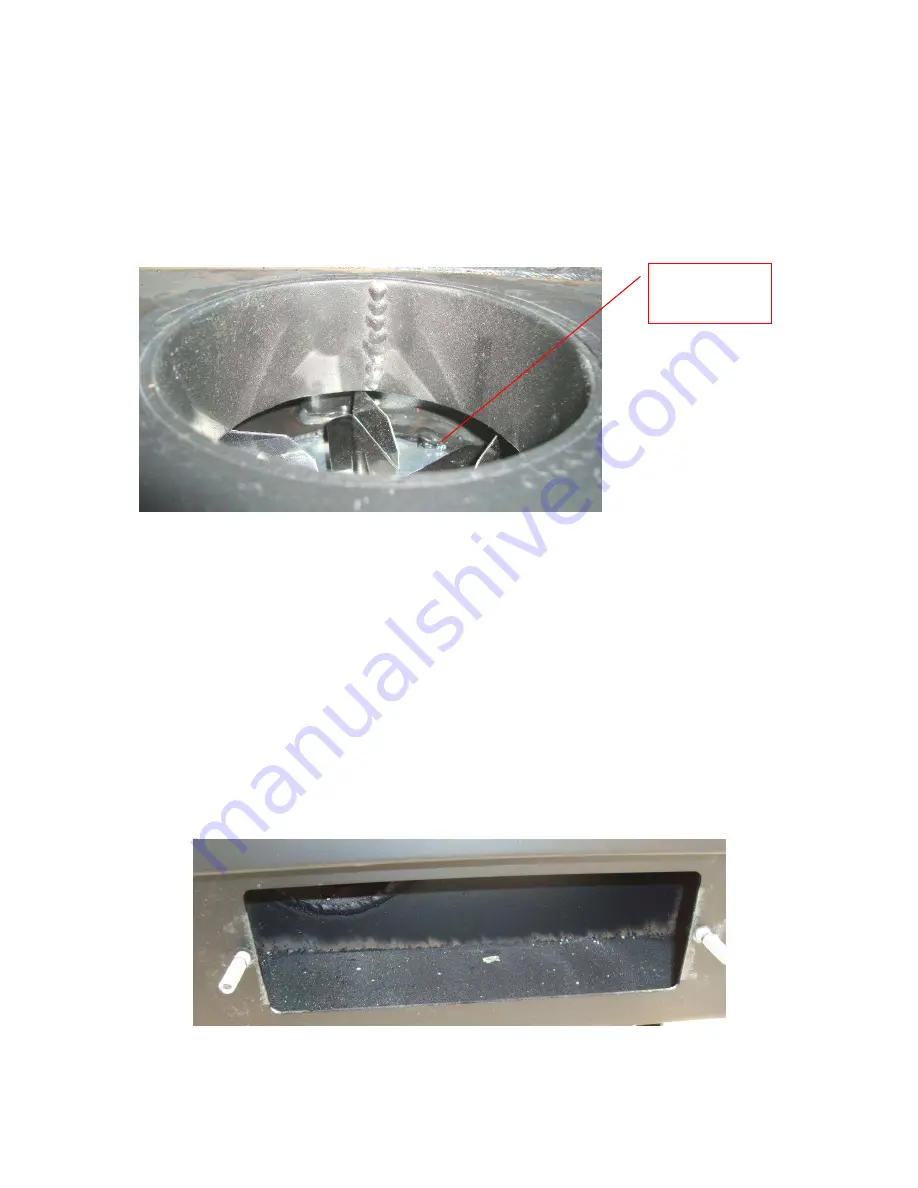
p. 58/69
After the convective duct of the boiler has been cleaned out from the deposited
ash, it is recommended to clean (or at least check the condition) the turbine of
the flue gas fan of the boiler – this procedure should be carefully done.
ATTENTION – clean the deposited ash as well as other tar residues of the
turbine of the flue gases fan by using a soft brush (do not use any wire brush or
any other stiff cleaning tool), by operating through the inlet of the flue gases fan
orifice.
Figure 5.20. View of the inlet orifice of the flue gases fan;
EXPLANATION : it is highly recommended to detach the flue gas fan and to
clean it thoroughly, next it should be carefully installed back on the boiler,
considering the gasket and the its tightness. The flue gas ash cleaning procedure
should be performed at switched off electrical power supply of the boiler, as
well as unplugged power supply cable of the boiler – this requirement is
obligatory;
After the ash residue of the heat exchanging surfaces has been brushed and
cleaned, the lid of the lower orifice of the convective duct should be opened -
the ash particles are collected in the volume of this section of the boiler – see the
following figure.
Figure 5.21. View of the orifice for ash removal from the lower section of the
convective section of the boiler;
Turbine of the
flue gases fan