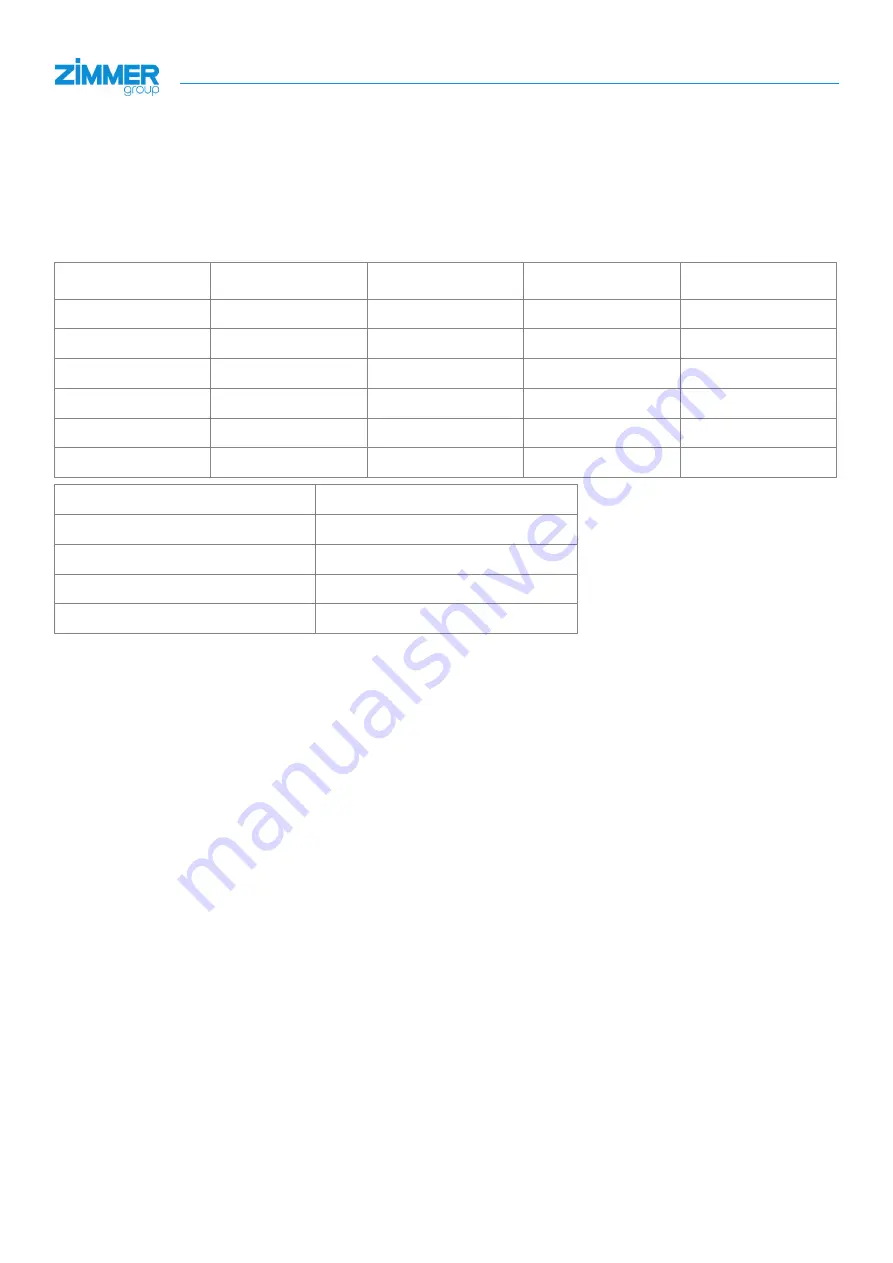
26
DDOC00247 / d
EN / 2020-07-20
Zimmer GmbH
●
Im Salmenkopf 5
●
77866 Rheinau, Germany
●
+49 7844 9138 0
●
+49 7844 9138 80
●
www.zimmer-group.com
INSTALLATION AND OPERATING INSTRUCTIONS:
Gripper, pneumatically intelligent, GPP/GPD5000-IL series
8.3.4 "TeachPosition" parameter
"TeachPosition" is used to tell the gripper at which position the workpiece is expected. The "PositionTolerance" functions
around this position. Thus the gripper can distinguish whether a correct or incorrect workpiece has been gripped. Confirma
-
tion that the correct workpiece has been gripped is communicated to the control system via the "StatusWord" parameter. If
the detection is correct, the "Teach" bit is set, thereby giving the user the option to monitor this work step.
By means of the position measuring system, it is possible to achieve a "TeachPosition" accuracy of +/- 0.05 mm.
The following values are to be used:
Product
Stroke per gripper
jaw
"BasePosition"
"WorkPosition"
"TeachPosition"
GPP/GPD5006IL
6 mm
0
1200
0 to 1200
GPP/GPD5008IL
8 mm
0
1600
0 to 1600
GPP/GPD5010IL
10 mm
0
2000
0 to 2000
GPP/GPD5013IL
13 mm
0
2600
0 to 2600
GPP/GPD5016IL
16 mm
0
3200
0 to 3200
GPP/GPD5025IL
25 mm
0
5000
0 to 5000
Name
"TeachPosition"
Data format
UINT16
Permission
Write
Transfer
Cyclical
Value range
0 to max. jaw stroke of the gripper
Example: GPP5006IL
• Full stroke of 6 mm per gripper jaw.
• "BasePosition" = 0
• "WorkPosition" = 1200
Ö
(2*6*100
2 gripper jaws * 3 mm stroke per gripper jaw * Resolution at 1/100 mm)
• The "TeachPosition" can acquire values from 0 to 1200.