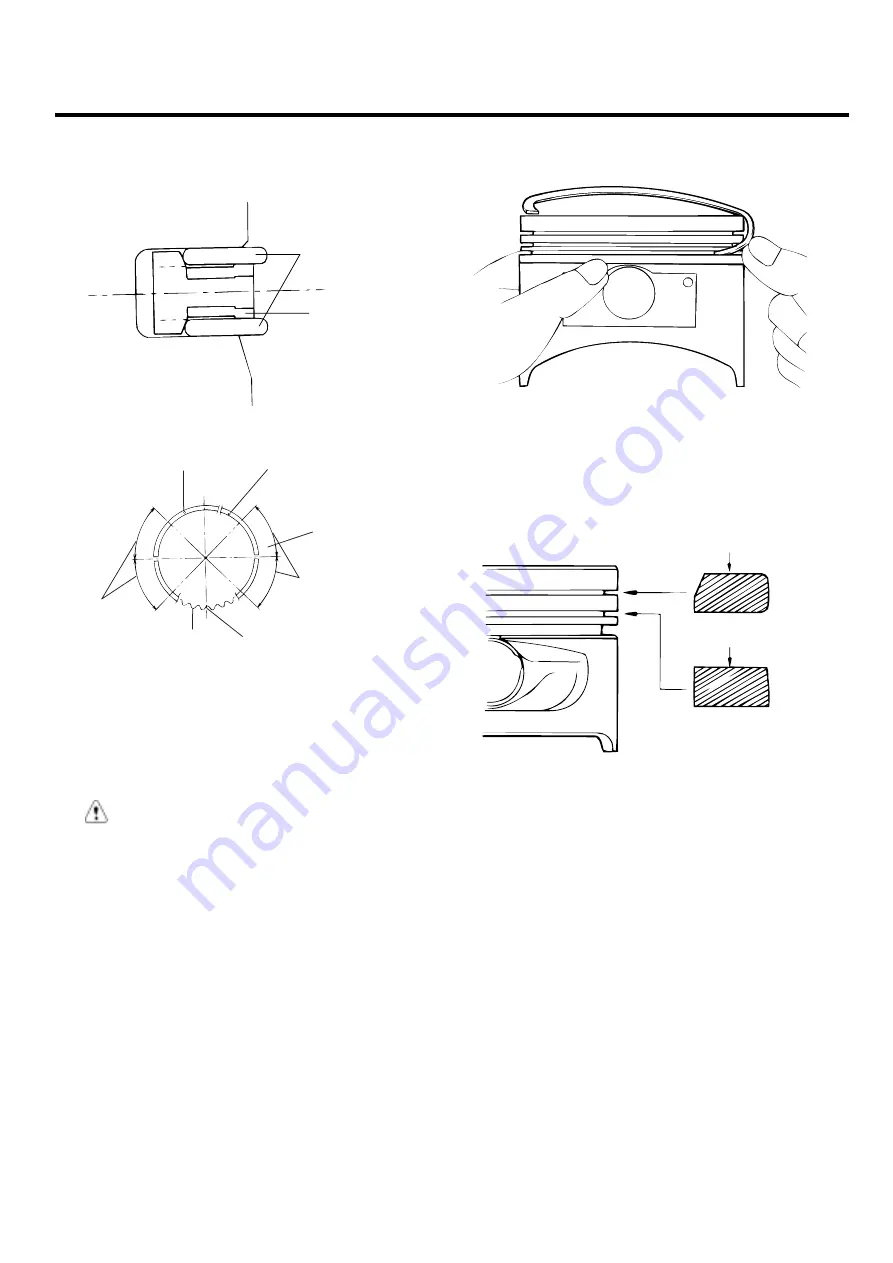
MAIN MOVING SYSTEM
EM -55
REASSEMBLY
ECCF87EF
1.
Install the spacer.
Piston upper
Piston lower
Side rail
Spacer
ECA9082A
Upper side rail
45˚
45˚
45˚
45˚
Lower side rail
90˚ Position
from the gap
of No. 2 ring
Gap position of
lower side rail
Gap position of spacer
Gap position
of upper
spacer
Spacer
EDJA490A
2.
Install the upper side rail. To install the side rail, first
put one end of the side rail between the piston ring
groove and spacer, hold it firmly, and press down with
a finger on the portion to be inserted into the groove
(as illustrated).
CAUTION
Do not use a piston ring expander when installing
side rail.
3.
Install the lower side rail by the same procedure de-
scribed in Step 2.
ECA9380B
4.
Apply engine oil around the piston and piston grooves.
5.
Using a piston ring expander, install the No.2 piston
ring.
6.
Install the No. 1 piston ring.
No.1
No.2
Berrel type
Inside bevel
Taper type
EDDA037B
7.
Position each piston ring end gap as far away from
its neighboring gaps as possible. Make sure that the
gaps are not positioned in the thrust and pin direc-
tions.
ZENITH POWER PRODUCTS - 416