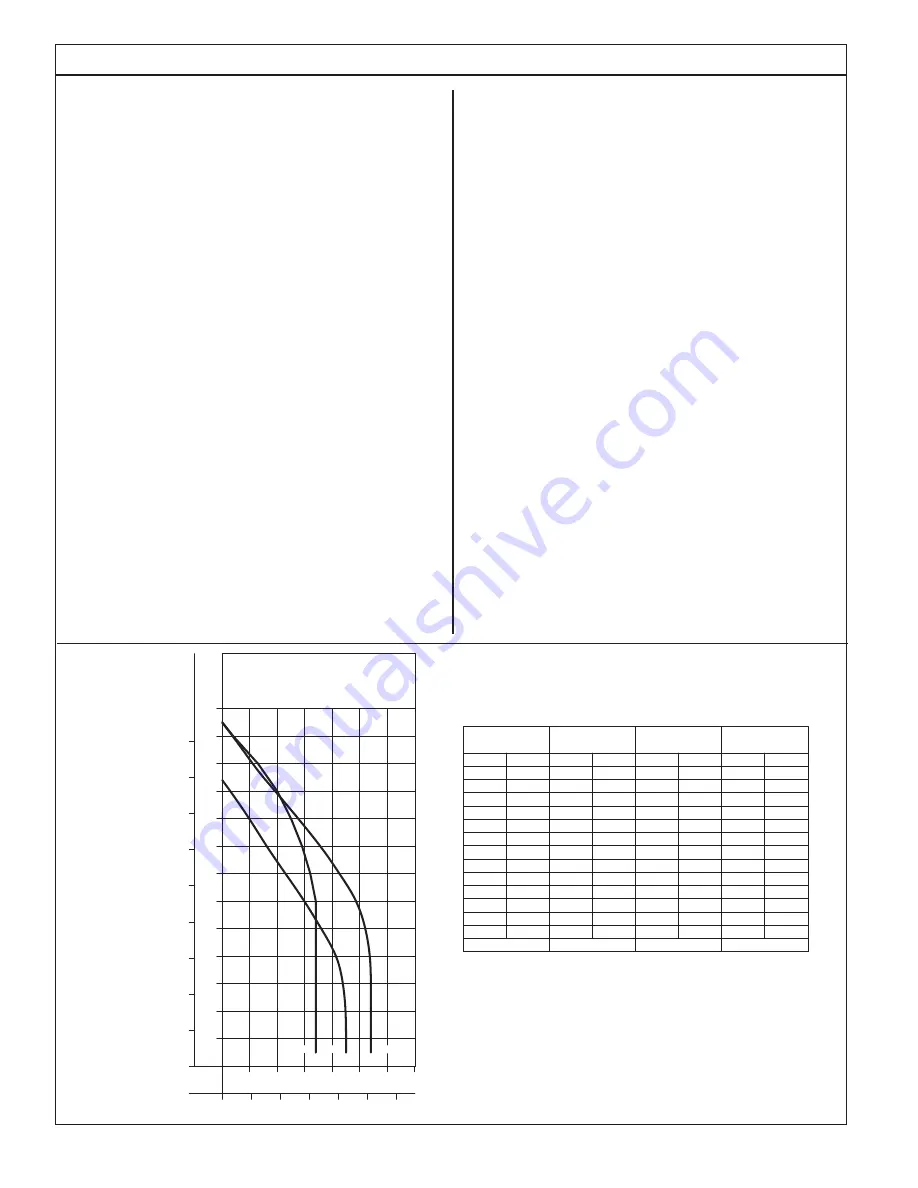
4
© Copyright 2015 Zoeller
®
Co. All rights reserved.
General Information
GRINDER PUMP DESCRIPTION
1. Pumps are constructed of class 30 cast iron protected with powder
coated epoxy for long life when pumping sewage in submersible
applications. The cutter assembly is comprised of stainless steel
components hardened to a value of 55-60 on the Rockwell C scale;
a star shaped cutter and a precision ground flat disk. Cutting action
takes place with the rotation of the star cutter at 3450 RPM against
the stationary cutter plate (see page 11).
2. The cutter mechanism on the model X840 is bidirectional, enabling
it to cut in either direction. A control panel with the reversing feature
will alternate the pump’s rotational direction with each duty cycle. The
cutter mechanism on the model X842 & X841 is single directional.
3. Pump motors are available in single and three phase design. Single
phase motors require a Zoeller approved starting relay, starting
capacitor and a run capacitor, which are mounted in a control panel
(ref. page 5).
4. The X800 Series Grinder Pumps are dual seal and have seal leak
probes. Single phase units have an internal thermal overload. Three
phase pumps have a thermal sensor.
5. Three phase pumps require overload protection in the control
panel.
6. A Grinder Pump is an intermittent duty pump designed for pumping
sanitary sewage. It is not a dewatering or trash pump.
FIELD ASSEMBLED INSTALLATION
1. Installation and piping instructions are included with the control panel,
rail system and basin instructions. If pump is being retrofitted to an
existing rail system, accessory parts may be required. Consult the
factory and advise make and model of rail system being used.
2. Refer to the appropriate Indoor/Outdoor prepackaged instructions
on pages 6-9 for more information on system installation.
3. All electrical connections including pump to control box and power
supply to control panels must comply with the “National Electrical
Code” and applicable local codes. Conduit and panel enclosure
openings must have a gas and watertight seal. Installation of
electrical panels, conduit and connections should be made by a
qualified licensed electrician. A UL Listed potting kit, P/N 10-2350,
is available from Zoeller Company.
4. A properly sized disconnect switch, supplied by others, shall be
installed on the service side of the pump and control panel.
5. When installing a pump with a check valve, or a rail system with
a check valve, you must give the pump case time to fill to help
prevent air lock when lowering the unit into the liquid. The pump
case has an air vent located behind the discharge. This air vent is
across the pump housing mounting surface and must be cleaned
before each reinstall. An extra air vent hole (3/16") may be drilled
in discharge pipe below the check valve to help prevent air lock.
This drilled hole must be cleaned before each reinstall. After the
pump is installed, run the unit submerged to assure the pump case
is filled (Water should come out of 3/16" diameter hole).
FIGURE 1.
016532
HEAD CAPACITY CURVE
MODEL X840/X841/X842
0
40
80
120
160
200
240
70
60
50
40
30
20
10
0
10
4
8
12
16
20
130
70
60
50
40
30
20
FLOW PER MINUTE
GALLONS
LITERS
TO
TAL D
YNAMIC HEAD
80
90
28
24
METERS
FEET
100
110
120
32
36
X840
X841
X842
TOTAL DYNAMIC HEAD/FLOW
PER MINUTE
SEWAGE
MODEL
Feet
Shut-off Head:
X840
Meters
Gal.
Liters
5
10
20
30
9.1
6.1
3.0
1.5
44
45
167
170
104 ft (31.7 m)
60
50
40
90
80
70
110
100
120
12.2
15.2
18.3
21.3
24.4
27.4
30.5
33.5
36.6
42
36
30
114
136
159
23
16
10
38
61
87
3
--
--
--
--
11
125 ft (38.1 m)
X841
Gal.
Liters
45
170
45
170
125 ft (38.1 m)
95
25
13
4
20
76
49
15
34
32
29
34
34
34
34
129
121
110
129
129
129
129
X842
Gal.
34
34
129
129
Liters
52
49
185
197
43
36
28
106
136
163
19
11
4
15
42
72
54
204
54
204
54
204
54
204
54
204