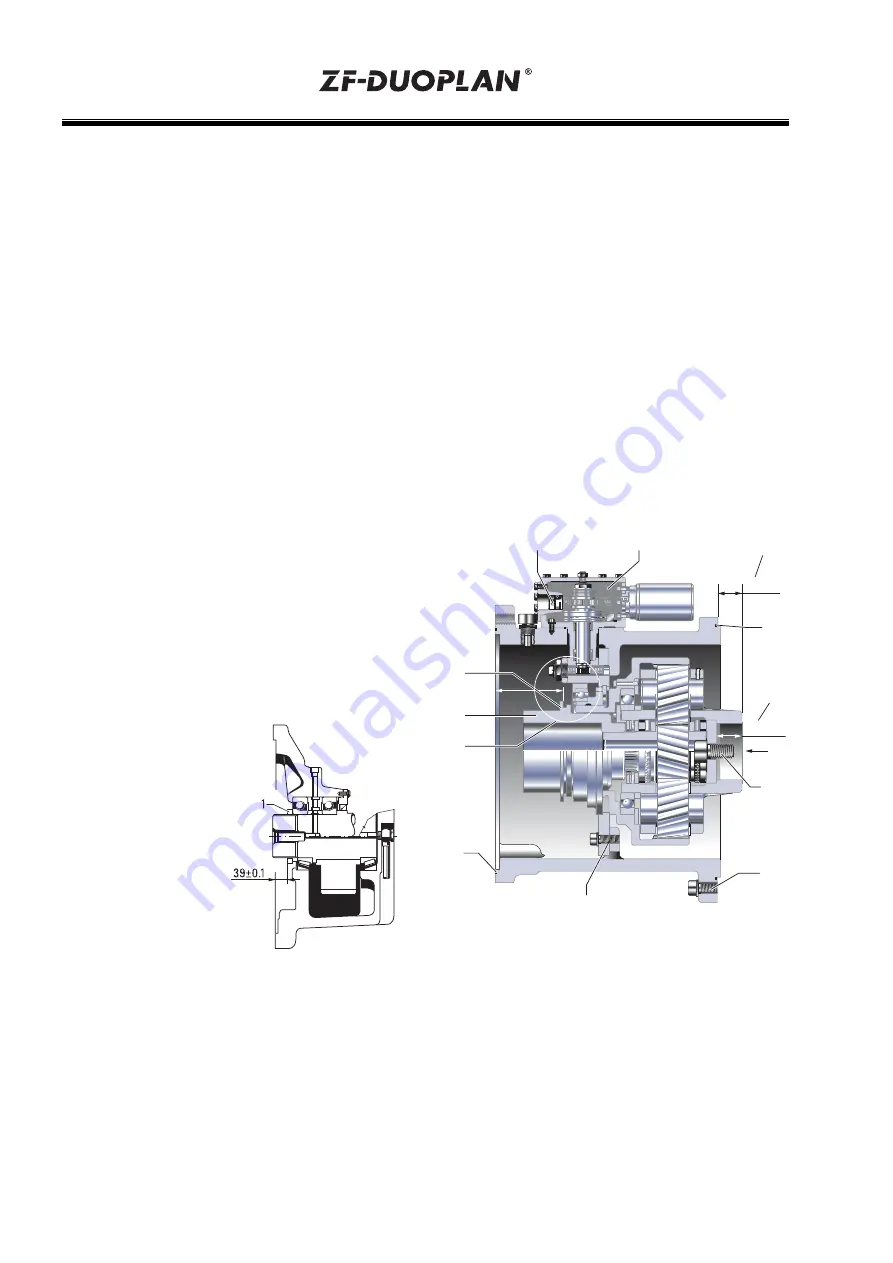
Operating
Instructions
Initial installation
2K2100 with STW
3.3
Mounting of 2K2100 without STW (spur
gear stage) on motor/gearbox
If the 2K2100 without output (without spur gear
stage) is supplied, mount the gearbox as follows.
Clean the flange faces on the gearbox housing and
the machine, check for unevenness and, if
necessary, skim with an oil stone.
First check the following dimensions (see
diagram):
A: 39 ± 0.1 mm is required on the input shaft in
order to allow bracing of the planetary gear carrier
with the machine bearings or spacer ring (1).
B: 41 – 0.5 mm; length of the profile in the
planetary gear carrier
Installation:
14
Slide the planetary gear carrier (profile
N90x2x30x44x9H) with ring gear onto the shaft
with the profile W90x2x30x44x9k. Bolt the
planetary gear carrier using the pan head screw
"D" with hexagon socket head (M24x2x60, with
bore).
Tightening torque: 420 Nm.
023648
Insert the O-ring "C" into the groove, using
standard grease to affix it if necessary. First
position the gearbox housing with the pan head
screws (13xM16x*) "F" and then tighten the
screws diagonally/alternately in several stages
until the final torque (195 Nm) is reached.
Undo the brake disc bolts. The shift mechanism
must be in 1st gear (4:1). Centering the brake disc
relative to the sliding sleeve can influence the
gear change.
NOTE:
The shift mechanism must be in 1st gear (position
S; 4:1). As a result, the sliding sleeve is also
guided. The gearing should be greased to make
installation easier.
A
39.000
41.000
C
B
I
D
F
H
R
P
M
S
T
G
N1
023649
* (not part of ZF scope of supply)