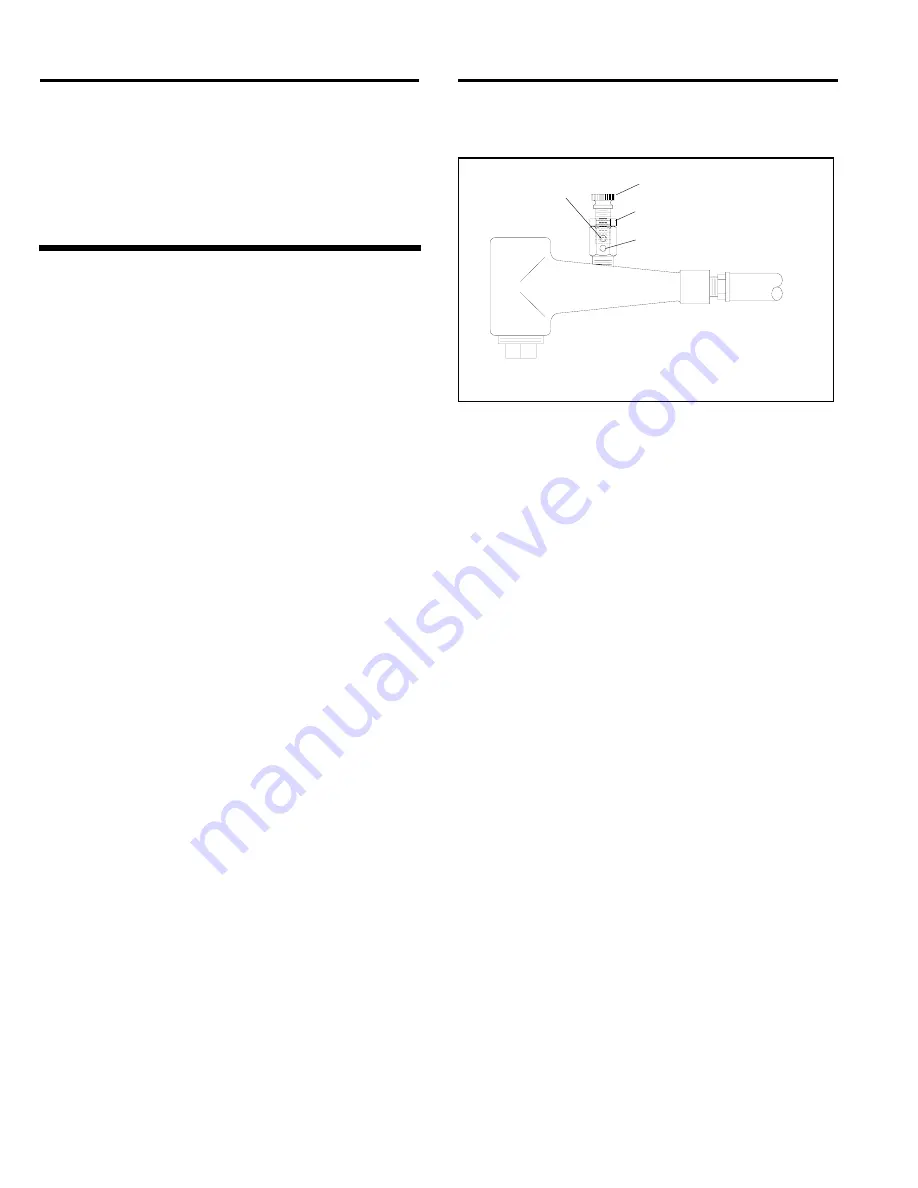
INEX SUCTION BLAST CABINET with 300 CFM RECLAIMER
Page 6
© 2005 CLEMCO INDUSTRIES CORP.
•
www.clemcoindustries.com
•
Manual No. 21803 Rev. D 03/05
3.5 Blasting
Technique
3.5.1
Blasting technique is similar to spray painting
technique. Smooth continuous strokes are most
effective. The distance from the part affects size of blast
pattern. Under normal conditions, hold the nozzle
approximately 3" to 6" from the surface of the part.
4.0 ADJUSTMENTS
4.1 Blasting
Pressure
4.1.1
The pilot regulator, located in the light shield,
enables the user to adjust blasting pressure to suit the
application. The suitable pressure for most purposes is
80 psi. Lower pressures may be used for delicate work.
In all cases, highest production can be achieved only
when pressure is carefully monitored.
4.1.2
To adjust, unlock the knob, and turn it clockwise
to increase pressure or counter-clockwise to decrease
pressure. Pressure will usually drop from closed-line
pressure when blasting is started. Once operating
pressure is set, lock the knob to maintain the setting.
4.2 Air
Jet
Adjustment
4.2.1
The air jet should be screwed 4-1/2 to 5 full
turns into the gun body. Doing so will leave 3-1/2 to 4
threads exposed past the lock nut. Tighten the lock nut
to hold the jet in place. See Section 8.1 or 8.3 for
optional adjusting tool.
4.3
Media/Air Mixture, Figure 4
4.3.1
Check the media stream for correct media/air
mixture; media flow is smooth and appears as a light mist
coming from the nozzle.
4.3.2
If media does not flow smoothly, loosen the
locking nut, and adjust the metering screw until the upper
holes in the metering stem are closed-off, and the lower
holes are fully open. See Figure 4. This adjustment is a
starting point.
4.3.3
If pulsation occurs in the media hose, either media
is damp and caked, or not enough air is entering the
media stream. While blasting, loosen the locking nut and
slowly turn the adjusting screw out (counterclockwise
when viewed from the top) until the media flows smoothly.
Tighten the locking nut finger-tight to maintain the setting.
4.3.4
If media flow is too light, decrease air in the
mixture by turning the metering screw in (clockwise when
viewed from the top) covering more of the holes so less air
enters the media hose. Tighten the locking nut finger-tight
to maintain the setting.
Figure
4
4.4
Static Pressure (dry filter models only)
4.4.1
Correct static pressure requirements vary with
size, weight and type of media.
4.4.2
Adjust static pressure by opening (handle
horizontal) or closing (handle vertical) the damper. The
damper is located on the inlet on dry. If the damper is
not opened enough, the reclaimer will not remove fines,
resulting in dusty media, poor visibility, and possible
media blockage in the conveying hose. If the damper is
opened too far, it may cause carryover (usable media
carried into the dust collector) and result in excessive
media consumption. Open only as far as necessary to
obtain a balance of dust removal without media
carryover.
4.4.3
A manometer is useful when adjusting or
monitoring static pressure. The optional manometer kit is
listed under Optional Accessories in Section 8.1. The
following are static pressure starting points for given
media. Static pressure may need to be lower with finer
media, higher with coarser media.
Glass Bead No. 8 to 13 ..................................... 2-1/2 - 3"
Alox. 60 & coarser ................................................... 4 - 5"
Alox. 80 & finer .................................................. 2-1/2 - 3"
4.4.4
If the damper has been adjusted and carryover
or excessive dust in the media continues to be a
problem, the optional adjustable vortex cylinder, which is
standard on pull through reclaimers, may help retain
media. The vortex cylinder is usually required only when
using 200 mesh and finer media, or lightweight media.
See Section 4.5, and Accessories in Section 8.1.
Adjusting Screw
Locking Nut
Lower holes fully open
Upper holes
fully Closed