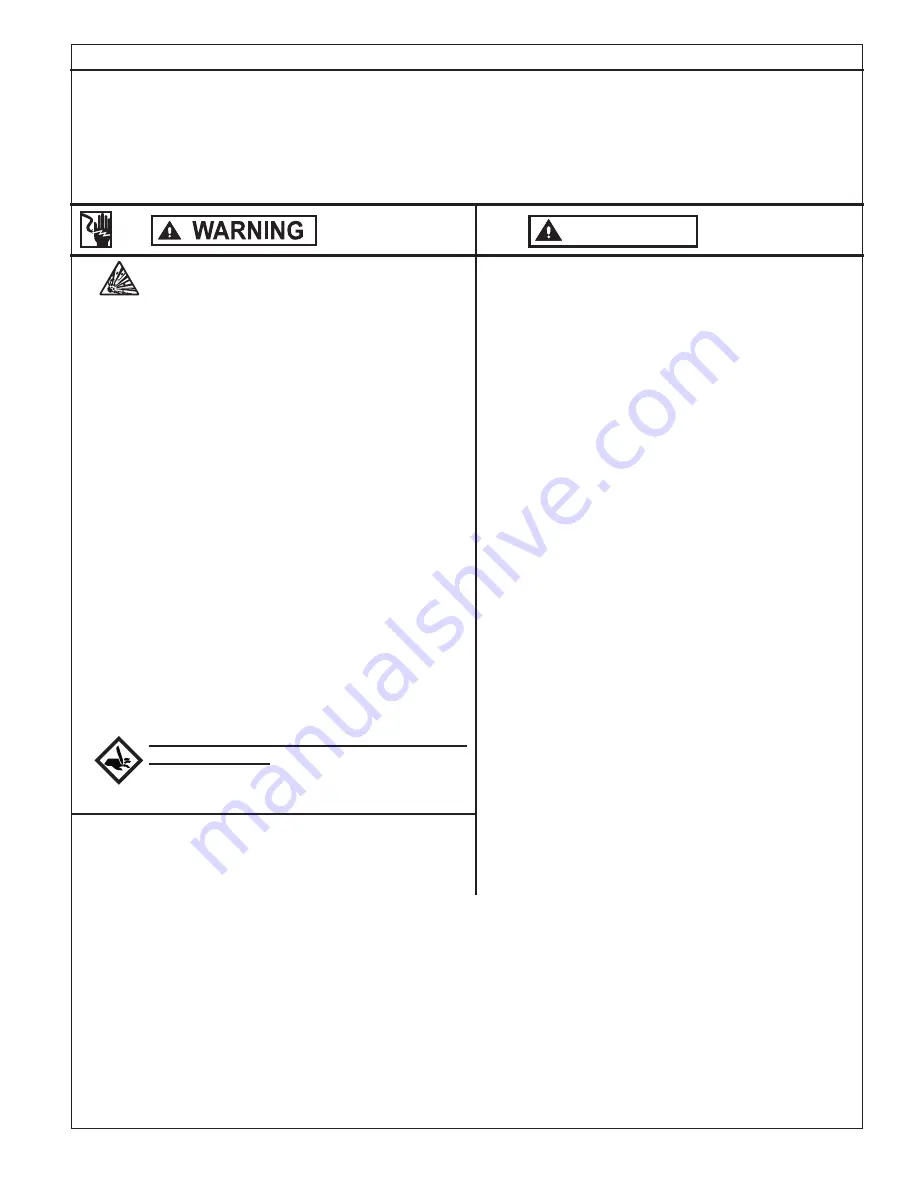
3
© Copyright 2015 Zoeller
®
Co. All rights reserved.
Preinstallation Information
1. Inspect your pump.
Occasionally, products are damaged during shipment. If the unit is damaged, contact your distributor before using.
DO
NOT
remove the test plugs in the cover nor the motor housing.
2. Carefully read the literature
provided to familiarize yourself with specific details regarding installation and use. These materials should be
retained for future reference.
3. National Electrical Code (NEC) articles 500 through 503 explain in detail the requirements for the installation and wiring of electrical
equipment in hazardous locations.
1
. Check to be sure your power source is capable of handling the
voltage requirements of the motor, as indicated on the pump
nameplate.
2.
The float switches must be connected to an intrinsically safe
circuit in the control panel. The installation of float switches is the
responsibility of the installing party and care should be taken that
the tethered float switch will not hang up on the pump apparatus
or pit peculiarities and is secured so that the pump will shut off. It
is recommended that rigid piping and fittings be used and the pit
be 36" or larger in diameter.
3. INFORMATION - VENT HOLE PURPOSE.
It is necessary that
all submersible pumps capable of handling various sizes of solid
waste be of the bottom intake design to reduce clogging and seal
failures. If a check valve is incorporated in the installation, a vent
hole (approx. 3/16") must be drilled in the discharge pipe below
the check valve and pit cover to purge the unit of trapped air. Water
stream will be visible from this hole during pump run periods. This
vent hole should be checked periodically for clogging and cleaned
as necessary. Trapped air is caused by agitation and/or a dry basin.
4.
Water hammer creates momentary high pressure surges. These
surges can cause severe damage to check valves and the piping
system. Consideration for water hammer must be included in the
piping system design. Reference ASPE Data Book, Chapter 2.33.
Some systems may require external spring or lever weighted check
valves or other engineered solutions.
5.
Three phase pumps must be connected for proper rotation, which
is counterclockwise looking into impeller inlet. See page 4 for
instructions for checking 3 phase rotation.
6.
Grinder installations should be checked frequently for debris and/
or buildup which may interfere with the “ON”/”OFF” cycles or the
positions of variable level float control switches. For repair and
service, other than cutter assembly maintenance, contact factory.
7.
Care should be taken during the initial installation to be sure that
adequate air supply is available whenever any person is in the basin.
Always follow OSHA guidelines on confined space requirements.
NOTE: CSA Certified pumps are certified to CSA Standard C22.2 No. 145.
CAUTION
SEE BELOW FOR
LIST OF CAUTIONS
SEE BELOW FOR
LIST OF WARNINGS
1.
Not for use in acidic atmospheres.
2.
Do not lift, carry, or hang pump by the electrical cables. Damage to
the electrical cables can cause shock, burns or death.
3. Make sure there is a properly grounded connection available.
All pumps are furnished with provisions for proper grounding to help
protect you against the possibility of electrical shock.
4.
Make certain that the control box is within the reach of the pump’s
power supply cord.
DO NOT USE AN EXTENSION CORD.
Extension
cords that are too long or too light do not deliver sufficient voltage
to the pump motor. But, more important, they could present a safety
hazard if the insulation were to become damaged or the connection
end were to fall into the sump.
5. Make sure the pump electrical supply circuit is equipped with
fuses and disconnect or circuit breakers of proper capacity.
A
separate branch circuit is recommended, sized according to the “Na-
tional Electrical Code” for the current shown on the pump nameplate.
6.
Risk of electric shock - These pumps have not been investigated for
use in swimming pool areas.
7.
According to the state of California (Prop 65), this product contains
chemicals known to the state of California to cause cancer and birth
defects or other reproductive harm.
8.
Electrical wiring and protection
must
be in accordance with the National
Electrical Code per NEC articles 500 through 503 for installation in
Class
I
, Division 1, Group C & D environments, and any other ap-
plicable state and local electrical requirements.
9.
Do not attempt to turn cutter rotor located on bottom of
the unit with fingers.
Use the appropriately sized wrench
when checking or removing the cutter.