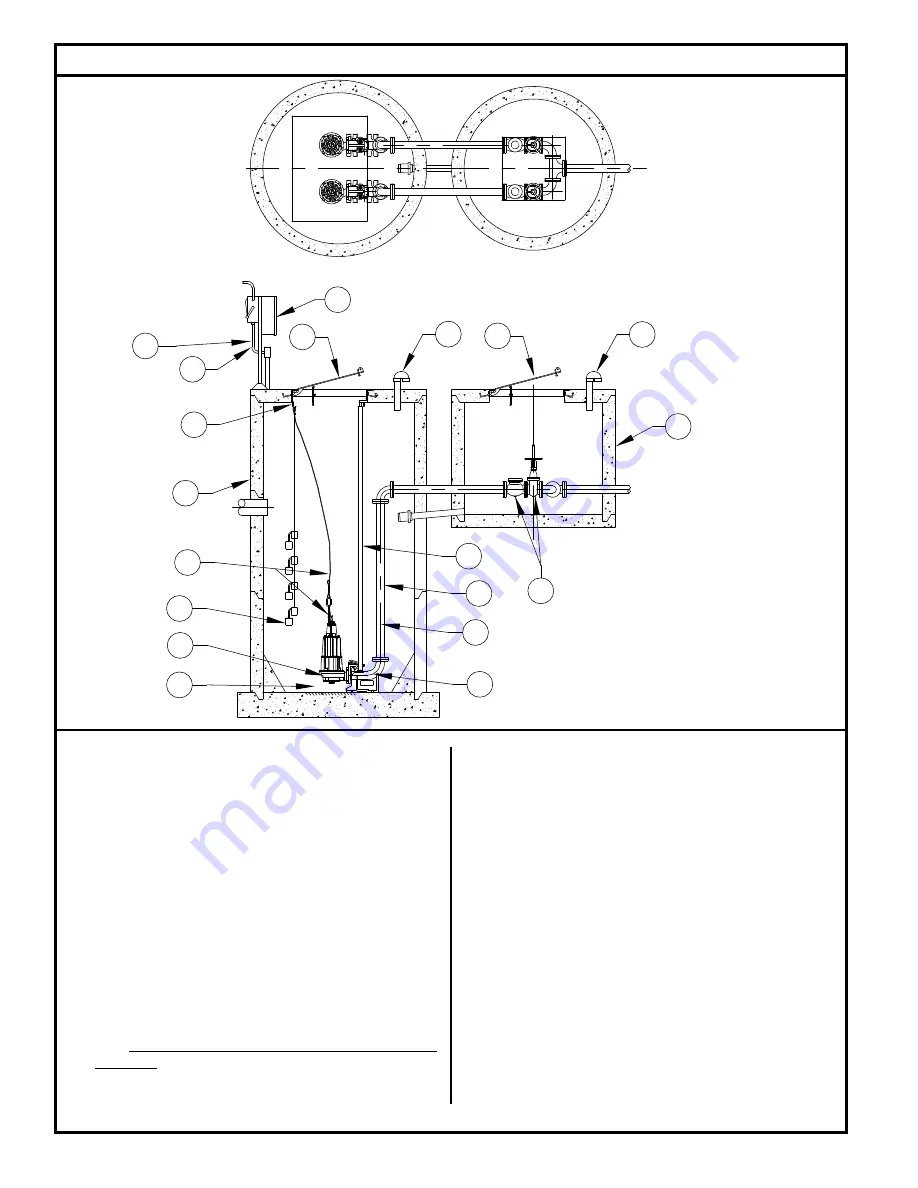
4
© Copyright 2020 Zoeller
®
Co. All rights reserved.
Typical Grinder Pumping System Installation
(8) Secure power cord to avoid entanglement with variable level
float switch mechanism.
(9)
Do not
reduce pump discharge pipe below 2” IPS size.
(10) Basin
must
be in accordance with all applicable codes
and specifications regarding Class I, Division 1, Group C &
D Class I, Zone 1, Groups IIA & IIB locations. Basin must be
sized to allow a minimum 3 minute off-time between starts.
(11) The tethered variable level float switches must be free and not
hang up on pump or pit peculiarities. Float switch circuits shall
be intrinsically safe.
(12)
If
a rail system is used, it should be non-sparking. Discharge
elbow
must
be firmly anchored to the bottom of basin. In
fiberglass basin, the bottom will need to be reinforced if the
discharge elbow is used.
(13)
If
a rail system is used, it should be non-sparking. The guide
rails are 2” schedule 40 pipe for all units. Brass, stainless steel
or galvanized steel is recommended.
(14) Install ring and cable for lifting pump from pit.
(15) Basin must be clean and free of debris after installation and
before operation.
All installations must comply with all applicable
electrical and plumbing codes, including, but not
limited to, National Electrical Code, local, regional,
and/or state plumbing codes, etc.
ZEPA0560
(1) Electrical wiring and protection
must
be in accordance with the
National Electrical Code per NEC articles 500 through 503 for
installation in Class I, Division 1, Group C & D Class I, Zone 1,
Groups IIA & IIB locations, and any other applicable state and
local electrical requirements.
(2) Install proper full flow check and shut-off valve.
(3) Install proper controls (outdoor panels in ventillated areas
require
NEMA 3R or 4X enclosure). Float switch connections shall be
intrinsically safe.
(4) All installations
require
a basin cover to prevent debris from falling
into the basin and to prevent accidental injury.
(5) Cords must be properly sealed per NEC articles 500 through 503
for installation in Class I, Division 1, Group C & D Class I, Zone 1,
Groups IIA & IIB locations, to prevent moisture and gases from
entering the control panel.
(6)
When check valve is installed
, drill a 3/16" diameter hole in the
discharge pipe below the check valve even with the top of the
pump. NOTE: The hole must be below the basin cover and cleaned
periodically. Also a vent hole is drilled in the pump housing. Be
sure that this hole is cleared during any servicing.
(7) Vent gases and odors to the atmosphere through vent pipe per
local and state codes.
9
10
5
1
8
4
3
4
7
10
7
15
6
14
11
12
13
2
6