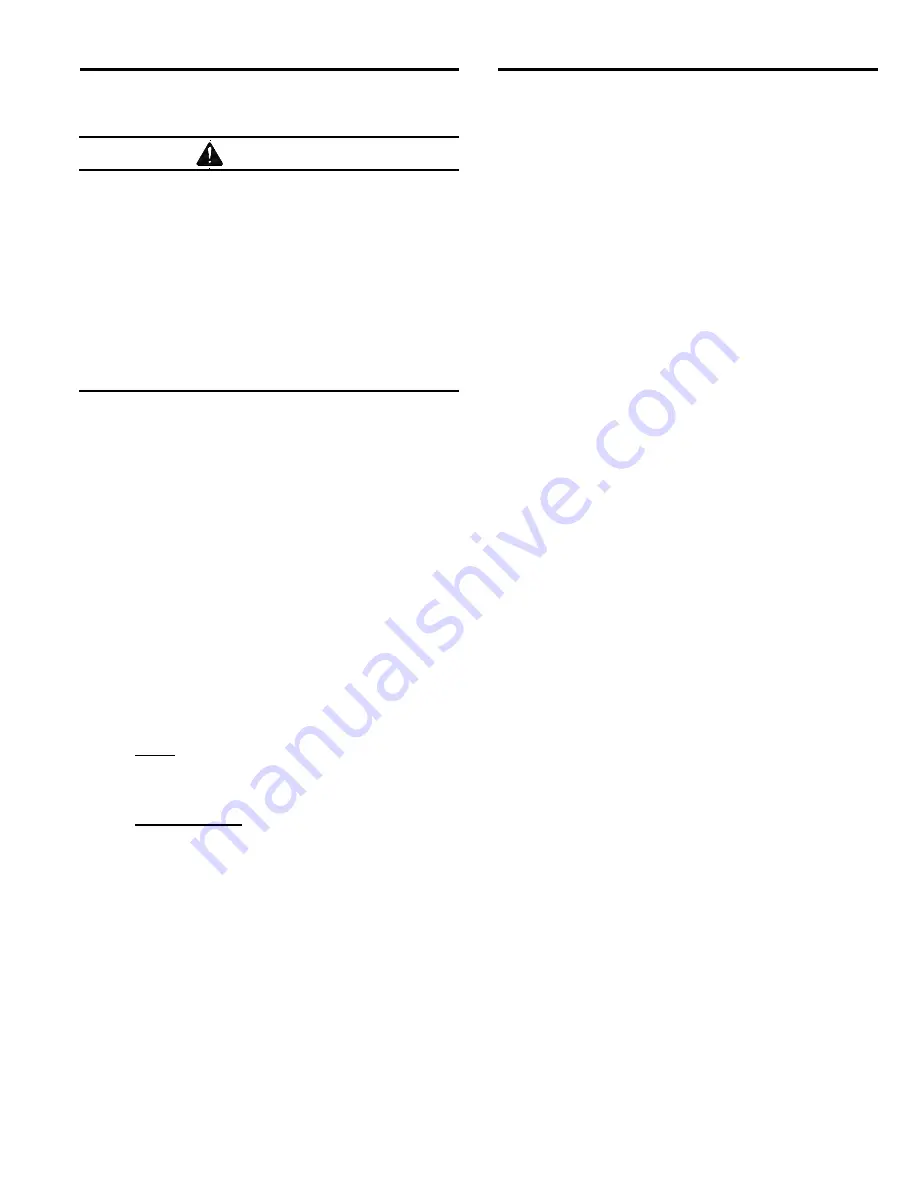
AEROLYTE 6060A and 7070A G2 PRESSURE CABINETS
Page 21
© 2016 CLEMCO INDUSTRIES CORP.
www.clemcoindustries.com
Manual No. 27789 Rev. A, 10/16
8.0 TROUBLESHOOTING
WARNING
To avoid serious injury, observe the following
when troubleshooting.
Turn OFF the air, and lockout and tagout the
air supply.
When checking the controls requires air,
always enlist the aid of another person to:
•
Hold the nozzle securely.
•
Operate the foot pedal.
Never bypass the foot pedal or wedge it in
the operating position.
Never override the door interlock system.
8.1 Poor
visibility
8.1.1
Dirty filter cartridges. Refer to the reverse-pulse
dust collector manual to adjust pulse pressure and
pulse sequence.
8.1.2
Exhauster motor not operating. Check voltage
to motor and motor wiring.
8.1.3
Check rotation of exhauster motor; the motor
should rotate as indicated by the arrow on the housing.
If it does not rotate in the proper direction,
lockout and
tagout electrical power
and switch the motor leads as
shown on the motor plate. Refer to Section 2.11.
8.1.4
Using friable media that rapidly breaks down or
using media that is too fine or worn out.
8.1.5
Outlet damper closed too far restricting air
movement through the cabinet. Adjust static pressure
per Section 5.3.
8.1.6
Cabinet air-Inlet damper closed too far restricting
air movement in the cabinet. Adjust damper per Section
2.13 and 5.6.
8.1.7
Reclaimer door open.
8.1.8
Hole worn in flex hose between cabinet hopper
and reclaimer inlet or between the reclaimer and dust
collector. Replace hose and route it with as few bends
as possible to prevent wear.
8.1.9
Obstruction in flex hose between the cabinet
hopper and reclaimer inlet.
8.1.10
Nozzle worn. Replace the nozzle when its
orifice diameter has increased by 1/16".
8.2
Abnormally high media consumption
8.2.1
Fill door on reclaimer open or worn door gasket.
Air entering the reclaimer around the door will cause
media carry-over to the dust collector. DO NOT operate
unless all doors are closed.
8.2.2
Dust collector damper open too far. Adjust static
pressure per Section 5.3.
8.2.3
Media may be too fine or worn-out.
8.2.4
Using friable media that rapidly breaks down.
8.2.5
Blast pressure too high for the media, causing
media to break down.
8.2.6
Hole worn in reclaimer or leak in reclaimer
seams. Check entire reclaimer for negative-pressure
leaks.
8.2.7
Metering valve requires adjustment. Adjust
media flow per Section 5.2.
8.2.8 E
xternally-adjustable vortex cylinder requires
adjustment, refer to Section 5.4.
8.3
Reduction in blast cleaning rate
8.3.1
Low media level. Check media level and refill if
low.
8.3.2
Media/air mixture out of adjustment. Adjust
metering valve per Section 5.2.
8.3.3
Reduced air pressure. This may be caused by a
malfunctioning regulator, a dirty filter element in air filter,
partially closed air valve, leaking air line, or other air
tools in use.
8.3.4
Blockage in nozzle. Blockage may occur as a
result of a missing debris screen.
8.3.5
Moist media. Frequent bridging or blockage in
the area of the metering valve can be caused by
moisture. See Section 8.5.
8.3.6
Air leaking through the outlet valve, reducing
blast pressure and control pressure to media metering
valve. Inspect outlet valve for leaks.
8.4 Plugged
nozzle
8.4.1
A damaged or missing reclaimer screen will
allow large particles to pass and block the nozzle.
Inspect screen and replace or re-install as necessary.