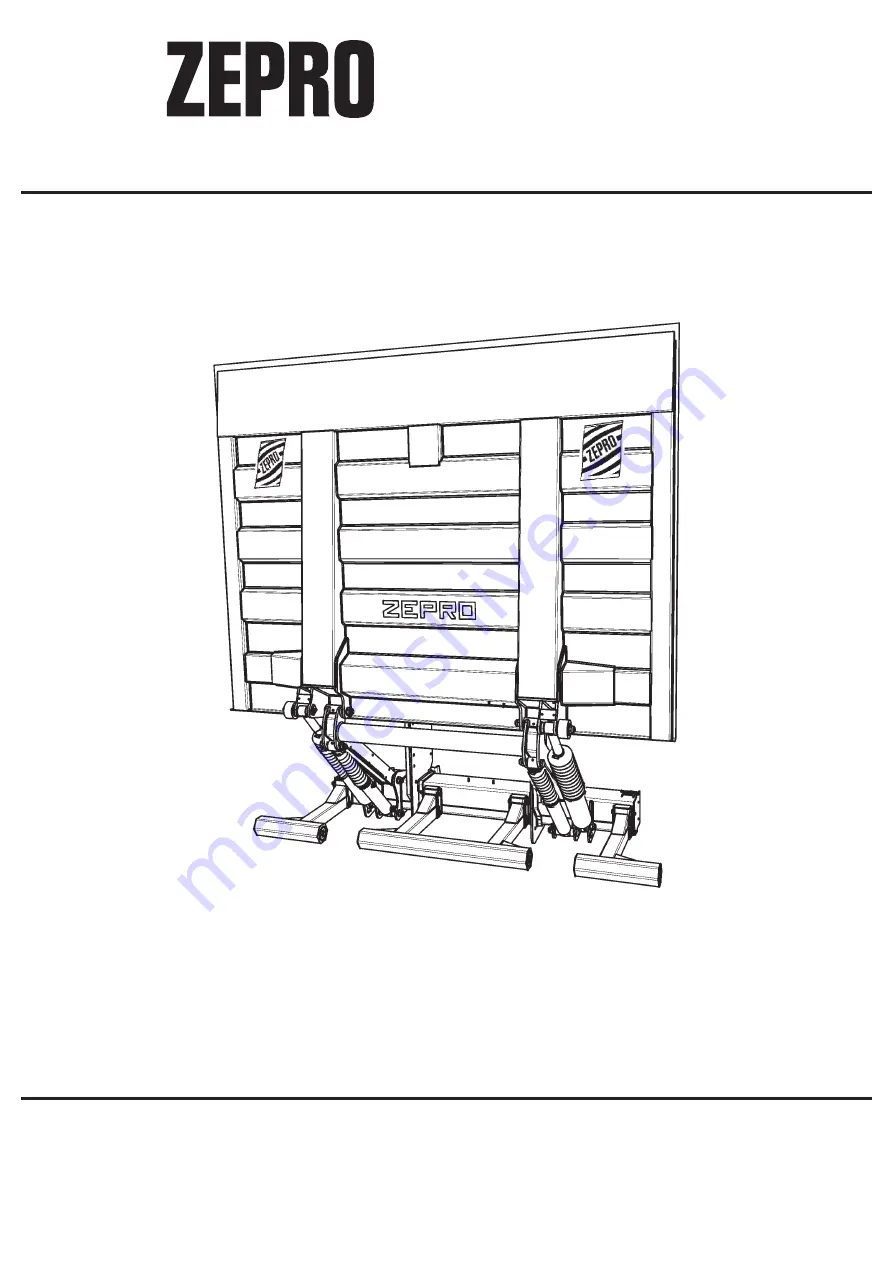
ZHD 3000-150
Sales
Mossvägen 8, 641 49 KATRINEHOLM, SWEDEN
Telephone:
+46 150 - 489550
Telefax:
+46 150 - 489551
E-mail:
Internet: www.zepro.com
Factory
Allévägen 4, 840 73 BISPGÅRDEN, SWEDEN
Telephone:
+46 696 - 17200
Telefax:
+46 696 - 17242
E-mail:
Internet: www.zepro.com
2020-05-14
72689TL
INSTALLATION INSTRUCTION
Z-LYFTEN PRODUKTION AB