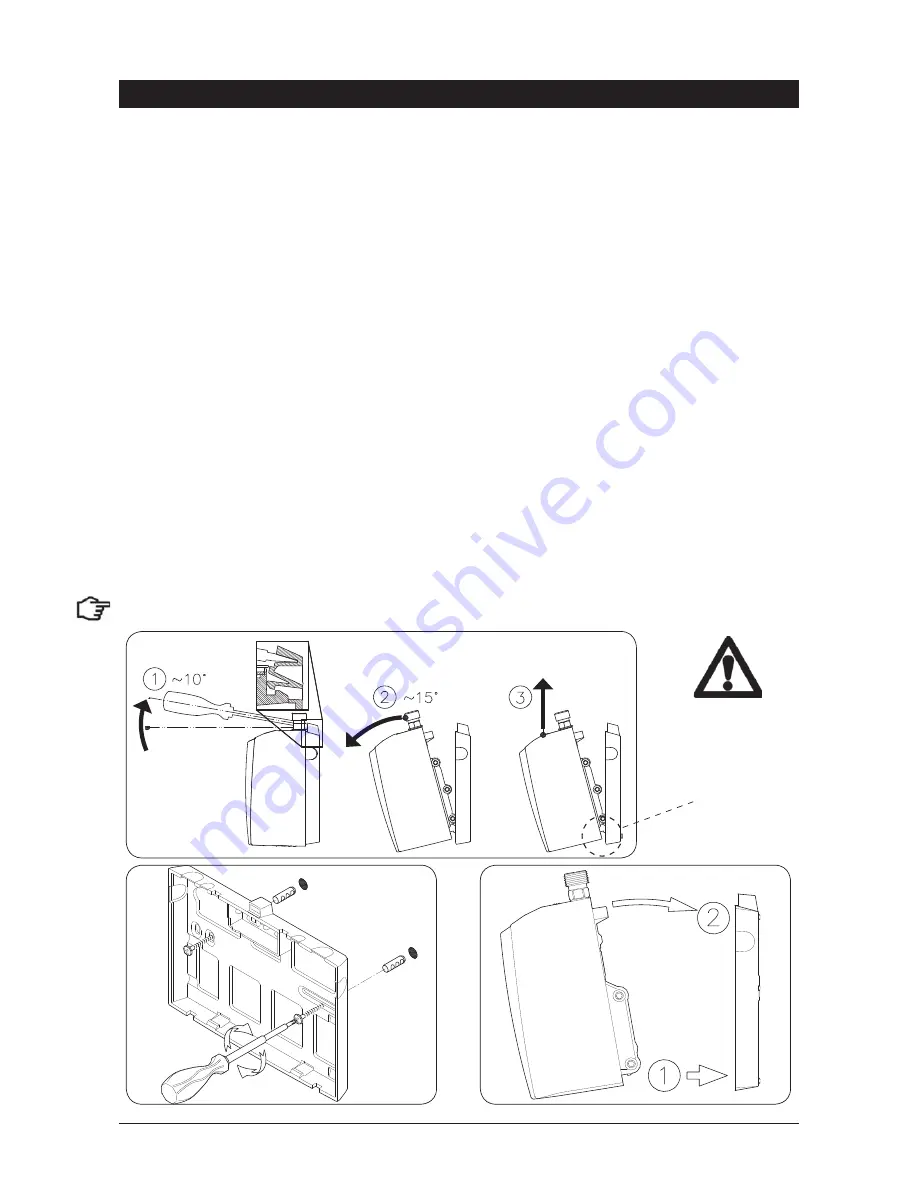
802265 - Sparkling HT- BCS Compact Commercial - Installation Instructions - 09.16 - v3.01
Page 15 of 28
Booster Installation
3.2
Installation Procedure
Site requirements
•
Appliance must only be installed in a frost-free area. Never expose appliance to frost.
•
The Appliance is designed for wall mounted Installation and must to be installed with water connectors
facing upwards.
•
The appliance complies with protection class IP 25.
•
The 400mm braided hoses supplied with the unit cannot be lengthened.
•
The 90
°
elbow hose ends, should be fitted to the inlet and outlet connections on top of the Booster.
•
The hot water outlet hose must be thermally insulated with the insulation provided.
Tilt Forward
Lift UP
Release
NOTE:
Remove the backing plate for wall mounting
3.3
To Remove / Install the appliance
1.
Insert a flat head screwdriver all the way into the lock.
2.
Gently angle the screwdriver upwards by approximately 10° as shown in the image below.
3.
Pull the appliance forwards by approximately 15° as shown.
4.
Carefully pull the appliance upwards to complete the removal process. Taking care not to break the
lower clips.
5.
To install; Place the appliance on the wall bracket and snap into position (See installation below).
Take care
not to break
the lower
clips when
removing or
installing the
Booster
Installation